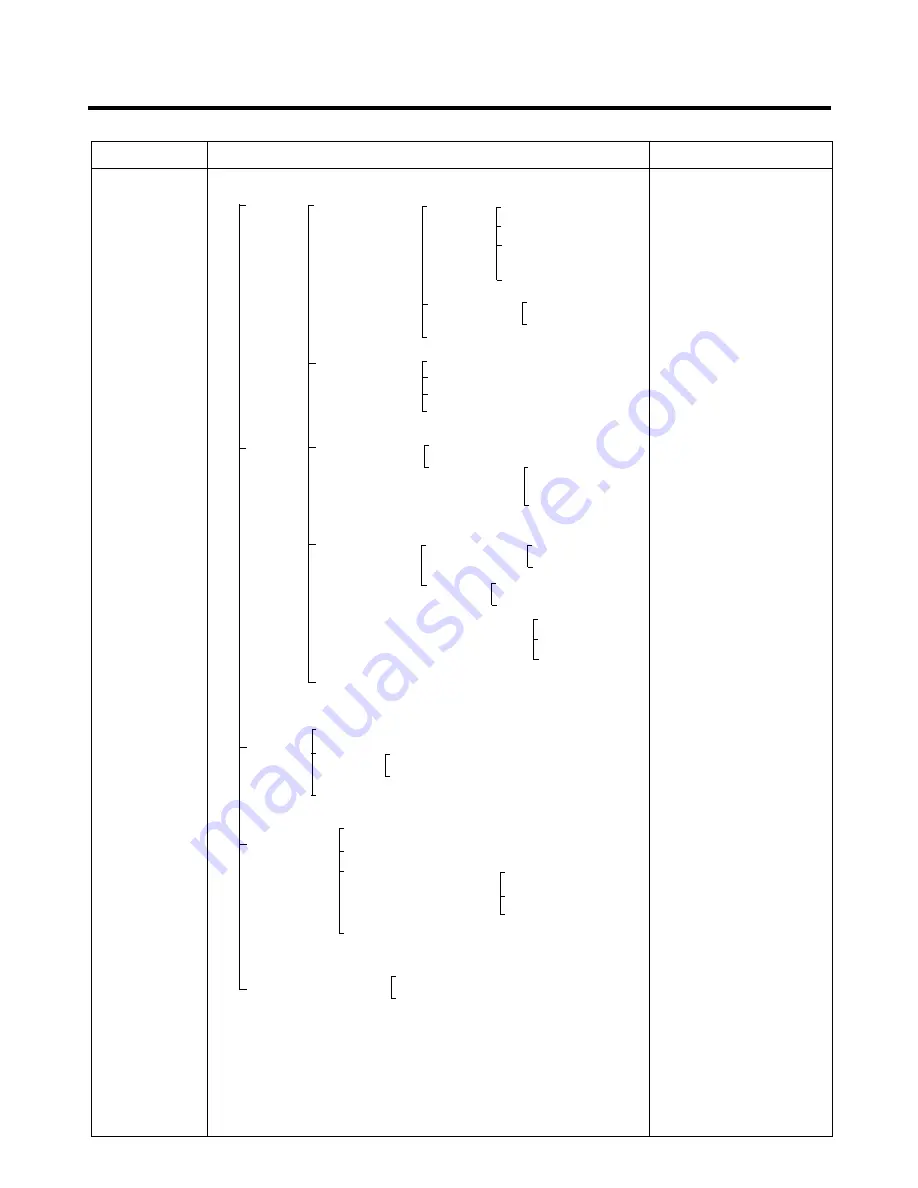
TROUBLE DIAGNOSIS
- 50 -
CLAIMS.
CAUSES AND CHECK POINTS.
HOW TO CHECK
2. No cooling.
2) Refrigeration system is clogged.
■
Check the clogged
evaporator by heating (as
soon as the cracking sound
begins, the evaporator start
freezing)
■
The evaporator does not cool
from the beginnig (no evidece
of misture attached).
The evaporator is the same
as before even heat is
applied.
Moisture
clogged.
No electric
power on
therm-
ostat.
Weld joint
clogged.
Drier cloggeing.
Foreign material clogging.
Residual moisture
in the evaporator.
Residual moisture.
Insufficient drier
capacity.
Residual moisture
in pipes.
Moisture penetration - Leave it in the air. - Moisture penetration.
into the refrigeration oil.
Caps are missed.
Air blowing.
During transportation.
During work.
Not performed.
Performed.
Too short time.
Low air pressure.
Less dry air.
Air Blowing.
Leave it in the air.
Caps are missed.
Short pipe insert.
Pipe gaps.
Too much solder.
Too large.
Damaged pipes.
Not dried in the compressor.
Elapsed more than 6 months after drying
Caps are missed.
No pressure when it is open.
During rest time.
After work.
Compressor cap is disconnected.
Foreign materials are in the pipe.
Not performed.
Too short.
Impossible moisture
confirmation.
Low air pressure.
Dry drier - Drier temperature.
Leave it in the air.
The capillary tube inserted depth. - Too much.
Capillary tube melts. - Over heat.
Clogged with foreign materials.
Reduced cross section by cutting. - Squeezed.
Desiccant powder.
Weld oxides.
Drier angle.
Check on package
condition.
Good storage after
finishing.