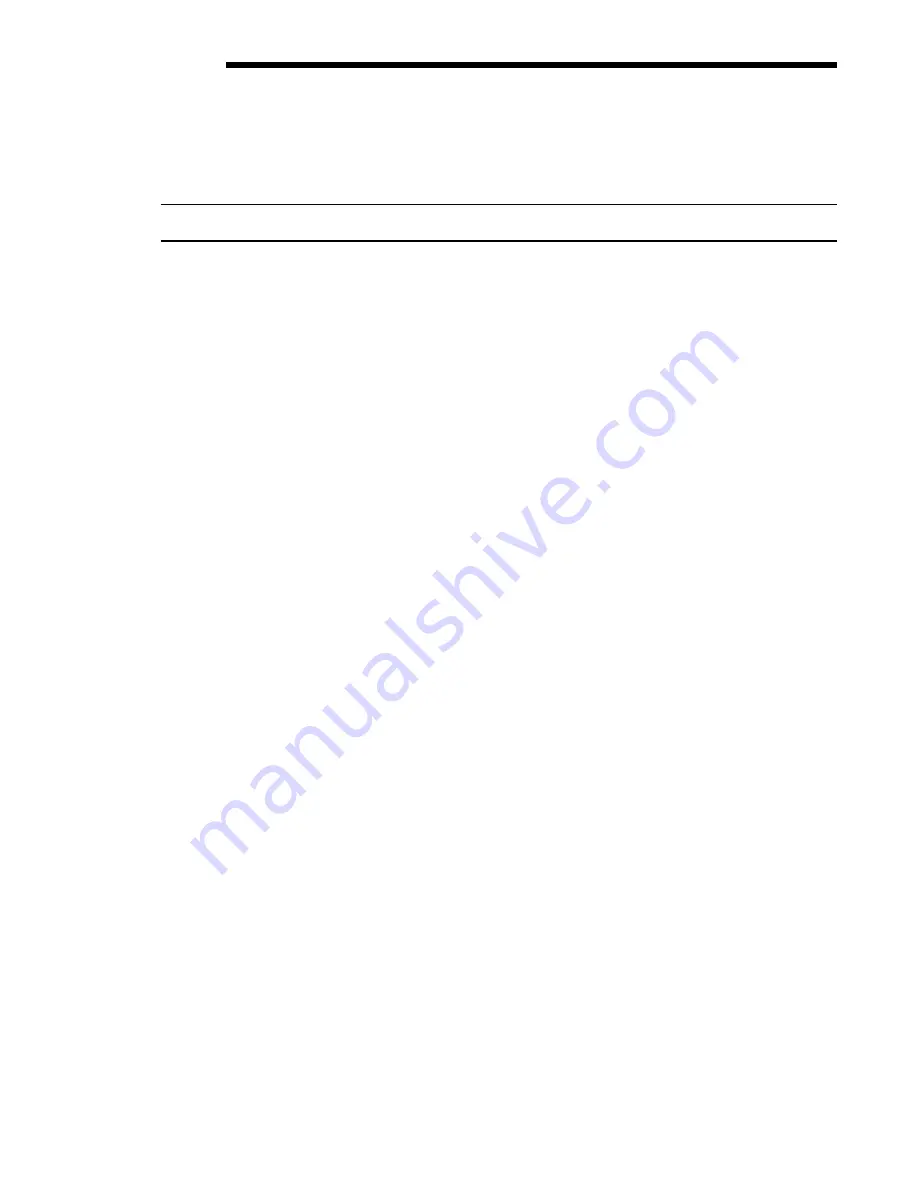
SMB/SB Installation and Maintenance Manual
140-11000 • July 2003
5-1
Flow Control Division
Limitorque Actuation Systems
5
Operation
a
WARNING: See Section 4.1 and 4.2 on Safety Precautions and Safety Practices prior to operation.
5.1 Motor Operation
Actuator motors are high-starting torque, totally enclosed motors. The motors are furnished in weatherproof, explosionproof, or
submersible enclosures. The motors are furnished with ball bearings and provided with grease seals. All three-phase AC motors are
squirrel-cage design and all DC motors are compound wound.
Piece numbers refer to Figure 7.12. However, this description is applicable to all models. The piece numbers will differ for each
model.
The electric motor has a Motor Pinion (piece #40) mounted on its shaft extension. This pinion drives the Worm Shaft Clutch Gear
(piece #41), which is engaged with the Worm Shaft Clutch (piece #50). The Worm Shaft Clutch is splined to the Worm Shaft (piece
#43). The Worm (piece #53) is splined to the Worm Shaft (piece #43), and when it is rotated, it turns the Worm Gear (piece #16).
The Worm Gear has two lugs cast onto the top portion that engage the two lugs on the Drive Sleeve (piece #11). These lugs are
spaced so that when the Worm Gear begins to turn during motor operation there is a certain amount of lost motion before the lugs
engage, causing the hammer blow effect within the actuator.
As soon as the Worm Gear Lugs engage, the Drive Sleeve, splined internally with the Stem Nut (piece #20), causes the stem nut to
rotate and open or close the valve. The Stem Nut is threaded to fit the thread of any rising stem valve. In the case of non-rising stem
valves, the electric actuator may be mounted in tandem with an additional gear drive, and the Stem Nut (piece #20) is bored and keyed
to fit the shaft.
The thrust developed by the actuator is absorbed by the heavy-duty Bearings (piece #75, 76, 77, 78) on the top and bottom of the
main Drive Sleeve. As the actuator develops greater torque, when seating the valve, the Worm (piece #53) slides axially along the
splines of the Worm Shaft (piece #43) and compresses the Belleville Springs (piece #56) in the torque spring pack.
The Belleville Springs are calibrated springs. For every increment of compression from a given size unit, a certain pre-determined
amount of torque is developed. The Worm mechanically actuates the Torque Switch. When the Worm moves back a preset distance
and develops the torque output required, the Torque Switch opens and a pair of electrical contacts that are wired into the motor
control circuit interrupt the circuit and stop the motor.
The Geared Limit Switch (piece #105) is directly geared to the Worm Shaft and is in step at all times with the movement of the
actuator. The switch cannot slip because no belts or other friction devices are used in its operation. Once the Geared Limit Switch
(piece #105) is set to trip at its proper position of valve travel, it will trip at the same point every time.
The Torque Switch (piece #104) is wired into the motor control circuit to stop the actuator in the full closed position for any rising
stem operation. The Geared Limit Switch (piece #105) is wired into the motor control circuit to stop the operator at the full open
position. For most 90˚ turn valves and sluice gates, the Geared Limit Switch is wired into the motor control circuit to stop the actuator
at both the full open and full close position of the valve or gate. The Torque Switch is wired in series with the Geared Limit Switch in
both directions so that in the event of a mechanical overload, the Torque Switch will open and cause the motor to stop.
Check the applicable wiring diagram to determine the correct wiring connections made for the torque switch and geared limit
switch.