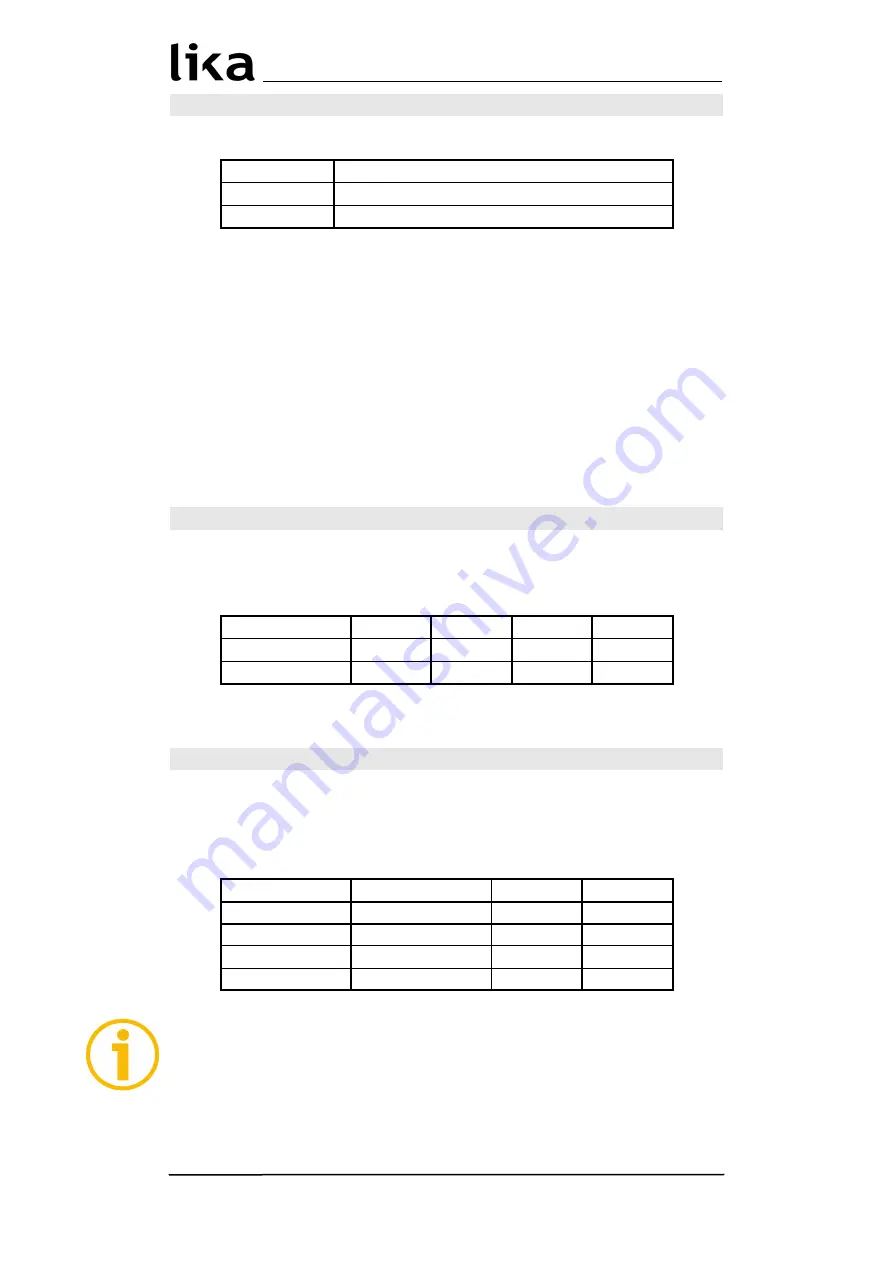
SMRA - SSI and BiSS
Command
[77, wo]
Value
Function
01
Save parameters
02
Save parameters and activate Preset
After having set a new value in any register use the
register to save the new value. Set “01” in the
register.
After having set a new value in any register use the
register to both save the new value
and activate the preset function at the same time. Set “02” in the
register.
After having sent the command the register is set back to "00" automatically.
Wait 30 ms at least (EPROM writing time) before activating a new function.
Device ID
[78 … 7B, ro]
These registers contain the Device ID. Identification name is expressed in
hexadecimal ASCII code.
Register
78
79
7A
7B
Hex
53
4D
52
41
ASCII
S
M
R
A
Time-out
[7C, rw]
It allows to set the minimum interval time between two transmission sequences.
After having set the desired time-out value, save data using the
register = “01”).
Time-out
Bit 7 ... bit 2
Bit 1
Bit 0
16 µs
0 … 0
0
0
8 µs
0 … 0
0
1
2 µs (default)
0 … 0
1
0
1 µs
0 … 0
1
1
NOTE
You can save the entered time-out value also by using the
register (
“02”). Please note that in this case you both save time-out data and activate the
preset function (see on page 27).
MAN SMRA SSI_BiSS E 1.2.odt
30
www.lika.it
www.lika.biz
Содержание MRA
Страница 1: ...User s guide SMRA MRA Bearingless absolute encoder Smart encoders actuators ...
Страница 32: ...SMRA SSI and BiSS 6 6 Recommended BiSS input circuit MAN SMRA SSI_BiSS E 1 2 odt 32 www lika it www lika biz ...
Страница 38: ...This page intentionally left blank ...
Страница 39: ...This page intentionally left blank ...