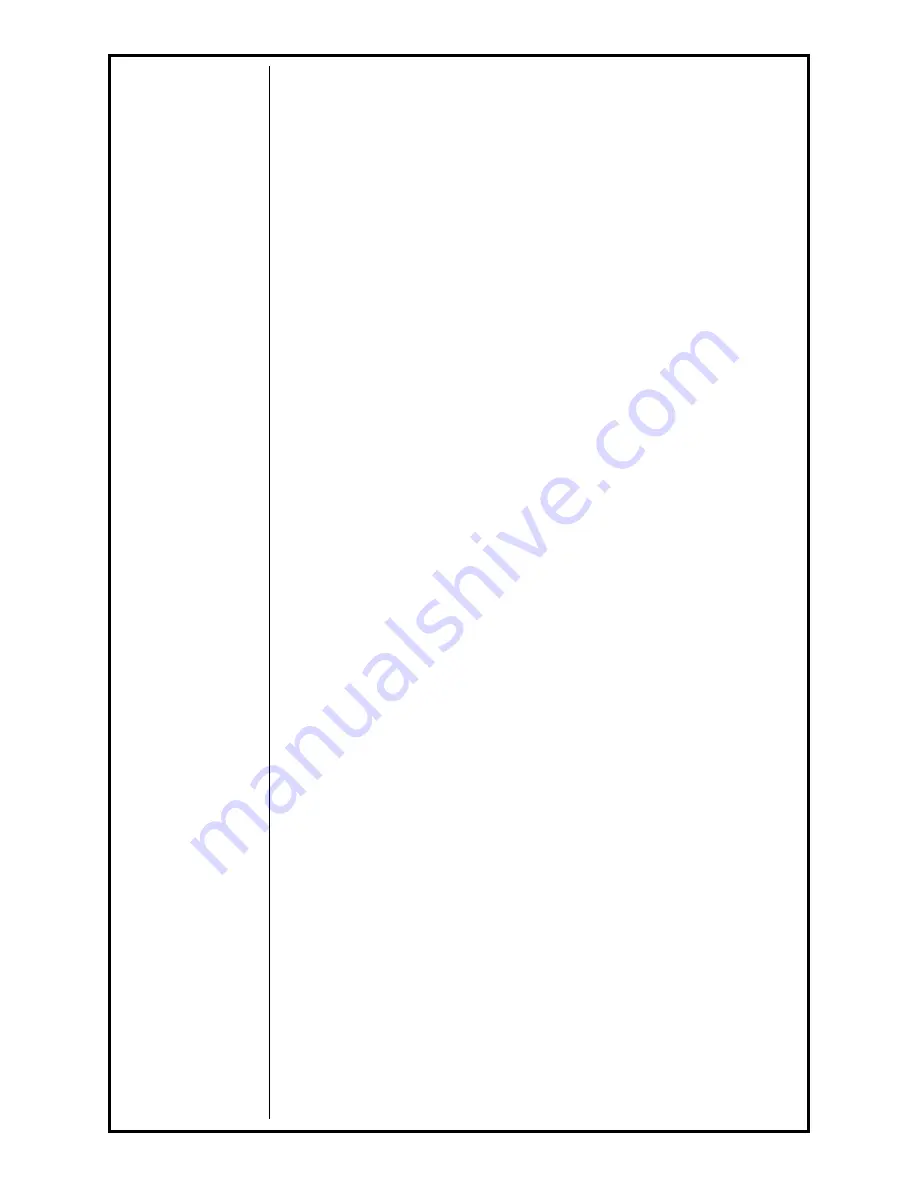
K1587-1 Cobramatic® Owner's Manual -
Page 14
7.3.3 CC POSA START OPERATION
Attach the Cobramatic® to a CC power source according to the installation
instructions.
Insure power supply high frequency switch is in the
“OFF”
position, and
power supply is set to DC reverse polarity.
The power supply contactor should be set to
“Remote”
or
“Tig”
and the
amperage control set to
“Panel”
or
“Standard”
depending on power supply.
Turn the Cobramatic® power switch to the
“ON”
position and the Posa Start
switch to the
“OFF”
position.
Adjust power source to desired amperage for your weld condition.
Press gun trigger and adjust wire feed speed at gun to match current setting.
If approximate wire feed speed is not known, it is better to start with excess
wire feed rather than too little, in order to prevent possible damage to the
contact tip.
Turn Posa Start switch to the
“ON”
position. Press torch trigger and, using
Run-in Speed Control, adjust wire feed speed to approximately 10% of
welding wire speed set at torch.
Strike an arc; if the wire stubs out, reduce wire feed rate at gun, or increase
amperage setting on power source.
NOTE: Because the Posa Start Run-in Speed always remains a percentage of the
actual welding wire feed rate, the Posa Start run-in speed will always slow down or
speed up proportional to any adjustment you now make at the gun. Therefore, if you
slow down the welding wire feed speed, you will have to increase the Run-in Speed
setting.
Section 8
MAINTENANCE
Maintenance of the torch will normally consist of a general cleaning of the
wire guide system, including tubes, drive rolls, and conduits at regular
intervals.
Remove spatter build-up from inside of nozzles with a hardwood stick.
The only parts on the Cobramatic system that are subject to normal wear are
the conduit, contact tips, gas cups, front body liners, wire guides, drive and
idler rolls. A supply of these parts should be maintained on hand.
If repairs do become necessary, any part can easily be replaced by a qualified
shop maintenance man.
Your Cobramatic® is designed to provide years of reliable service. Normal
wear and component failure may require occasional service.
The number of units in operation and the importance of minimal "down time"
will determine to what extent spare parts should be stocked on hand.
8.1 TESTING THE TORCH
8.1.1 MOTOR CHECK
Remove the amphenol connector from the cabinet.
Using the torch amphenol, check the resistance across pins
“A”
and
“B”
(motor leads). The resistance across the motor should be between
5-10
ohms.
If an open circuit or short exist, check the motor leads and motor
independently.
Содержание Cobramatic
Страница 2: ......
Страница 3: ......
Страница 4: ......
Страница 5: ......
Страница 6: ......
Страница 7: ...K1587 1 Cobramatic Owner s Manual Page 7 THIS PAGE INTENTIONALLY BLANK...
Страница 9: ...K1587 1 Cobramatic Owner s Manual Page 9 THIS PAGE INTENTIONALLY BLANK...
Страница 18: ...K1587 1 Cobramatic Owner s Manual Page 18 Exploded View K1587 1 Wire Feed Cabinet...
Страница 20: ...K1587 1 Cobramatic Owner s Manual Page 20 Exploded View MK P N 003 2016 Front Panel...
Страница 27: ...K1587 1 Cobramatic Owner s Manual Page 27 COBRAMATIC WIRING SCHEMATIC...
Страница 28: ...K1587 1 Cobramatic Owner s Manual Page 28 COBRAMATIC TORCH CONNECTIONS...
Страница 29: ...K1587 1 Cobramatic Owner s Manual Page 29 COBRAMATIC BLOCK DIAGRAM 071 0368...
Страница 34: ......
Страница 35: ......
Страница 36: ...K1587 1 Cobramatic Owner s Manual Page 36 THIS PAGE INTENTIONALLY BLANK...