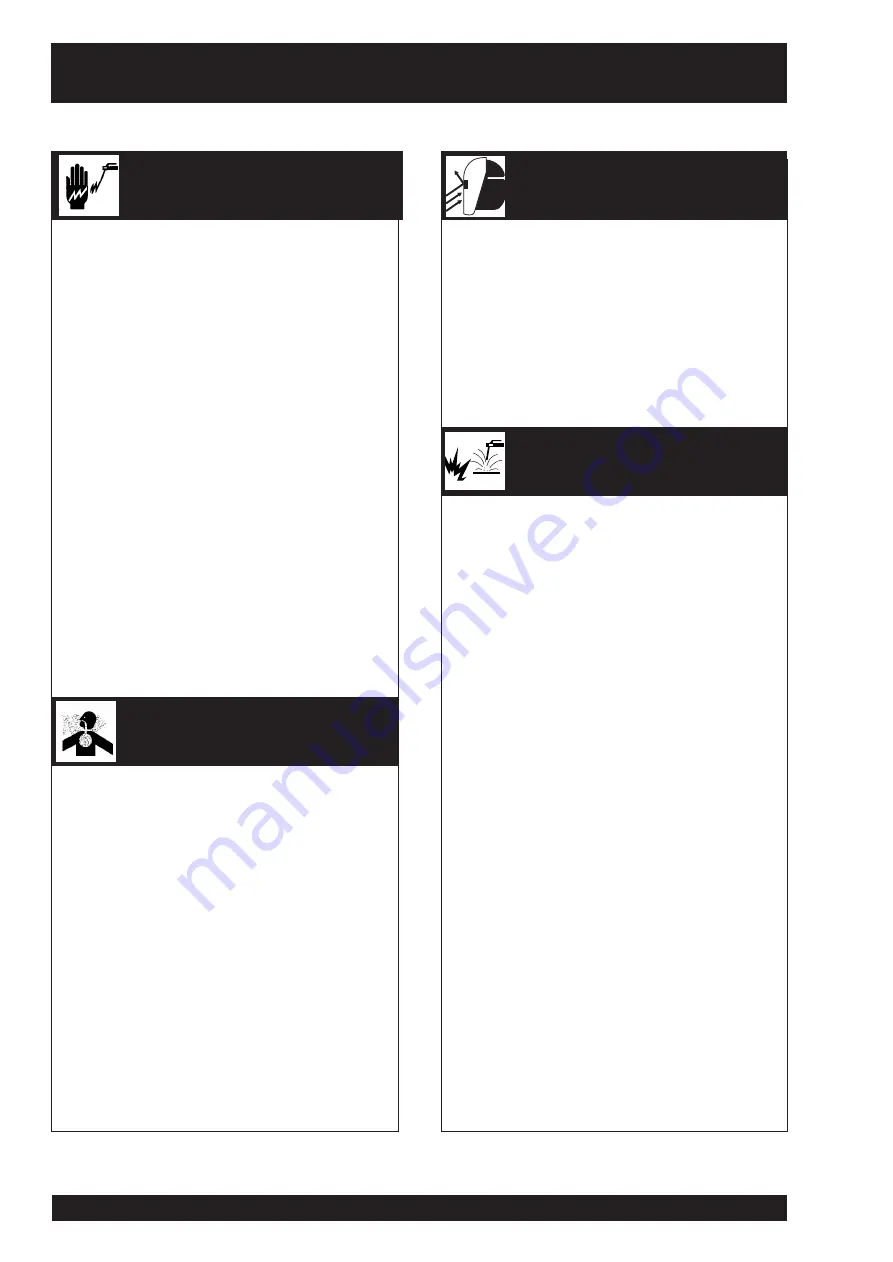
Page 2
Idealarc R3R 500-I & 600-I
IM 6000
PROTECT YOURSELF AND OTHERS FROM POSSIBLE SERIOUS INJURY OR DEATH. READ AND UNDERSTAND BOTH
THE SPECIFIC INFORMATION GIVEN IN THE OPERATING MANUAL FOR THE WELDER AND/OR OTHER EQUIPMENT
TO BE USED AS WELL AS THE FOLLOWING GENERAL INFORMATION.
ARC WELDING SAFETY PRECAUTIONS
1.
a.
The electrode and work (or ground) circuits are
electrically “hot” when the welder is on. Do not touch
these “hot” parts with your bare skin or wet clothing.
Wear dry, hole-free gloves to insulate hands.
b.
In semi-automatic and automatic wire welding, the
electrode, electrode reel, welding head and nozzle or
semi-automatic welding gun are also electrically “hot”.
c.
