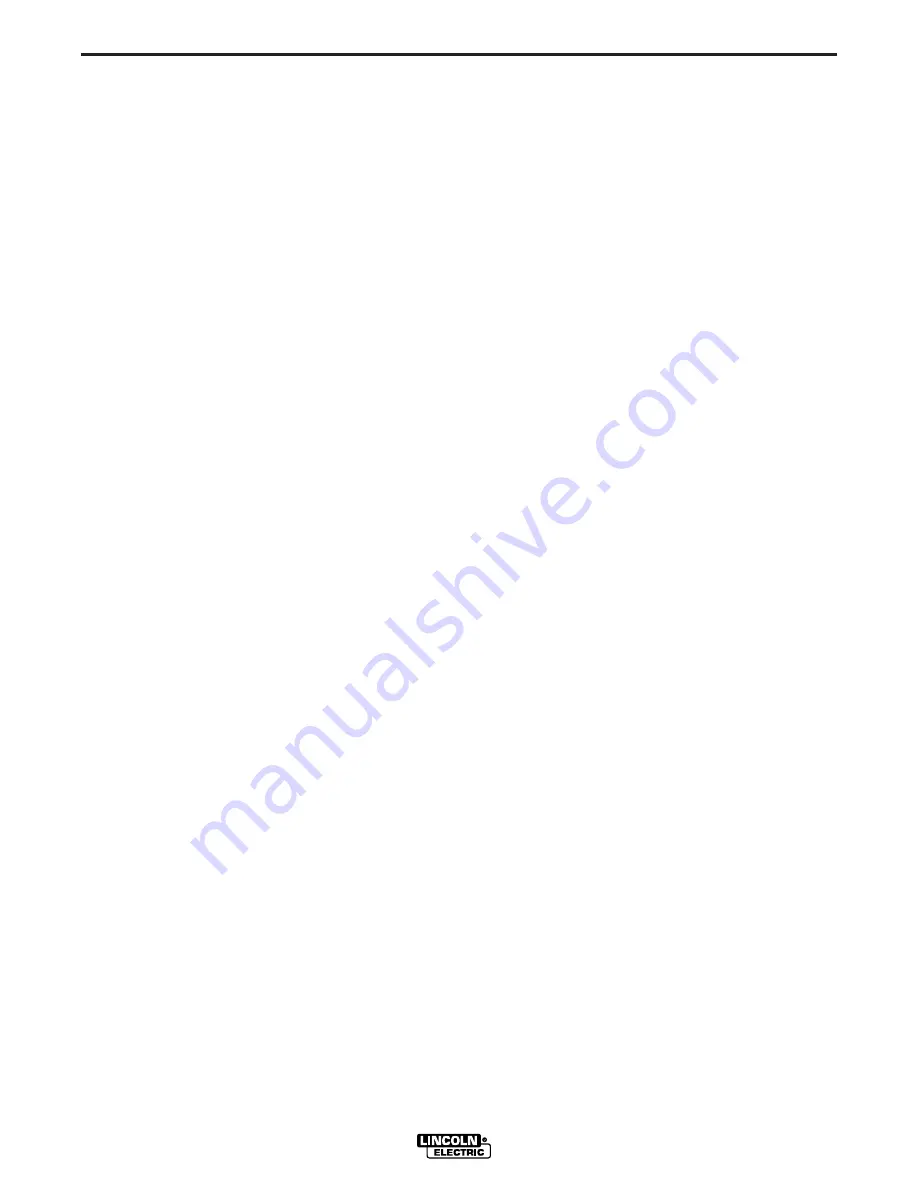
B-3
OPERATION
B-3
6. ARC FORCE
-
This control functions in CC Stick SMAW
modes to adjust the Arc Force. The arc is soft at the mini-
mum settings and more forceful or driving at the maximum
settings. Higher spatter levels may be present at the maxi-
mum settings.
