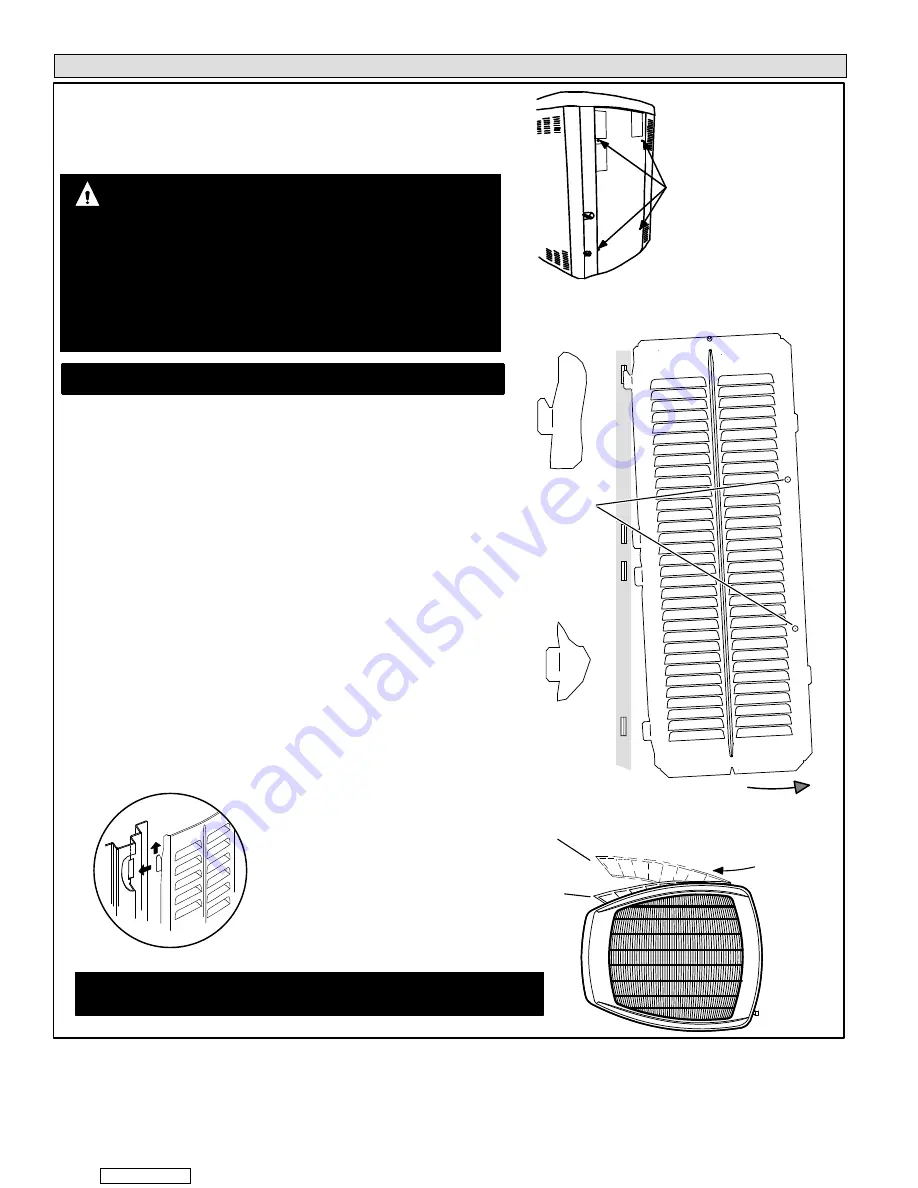
Page 10
506510−01
Removing and Installing Panels
REMOVE 4 SCREWS TO
REMOVE PANEL FOR
ACCESSING COMPRESSOR
AND CONTROLS.
POSITION PANEL WITH HOLES
ALIGNED; INSTALL SCREWS
AND TIGHTEN.
ACCESS PANEL REMOVAL
Removal and reinstallation of the access
panel is as illustrated.
Detail A
Detail C
Detail B
ROTATE IN THIS DIRECTION; THEN
DOWN TO REMOVE PANEL
SCREW
HOLES
LIP
PANEL SHOWN SLIGHTLY ROTATED TO ALLOW TOP TAB TO EXIT (OR ENTER) TOP SLOT
FOR REMOVING (OR INSTALLING) PANEL.
MAINTAIN MINIMUM PANEL ANGLE (AS CLOSE TO PARALLEL
WITH THE UNIT AS POSSIBLE) WHILE INSTALLING PANEL.
PREFERRED
ANGLE FOR
INSTALLATION
Detail D
ANGLE MAY BE
TOO EXTREME
HOLD DOOR FIRMLY ALONG THE
HINGED SIDE TO MAINTAIN
FULLY−ENGAGED TABS
LOUVERED PANEL REMOVAL
Remove the louvered panels as follows:
1.
Remove two screws, allowing the panel to swing open slightly.
2.
Hold the panel firmly throughout this procedure. Rotate bottom corner of panel
away from hinged corner post until lower three tabs clear the slots as illustrated in
Detail B.
3.
Move panel down until lip of upper tab clears the top slot in corner post as illustrated
in
Detail A
.
LOUVERED PANEL INSTALLATION
Position the panel almost parallel with the unit as illustrated in
Detail D
with the screw
side as close to the unit as possible. Then, in a continuous motion:
1. Slightly rotate and guide the lip of top tab inward as illustrated in
Detail A
and
C
;
then upward into the top slot of the hinge corner post.
2. Rotate panel to vertical to fully engage all tabs.
3. Holding the panel’s hinged side firmly in place, close the right−hand side of the pan-
el, aligning the screw holes.
4. When panel is correctly positioned and aligned, insert the screws and tighten
.
PANELS
ACCESS AND LOUVERED
IMPORTANT
Do not allow panels to hang on unit by top tab. Tab is for align-
ment and not designed to support weight of panel.
IMPORTANT
To help stabilize an outdoor unit, some installations may require
strapping the unit to the pad using brackets and anchors commonly available in the
marketplace.
To prevent personal injury, or damage to panels, unit or structure, be sure to observe
the following:
While installing or servicing this unit, carefully stow all removed panels out of the
way, so that the panels will not cause injury to personnel, nor cause damage to ob-
jects or structures nearby, nor will the panels be subjected to damage (e.g., being
bent or scratched).
While handling or stowing the panels, consider any weather conditions, especially
windy conditions, that may cause panels to be blown around and battered.
WARNING
Downloaded from
Содержание Signature XC17
Страница 21: ...Page 21 XC17 SERIES Figure 7 Typical XC17 Wiring Downloaded from ManualsNet com search engine...
Страница 39: ...Page 39 XC17 SERIES Figure 19 High Pressure Switch Operation Downloaded from ManualsNet com search engine...
Страница 40: ...Page 40 506510 01 Figure 20 Low Pressure Switch Operation Downloaded from ManualsNet com search engine...