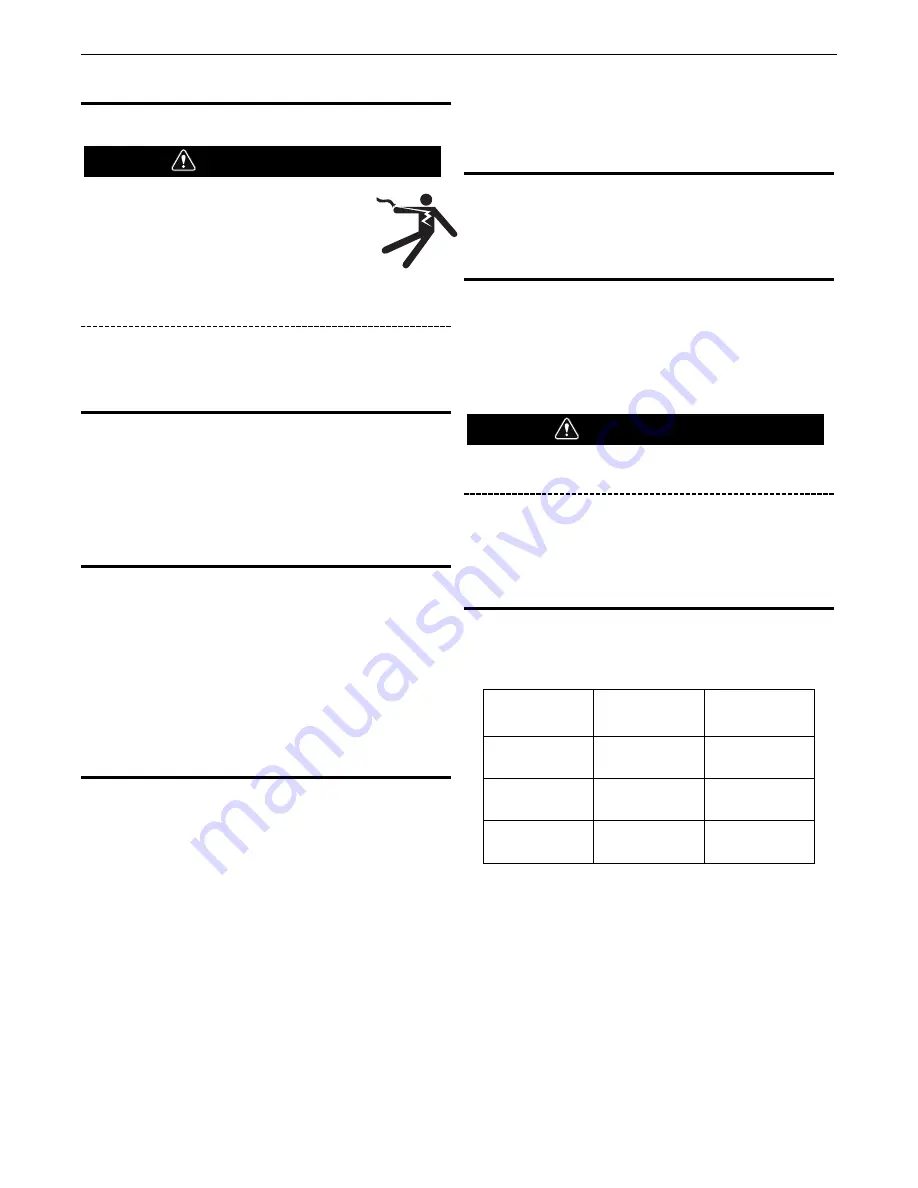
MAINTENANCE
Safety Precautions
ELECTRIC SHOCK can kill.
•
Have an electrician install and service this
equipment.
•
Turn the input power OFF at the fuse box
before working on equipment
•
Do not touch electrically hot parts.
See additional warning information throughout
this Operator’s Manual
GENERAL MAINTENANCE
In extremely dusty locations, dirt may clog the air passages
causing the welder to run hot. Blow dirt out of the welder with
low-pressure air at regular intervals to eliminate excessive dirt
and dust build-up on internal parts.
The fan motors have sealed ball bearings which require no
service.
DRIVE ROLLS AND GUIDE PLATES
After every coil of wire, inspect the wire drive mechanism. Clean it
as necessary by blowing with low pressure compressed air. Do
not use solvents for cleaning the idle roll because it may wash the
lubricant out of the bearing.
All drive rolls are stamped with the wire sizes they will feed. If a
wire size other than that stamped on the roll is used, the drive roll
must be changed.
For instructions on replacing or changing drive roll, see “Wire
Drive Rolls” in Operation section.
CONTACT TIP AND GAS NOZZLE INSTALLATION
1. Choose the correct size contact tip for the electrode being
used (wire size is stenciled on the side of the contact tip) and
screw it snugly into the gas diffuser.
2. Screw the appropriate fixed gas nozzle fully onto the diffuser.
Either the standard .50" (12.7 mm) flush nozzle or other
optional flush or recessed (spray arc) nozzle sizes may be
used. (Refer to www.lincolnelectric.com)
3. If using optional adjustable slip-on nozzles. (Refer to
www.lincolnelectric.com)
•
Be sure the nozzle insulator is fully screwed onto the
gun tube and does not block the gas holes in the
diffuser.
•
Slip the appropriate gas nozzle onto the nozzle insulator.
Either a standard .50" (12.7 mm) or optional .62" (15.9
mm) I.D. slip-on gas nozzle may be used and should be
selected based on the welding application.
•
Adjust the gas nozzle as appropriate for the GMAW
process to be used. Typically, the contact tip end should
be flush to .12" (3.2 mm) extended for the short-
circuiting transfer process and .12" (3.2 mm) recessed
for spray transfer.
GUN TUBES AND NOZZLES
1. Replace worn contact tips as required.
2. Remove spatter from inside of gas nozzle and from tip after
each 10 minutes of arc time or as required.
GUN CABLE CLEANING
To help prevent feeding problems, clean cable liner after using
approximately 300 pounds (136 kg) of electrode. Remove the
cable from the wire feeder and lay it out straight on the floor.
Remove the contact tip from the gun. Using an air hose and only
partial pressure, gently blow out the cable liner from the gas
diffuser end.
Excessive pressure at the beginning of the cleaning
procedure may cause the dirt to form a plug.
Flex the cable over its entire length and again blow out the cable.
Repeat this procedure until no further dirt comes out. If this has
been done and feed problems are experienced, try liner
replacement, and refer to trouble shooting section on rough wire
feeding.
LINER REMOVAL AND REPLACEMENT
NOTE: Changing the liner for a different wire size requires
replacement of the gas diffuser per Table D.1 to properly secure
the different liner.
WARNING
CAUTION
Diameter of
Electrodes Used
Replacement
Liner Part Number
Size Stencilled on
End of Liner
Bushing
.025”-.030" Steel
(0.6-0.8 mm)
KP42-25-15
.030” (0.8 mm)
.035”-.045" Steel
(0.9-1.1 mm)
KP42-4045-15
.045” (1.1 mm)
3/64" Aluminum
(1.2 mm)
KP42N-3545-15
3/64" (1.2 mm)
D-1
MAINTENANCE
POWER MIG
®
260