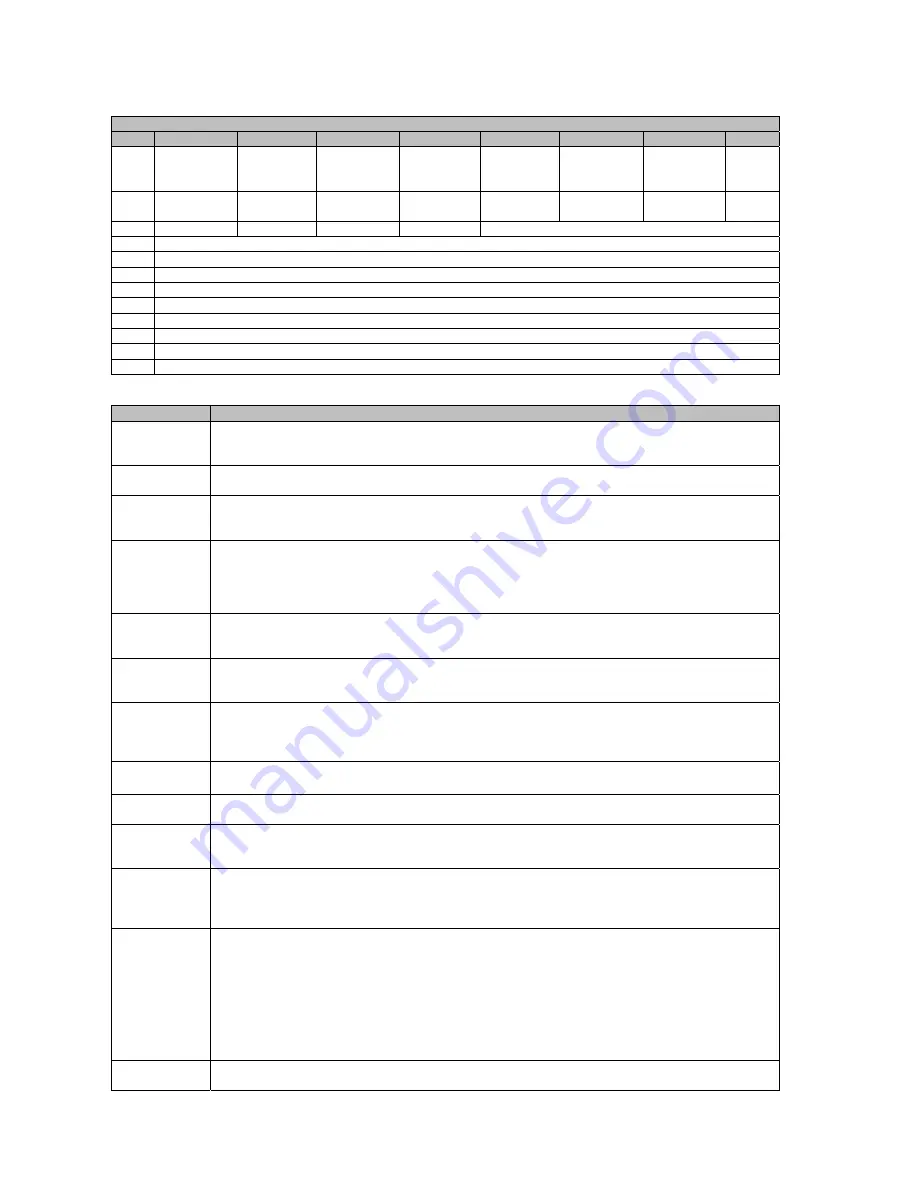
English
English
10
I/O Format
I/O from Welder to Master
Cyclic I/O From Welder to Master
Byte B7
B6
B5
B4
B3
B2
B1
B0
0 Misc
Module
Fault
Wire Stick
WC Fault
Water
Fault
WD Fault
Gas Fault
Touch
Sense
Arc
Detect
1
Anybus
Fault
PM Limit
PM Fault
Weld
Complete
Limit Error
2
Weld Sequencer Current State
3
4
Voltage Feedback, Low Byte (In Volts with 1 implied decimal places)
5
Voltage Feedback, High Byte
6
Current Feedback, Low Byte (In Amps with 1 implied decimal places)
7
Current Feedback, High Byte
8
Wire Drive Motor Current, Low Byte (Signed value In Amps with 2 implied decimal places)
9
Wire Drive Motor Current, High Byte
10
Wire Feed Speed Feedback, Low Byte
11
Wire Feed Speed Feedback, High Byte
I/O Bit Description to Master
Item
Description
Arc Detect
A True value indicates sufficient arc voltage and arc current have been detected. Arc voltage and
arc current levels are addicted to mode. When there is no longer sufficient Arc current and Arc
voltage then go to False.
Touch Sensed A True value indicates that the Touch Sense detected a short between the work piece and the
electrode.
Gas Fault
A True value indicates there is a failure in the gas controller. If a fault occurs the weld Power Wave
will turn the output off and welding will not be possible until the problem is corrected and the fault
is cleared.
WD Fault
Asserted when there is a fault in the Wire Drive. This fault occurs also when Shutdown input is
open on the external I/O connector Ref. Power Wave / Power Feed Wire Feeder Interconnections
section describing External I/O Connector in the Operator’s Manual. If a fault occurs the weld
Power Wave will turn the output off and welding will not be possible until the problem is corrected
and the fault is cleared.
Water Fault
True when Arclink Water Cooler reports an error. If a fault occurs the weld Power Wave will turn
the output off and welding will not be possible until the problem is corrected and the fault is
cleared.
WC Fault
True when there is a Weld Controller fault. Refer to “Troubleshooting” in the Operator’s Manual
for a list of possible errors. If a fault occurs the weld Power Wave will turn the output off and
welding will not be possible until the problem is corrected and the fault is cleared.
Wire Stick
True value indicates that after the welding output is turned off there is a short between the
electrode and the workpiece. This will stay true until the welding output is turned on and the error
is cleared or if a Touch Sense Command is asserted and the short has been cleared. This check
is disabled by default and be enabled using the option “Enable Wire Stick Check”.
Misc Module
Fault
True value indicates that a module, like the Advance Module, STT Switch, High Frequency Switch
has a fault.
Limit Error
Indicates that one of the Welding Job Parameters is out of limits. This will not stop welding
process.
Weld
Complete
Indicates that the weld has completed (subsequent to the trigger going false) including any
downslope, crater, burnback and postflow times. Goes false when the next weld begins (trigger
going true).
PM Fault
This bit is used to indicate that the Production Monitoring object is faulty, a common cause is that
the Production Monitoring object detected a limit error while welding and the Out of limit action
was set to Alarm Latch. This faulty condition must be cleared before welding; toggling the PM Flt
Reset bit to the welder should clear this condition.
PM Limit
This bit is used to indicate that the Production Monitoring (PM) object detected a limit error. This
bit is clear automatically when the trigger input goes on or when the PM Flt Reset bit to the welder
goes on.
This bit is basically just a status item indicating a PM limit fault occurred, but depending on how
PM is configured, other behavior can occur when this bit goes on. If PM is set to Fault System,
then PM will shut the Power Source output off automatically when a limit error occurs, this will
cause the LGA sequencer to fault and stop welding. If PM is set to Alarm Latch and a limit error
occurs, then the PM object will fault after the weld is over and welding can not resume until the PM
fault is cleared (see the PM Fault bit).
Anybus Fault
This bit is used to indicate that the Anybus module has a fault. This includes selecting a job with
invalid Workpoint or Trim units, or selecting an invalid Job number.