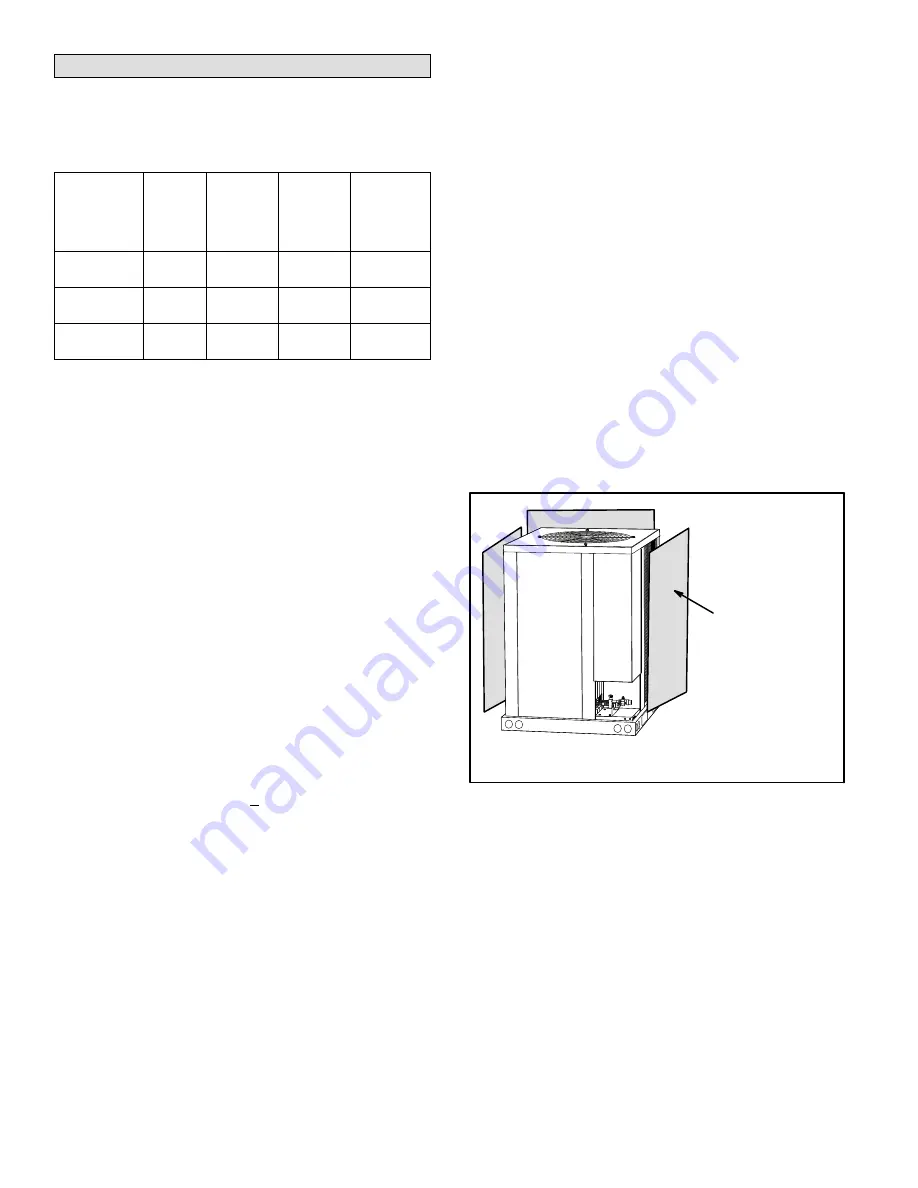
Page 8
Refrigerant Charge and Check
TPA units have a factory holding charge of 1 pound of
HFC-410A. Additional refrigerant will need to be added
during installation (table 2).
Table 2. Adding Refrigerant
Models
25 Feet
1
(pounds)
Liquid
Line
Diameter
(inches)
Vapor
Line
Diameter
(inches)
Adjustment
per foot of
Line
2
(Ounces)
TPA090 /
TAA090
17
5/8
1-3/8
1.8
TPA120 /
TAA120
23
5/8
1-3/8
1.8
(2) TPA090 /
TAA240
23
3
5/8
1-3/8
1.8
1
Total amount of charge necessary to accommodate 25
feet of line set.
2
If line set length is greater than 25 feet, add this amount to
each circuit. If line set is less than 25 feet, subtract this
amount from each circuit. Refer to Lennox Refrigerant
Piping Design and Fabrication Guidelines for more
information.
3
Charge amount per outdoor unit.
NOTE - Refrigerant line sets longer than
200 feet (60 meters)
are not recommended. For assistance contact Lennox
Application Department.
To charge the system, use either of the following
procedures:
CHARGE PROCEDURE — NORMAL OPERATING
PRESSURES
1. Connect a manifold gauge set to the service valves:
A
Low pressure gauge to vapor service port.
B
High pressure gauge to liquid valve service port
2. Operate system in cooling mode until pressures and
temperatures stabilize (5 minutes minimum).
3. Use a thermometer to measure the outdoor ambient
temperature. The outdoor temperature will determine
which charging procedure to use.
Outdoor Temp > 65ºF (18ºC)
1. Apply the outdoor ambient temperature to tables 4 or
5 to determine normal operating pressures. Compare
the normal operating pressures to the pressures
obtained from the connected gauges. If discharge
pressure is high, remove refrigerant from the system.
If discharge pressure is low, add refrigerant to the
system.
A
Add or remove charge in increments.
B
Allow the system to stabilize at least 5 minutes
each time refrigerant is added or removed
2. Minor variations in these pressures may be expected
due to differences in installations. Significant differences
could mean that the system is not properly charged or
that a problem exists with some component in the
system.
3. Switch to heating mode to confirm normal operating
pressures. Let the system stabilize at least 10 minutes
then compare the pressure obtained from the
connected gauges to the normal operating pressures
(heating mode) in table 5.
4. Verify the charge, as described in the approach
method section.
Outdoor Temp < 65ºF (18ºC)
1. When the outdoor ambient temperature is below 65F
(18C) it may be necessary to restrict the air flow
through the outdoor coil to achieve liquid pressures in
the 325-375 psig (2240-2585 kPa) range. These
higher pressures are necessary for checking the
charge. Block equal sections of the outdoor coil on all
coil sides until the liquid pressure is in the 325-375 psig
range (figure 4).
2. Charge the system as described in the approach
method section.
3. Switch to heating mode and let the system stabilize at
least 10 minutes. Then confirm that the pressures
obtained from the connected gauges match the
normal operating pressures (heating mode) in table 5
4. Minor variations in these pressures may be expected
due to differences in installations. Significant
differences could mean that the system is not properly
charged or that a problem exists with some
component in the system.
CARDBOARD OR
PLASTIC SHEET
OUTDOOR COIL SHOULD BE BLOCKED ONE SIDE AT A TIME
WITH CARDBOARD OR PLASTIC SHEET UNTIL PROPER
TESTING PRESSURES ARE REACHED.
Figure 4. Blocking Outdoor Coil
PROCEDURE — APPROACH METHOD
Use the following approach method along with the normal
operating pressures in cooling mode to confirm readings.
1. Using the same thermometer, compare liquid
temperature at service valve to outdoor ambient
temperature.
Approach Temperature = Liquid temperature
minus ambient temperature
2. Approach temperature should be as indicated in table
3 for each stage. An approach temperature greater
then this value indicates an undercharge. An approach
temperature less than this value indicates an
overcharge.
A
Add or remove charge in increments.
B
Allow the system to stabilize at least 5 minutes
each time refrigerant is added or removed