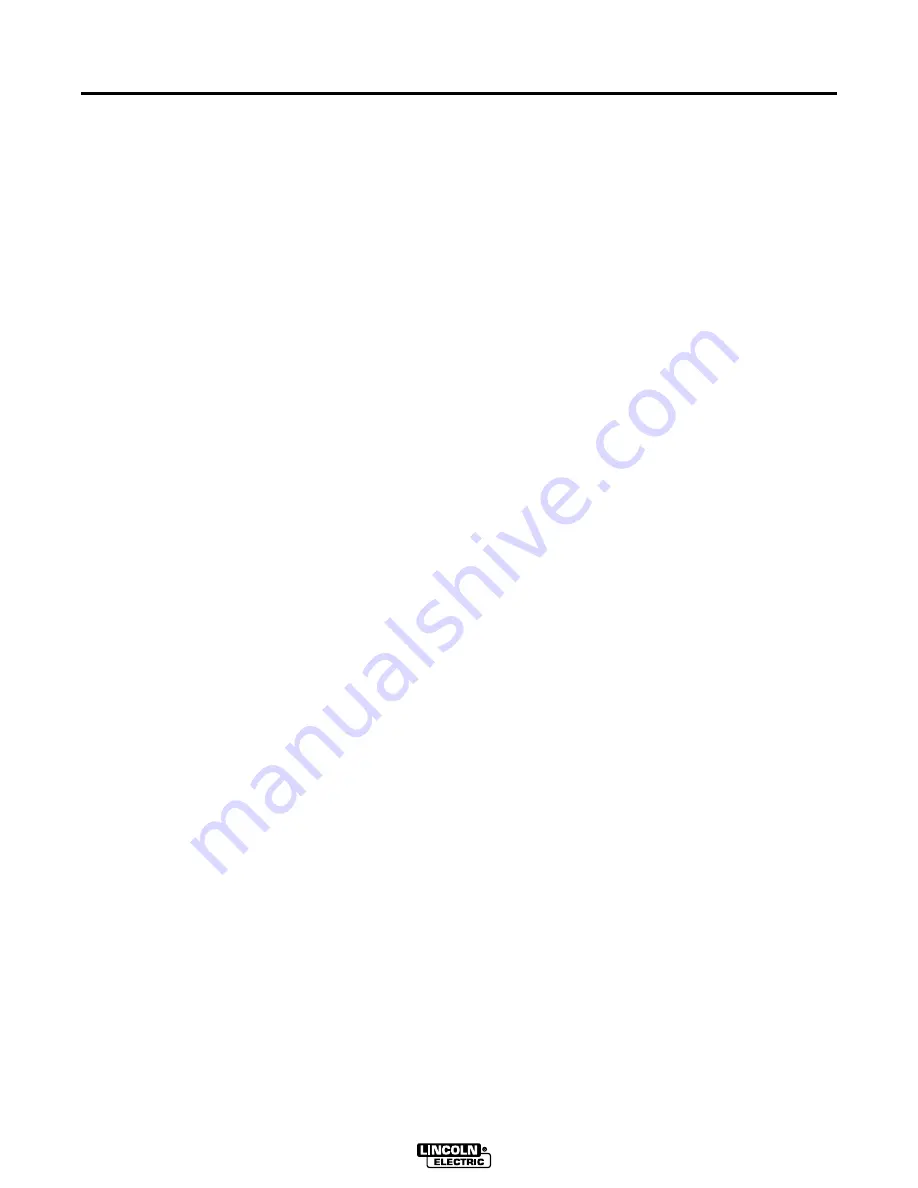
TABLE OF CONTENTS
- ELECTRICAL DIAGRAMS SECTION -
NA-3 AND NA-4
Electrical Diagram Section . . . . . . . . . . . . . . . . . . . . . . . . . . . . . . . . . Section G
Wiring Diagram (NA-3) . . . . . . . . . . . . . . . . . . . . . . . . . . . . . . . . . . . . . G-2
Wiring Diagram (NA-4) . . . . . . . . . . . . . . . . . . . . . . . . . . . . . . . . . . . . . G-3
Operating Schematic (NA-3) . . . . . . . . . . . . . . . . . . . . . . . . . . . . . . . . . G-4
Operating Schematic (NA-4) . . . . . . . . . . . . . . . . . . . . . . . . . . . . . . . . . G-5
Logic PC Board (G1379-2 & above) Schematic . . . . . . . . . . . . . . . . . . . G-6
Variable Voltage PC Board (L5394-2 & above) Schematic . . . . . . . . . . . G-7
Control PC Board (L5224-5 & above) Schematic . . . . . . . . . . . . . . . . . . G-8
Start PC Board (L9917-1 & above) Schematic . . . . . . . . . . . . . . . . . . . . G-9
Crater Fill PC Board (L5222-2 & above) Schematic . . . . . . . . . . . . . . . . G-10
G-1
G-1
Содержание NA-3S
Страница 6: ...NOTES v v NA 3 AND NA 4 ...
Страница 47: ...NOTES B 18 B 18 NA 3 AND NA 4 ...
Страница 53: ...NOTES C 6 C 6 NA 3 AND NA 4 ...
Страница 91: ...NOTES F 26 F 26 NA 3 AND NA 4 ...
Страница 101: ...NOTES NA 3 AND NA 4 ...