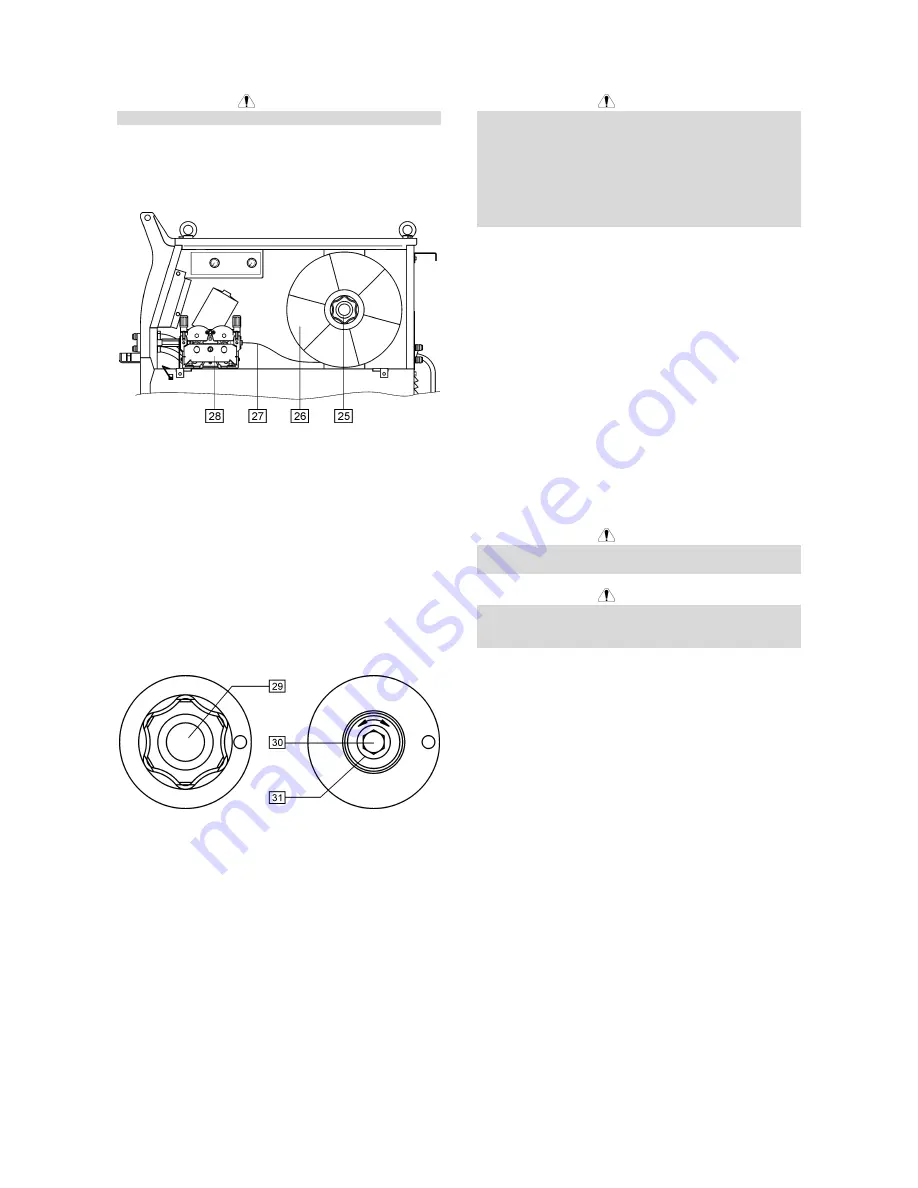
A-5
WARNING
Sharp end of the wire can hurt.
Rotate the wire spool clockwise and thread the end of
the wire into the wire feeder as far as the Euro socket.
Adjust force of pressure roll of the wire feeder properly.
25. Sleeve.
26. Wire spool.
27. Electrode wire.
28. Feeding unit.
The machine is designed for wire spools of 15kg
(300mm).
Adjustments of Brake Torque of Sleeve
To avoid spontaneous unrolling of the welding wire the
sleeve is fitted with a brake.
Adjustment is carried by rotation of its screw M10, which
is placed inside of the sleeve frame after unscrewing the
fastening cap of the sleeve.
29. Fastening cap.
30. Adjusting screw M10.
31. Pressing spring.
Turning the screw M10 clockwise increases the spring
tension and you can increase the brake torque.
Turning the screw M10 counterclockwise decreases the
spring tension and you can decrease the brake torque.
After finishing of adjustment, you should screw in the
fastening cap again.
Adjusting of Force of Pressure Roll
Force
Pressure force is adjusted by turning the adjustment nut
clockwise to increase force, counterclockwise to
decrease force.
WARNING
If the roll pressure is too low the roll will slide on the wire.
If the roll pressure is set too high the wire may be
deformed, which will cause feeding problems in the
welding gun. The pressure force should be set properly.
Decrease the pressure force slowly until the wire just
begins to slide on the drive roll and then increase the
force slightly by turning of the adjustment nut by one
turn.
Inserting Electrode Wire into Welding
Torch
Connect the proper welding torch to the Euro socket, the
rated parameters of the torch and of the welding source
shall match.
Switch on the power supply (the main switch [1] in “I”
position).
Remove the gas diffuser and contact tip from the
welding torch.
Set the wire feeding speed in the position of about
10m/min by the WFS knob [7].
Switch the Cold Inch / Gas Purge switch [5] in the
position “Cold Inch” and keep in this position until the
electrode wire leaves the contact tip of the welding torch.
WARNING
Take precaution to keep eyes and hands away from the
end of the torch while feeding wire.
WARNING
Once the wire has finished feeding through the welding
gun turn the machine “OFF“ before replacing to contact
tip and gas diffuser.
Gas Supplying
Connect the gas hose to the gas supplying socket [18]
located on the rear panel of the machine.
Put the gas cylinder on the machine shelf secure it with
the chain.
Take off the safety cap from the shielding gas cylinder
and install the flow regulator on it.
Connect the gas hose of the machine to the regulator
with the clamp band.
Welding with MIG / MAG method in
Manual mode
To begin welding process with MIG/MAG method in
manual mode you should:
•
Insert the plug of input supply cable into the main
socket.
•
Switch ON the machine with the “Power Switch” [1]
(it should light on).
•
Insert the electrode wire into the torch using ”Cold
Inch“ switch [5].
•
Check gas flow with ”Gas Purge” switch [5].
•
Set knob [17] in Manual position (verify that the
indicator [15] has lit the
Manual
mode).
•
According to selected welding mode and material
thickness set the proper welding voltage with
switches [3] and the wire feeding speed with WFS