Insulate yourself from work and ground using dry
insulation. When welding in damp locations, on metal
framework such as floors, gratings or scaffolds, and
when in positions such as sitting or Lying, make certain
the insulation is large enough to cover your full area of
physical contact with work and ground.
d.
Always be sure the work cable makes a good electrical
connection with the metal being welded. The
connection should be as close as possible to the area
being welded.
e.
Ground the work or metal to be welded to a good
electrical (earth) ground.
f.
Maintain the electrode holder, work clamp, welding
cable and welding machine in good, safe operating
condition. Replace damaged insulation.
g.
Never dip the electrode holder in water for cooling.
h.
Never simultaneously touch electrically “hot” parts of
electrode holders connected to two welders because
voltage between the two can be the total of the open
circuit voltage of both welders.
i.
When working above floor level, protect yourself from
a fall should you get a shock.
j.
Also see items 4c and 6.
2.
a.
Welding may produce fumes and gases hazardous to
health. Avoid breathing these fumes and gases. When
welding, keep your head out of the fume. Use enough
ventilation and/or exhaust at the arc to keep fumes and
gases away from the breathing zone. When welding
on galvanised, lead or cadmium plated steel and other
metals which produce toxic fumes, even greater care
must be taken.
b.
Do not weld in locations near chlorinated hydrocarbon
vapours coming from degreasing, cleaning or spraying
operations. The heat and rays of the arc can react with
solvent vapours to form phosgene, a highly toxic gas,
and other irritating products.
c.
Shielding gases used for arc welding can displace air
and cause injury or death. Always use enough
ventilation, especially in confined areas, to ensure
breathing air is safe.
d.
Read and understand the manufacturer’ s instructions
for this equipment and the consumables to be used,
including the material safety data sheet (MSDS) and
follow your employer’s safety practices.
e.
Also see Item 7b.
3.
a.
Use a shield with the proper filter and cover plates to
protect your eyes from sparks and the rays of the arc
when welding or observing open arc welding.
Headshield and filter lens should conform to AS
1674.2-1990 standards.
b.
Use suitable clothing made from durable flame
resistant material to protect your skin and that of your
helpers from the arc rays.
c.
Protect other nearby personnel with suitable non
flammable screening and/or warn them not to watch
the arc or expose themselves to the arc rays or to hot
spatter or metal.
4.
a.
Remove fire hazards from the welding area. If this is
not possible, cover them to prevent the welding sparks
from starting a fire. Remember that welding sparks
and hot materials from welding can easily go through
small cracks and openings to adjacent areas. Have a
fire extinguisher readily available.
b.
Where compressed gases are to be used at the job
site, special precautions should be used to prevent
hazardous situations. Refer to AS1674 Parts 1 & 2
“Safety in Welding and Allied Processes”, WTIA
Technical Note 7 “Health and Safety in Welding” and
the operating information for the equipment being
used.
c.
When not welding, make certain no part of the
electrode circuit is touching the work or ground.
Accidental contact can cause overheating and create
a fire hazard.
d.
Do not heat, cut or weld tanks, drums or containers
until the proper steps have been taken to insure that
such procedures will not cause flammable or toxic
vapours from substances inside. These can cause an
explosion even though the vessel has been “cleaned”.
For information purchase AS 1674-1990.
e.
Vent hollow castings or containers before heating,
cutting or welding. They may explode.
f.
Sparks and spatter are thrown from the welding arc.
Wear oil free protective garments such as leather
gloves, heavy shirt, cuffless trousers, high shoes and
a cap over your hair. Wear ear plugs when welding out
of position or in confined places. Always wear safety
glasses with side shields when in a welding area.
g.
Connect the work cable to the work as close to the
welding area as possible. Work cables connected to
the building framework or other locations away from
the welding area increase the possibility of the welding
current passing through lifting chains, crane cables or
other alternate circuits. This can create fire hazards or
overheat lifting chains or cables until they fail.
h.
Also see Item 7c.
ELECTRIC SHOCK can kill
FUMES AND GASES
can be dangerous
ARC RAYS can burn
WELDING SPARKS can
cause fire or explosion
Содержание IDEALARC R3R 500-I
Страница 21: ...IM 6000 Idealarc R3R 500 I 600 I Page 21 NOTES...
Страница 24: ...Page 24 Idealarc R3R 500 I 600 I IM 6000 NOTES...
Страница 42: ...Page 42 Idealarc R3R 500 I 600 I IM 6000 NOTES...
Страница 43: ...IM 6000 Idealarc R3R 500 I 600 I Page 43 NOTES...