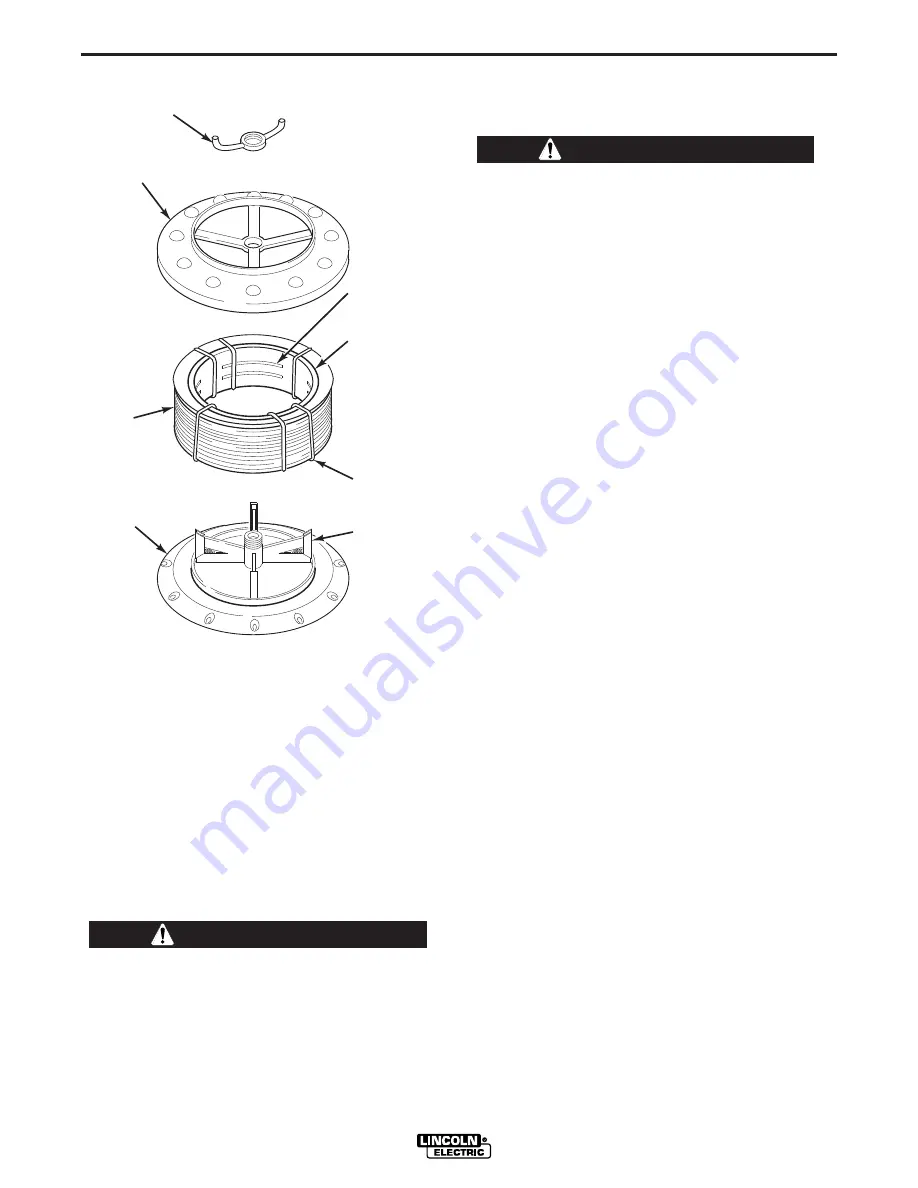
B-3
OPERATION
B-3
e. Press the gun trigger and push the electrode until
it
just
enters the drive roll.
When inching with gun trigger, the electrode and
drive mechanism are always “hot” to work and
ground.
---------------------------------------------------------------------
f. Inch the electrode through the gun.
IDLE ROLL PRESSURE SETTING
The idle roll pressure is set at the factory backed out
two turns from full pressure. This is an approximate
setting. The optimum idle roll setting can be
determined as follows:
1. Press end of gun against a solid object that is
electrically isolated from the welder output. Press
the gun trigger for several seconds.
2. If the wire “birdnests,” jams or breaks at the drive
roll, the idle roll pressure is too great. Back the
pressure setting out
1
⁄
2
turn, run new wire through
gun, and repeat above steps.
3. If the only result is drive roll slippage, shut off the
power source, then loosen the gun cable
clamping screw in the gearbox conductor block
and pull the gun cable forward about six inches.
There should be a slight waviness in the exposed
wire. If there is no waviness, the pressure is too
low. Increase the pressure setting
1
⁄
4
turn, lock the
gun cable in place and repeat the above steps.
LN-35
FIGURE B.1 – LOADING A 50 OR 60 LB COIL.
SPINNER
NUT
COVER
PLATE
COIL
REEL
SLOTS
CARDBOARD
COIL
LINER
TIE WIRE
SPRING
LOADED
ARM
LOADING WIRE DRIVE
a. Turn the reel or spool until the free end of the
electrode is accessible.
b. While tightly holding the electrode, cut off the bent
end and straighten the first six inches. Cut off the
first inch. (If the electrode is not properly
straightened, it may not feed or may not go into
the outgoing guide tube causing a “birdnest”.)
c. Insert the free end through the incoming guide
tube to the drive roll.
d. Turn on the welding power source.
The electrode circuit is electrically
“
hot
”
when the
power source is on.
------------------------------------------------------------------
WARNING
WARNING
Содержание IM812-A
Страница 25: ...NOTES LN 35 ...