Full range is from -10(Soft) to +10(Crisp)
7. OUTPUT TERMINALS
-
These quick disconnect termi-
nals provide connection points for the electrode and work
cables. Refer to
Output Connection
in the Installation chap-
ter for proper cable sizes. For positive polarity welding con-
nect the electrode cable to the positive terminal and the work
cable to the negative terminal. To weld negative polarity
reverse the electrode and work cables.
8. THERMAL SHUTDOWN INDICATOR
-
This light will
illuminate if an internal thermostat has been activated.
Machine output will return after the internal components
have returned to a normal operating temperature. See
Thermal Protection
later in this Operation chapter.
9. 6-PIN REMOTE RECEPTACLE
(Refer to
Output Connection
in the Installation chapter.)
10. POWER LIGHT
- This Light will illuminate when the
power switch is in the “ON” position.
CONSTANT CURRENT PROCESSES
MANUAL ARC WELDING (STICK)*
The Invertec may be utilized as a manual DC arc welder with
the electrode cable, work cable, and electrode holder being the
only equipment required.
AIR CARBON ARC CUTTING*
Air carbon arc cutting may be performed with the Invertec within
its output rating using 3/16” diameter carbon rods. Output
cables, an air carbon arc electrode cable assembly, and a
source of compressed air are required.
TIG WELDING*
The Invertec V275-S is capable of touch start TIG welding. An
electrode cable, work cable, TIG torch, and gas supply with reg-
ulator are required. Refer to
Accessories
section of this manu-
al.
Touch starting is done as follows:
1. Place the shield cup edge on the work piece.
2. Rock the tungsten down to touch.
3. Trigger the output, if using remote control.
4. Gently rock back the tungsten from the workpiece.
Note
: The short circuit current is limited to 20 amps to aid in
touch starting. Panel output control becomes the current
limit setting when in remote control.
* Note:
Operating this machine with the output control set to
maximum may cause the machine to phase back and the arc
to go out. This occurs because the welding current exceeded
300 amps and the machine’s protection circuitry activated.
Turn the output control down to correct this condition.
PARALLEL OPERATION
The Invertec’s are operable in parallel. For best results, the cur-
rents of each machine should be reasonably well shared. As an
example, with two machines set up in parallel for a 300 amp
procedure, each machine should be set to deliver approximately
150 amps, not 200 amps from one and 100 amps from the
other. This will minimize nuisance feedback conditions. In gen-
eral, more than two machines in parallel will not be effective due
to the voltage requirements of procedures in that power range.
To set machine outputs, start with output control pots and arc
force pots in identical positions. Adjust outputs and arc forces to
maintain current sharing while establishing the proper output
current.
OVERLOAD PROTECTION
The machine is electrically protected from producing high output
currents. Should the output current exceed 300A, an electronic
protection circuit will reduce the current to less than 200A. The
machine will continue to produce this low current until the pro-
tection circuit is reset. Reset occurs when the output load is
removed.
Note:
When TIG welding with the Output Knob at or above 275
Amps the Arc may go out.
THERMAL PROTECTION
Thermostats protect the machine from excessive operating tem-
peratures. Excessive temperatures may be caused by a lack of
cooling air or operating the machine beyond the duty cycle and
output rating. If excessive operating temperature should occur,
the thermostats will prevent output voltage or current.
Thermostats are self-resetting once the machine cools suffi-
ciently.
FAN
The cooling fan on the V275-S operates once 15 amps of weld-
ing current is drawn and for 7 minutes after the output current
has stopped flowing.
The fan will also run anytime the machine has over heated.
POWER-UP SEQUENCE
At power up the thermal light (and Power light on codes 11164
and above) turns on and the fans run for approximately 3 sec-
onds. This is the pre-charge time for the main capacitors. After
this time the fans and thermal light turn off and the pre-charge
relay closes to apply full line power to the capacitors. At this
time the machine is ready to weld.
INVERTEC V275-S
Содержание Invertec V275-S
Страница 30: ...NOTES INVERTEC V275 S...
Страница 31: ...NOTES INVERTEC V275 S...