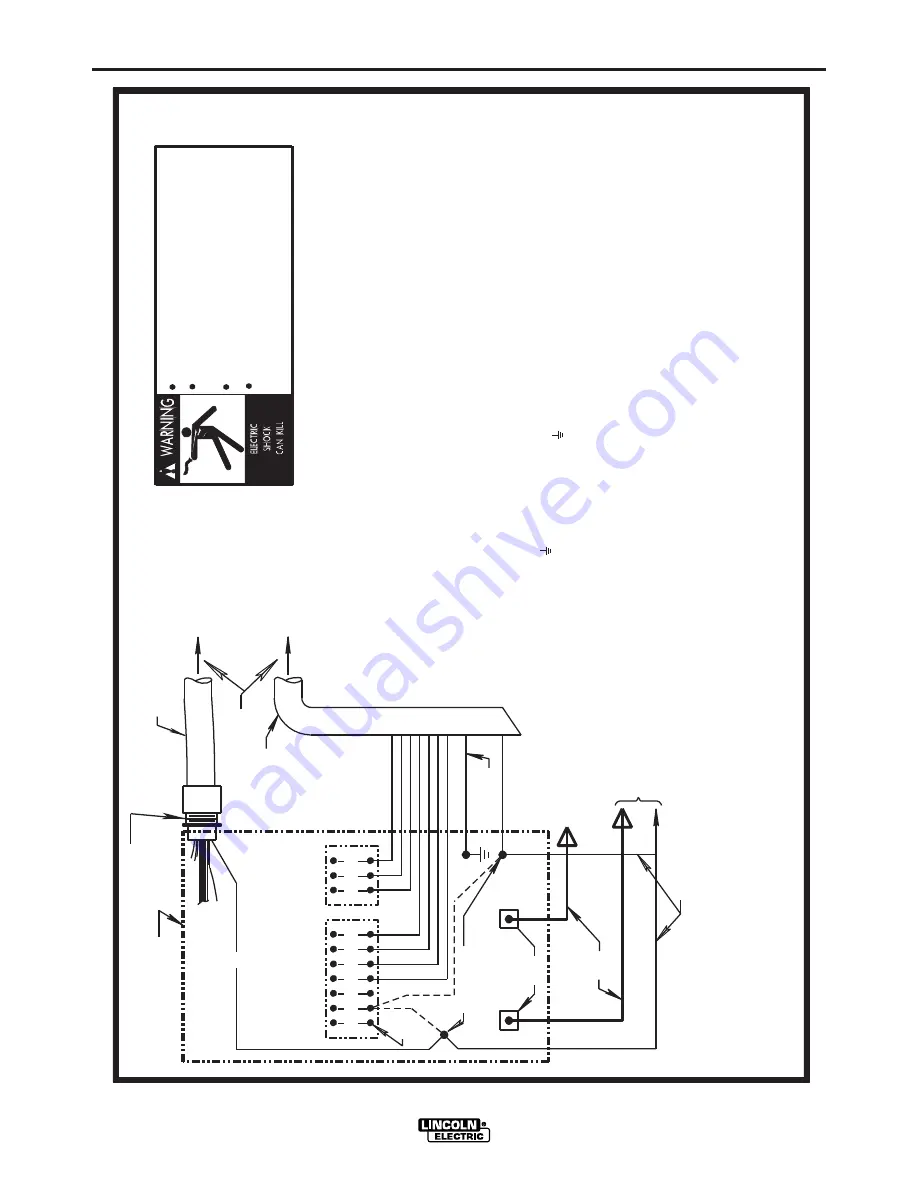
F-3
DIAGRAMS
F-3
DC-655
A
bove diagram shows electrode connected positive
.
T
o change polarity
,
turn power off
,
reverse the electrode and work leads at the power
NEGATIVE
POSITIVE
32 31 2 4
GND
21
N.A.
N.D.
ELECTRODE
CABLE
TO
WORK
POWER
SOURCE
O
nly qualified persons should install
,
use or
service this machine
.
D
o not operate with covers removed
.
D
isconnect power source before
servicing
.
D
o not touch electrically live parts
.
CONTROL
BOX
21
FOR
CONTROL
CABLE
WITH
14
PIN
MS-TYPE
PLUG
CONNECTOR
OR
FOR
CONTROL
CABLE
WITH
TERMINAL
STRIP
LEAD
CONNECTORS
CONTROL
CABLE
S22
97
8
N.B.
&
N.C.
14-PIN
RECEPTACLE
7
5
7
6
77
remote voltage sensing work lead may be ordered for this purpose
.
I
f lead #
21
is to be connected to
the terminal strip
,
connect to the #
21
terminal that matches
work polarity
.
T
his
connection must be changed whenever the
electrode polarity is
changed
.
N.A.
W
elding cables must be of proper capacity for the current and
duty cycle of immediate and future applications
.
C
onnect it directly to the work piece keeping it electrically
separate form the welding work lead circuit and connection
.
F
or
convenience
,
this extended #
21
lead should be taped to the
welding work lead
.
(
I
f the length of work lead circuit is
short
,
and connections can be expected to be reliable
,
then
control cable lead #
21
does not need to be extended and can be
directly connected to terminal #
21
on the terminal strip
.
N
ote
that this is not the preferred connection because it adds error
N.D.
C
onnect the control cable ground lead to the frame terminal
marked near the power source terminal strip
.
T
he power
source grounding terminal (marked and located near the power
source input power connections) must be properly connected to
electrical ground per the power source operating manual
.
to the wire feeder voltmeter reading
.
)
N.F.
source
.
R
everse the leads on the back of the ammeter and voltmeter
in the automatic control box
.A
lso refer to note
N.F.
TO
AUTOMATIC
E
Q
UIPMENT
TO
AUTOMATIC
CONTROL
CABLE
physically suitable for the installation
.
A
n
S16586-
[
LENGTH
]
41
423
1
32
7
5
7
6
77
N.F.
21
-
21
+
REMOTE
VOLTAGE
SENSING
LEAD
N.C.
T
ape up bolted connection if lead #
21
is extended
.
N.E.
I
f a variable voltage board is present in the automatic controls
,
the jumper lead on the
VV
board must be connected to pin "
L
" to
permit the inch down button to operate
.
T
his jumper
,
however
,
will disable the cold starting/autostop feature of the automatic
controls
,
permitting only hot starting techniques to be used
.
or from
14-
pin receptacle using #
14
AWG
or larger insulated wire
N.B.
E
xtend lead #
21
from control cable with terminal strip connectors
10-30-
9
8F
N.G.
I
llustration does not necessarily represent actual position of
manual for more information
.
N.G.
CONNECTION OF NA-3, LT-5 OR LT-7 TO THE CV-655, DC-655 OR DC-600 POWER SOURCE
appropriate output studs
.
R
efer to power source operating
F
or proper setting of switches on power source
,
see power source operating manual
.
Содержание DC-655 IM602-A
Страница 45: ...F 9 DIAGRAMS F 9 DC 655...
Страница 46: ...F 10 DIAGRAMS F 10 DC 655...