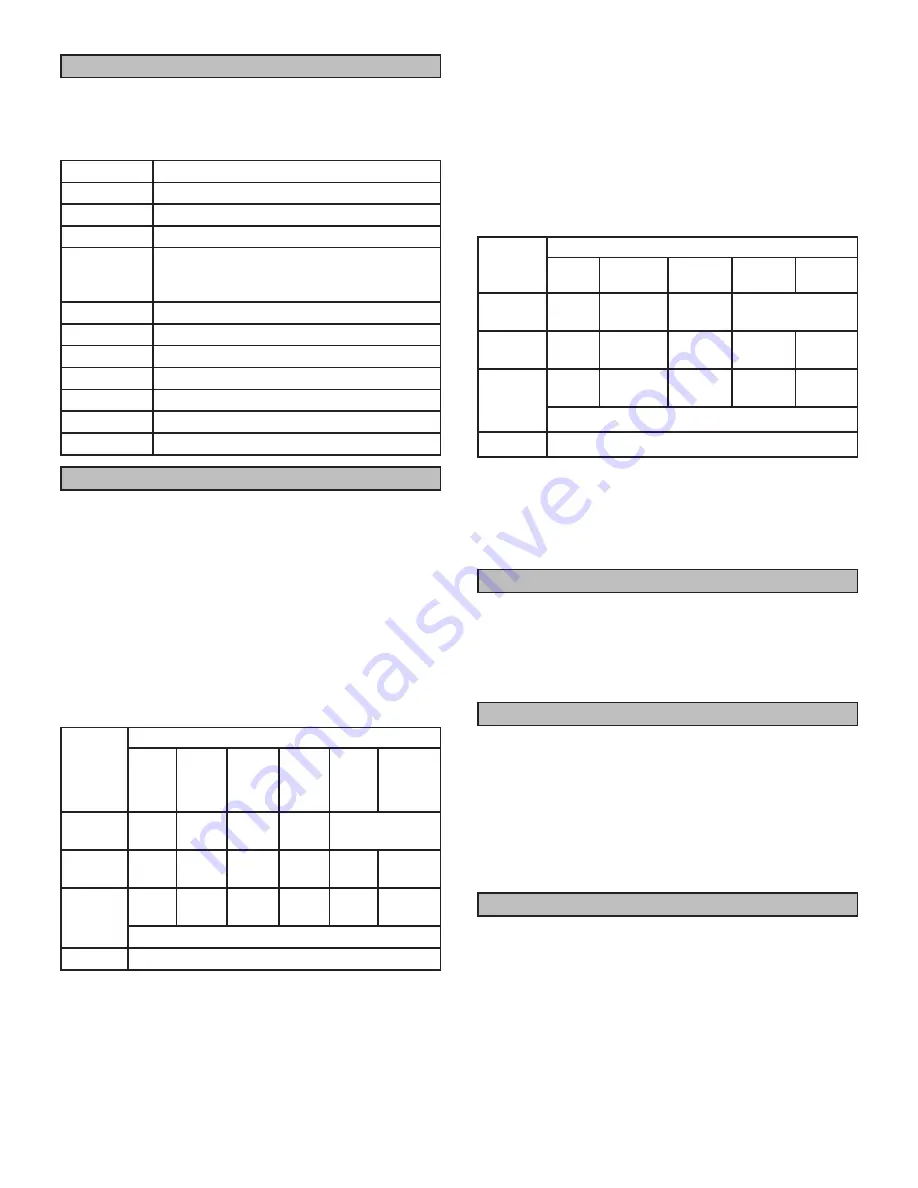
Page 22
Ignition Control LED
The ignition control contains a green LED which indicates
the following:
TABLE 6
IGNITION CONTROL LED
LED
UNIT OPERATION
Slow Flash*
Normal Operation - No call for heat
Fast F;lash
Normal Operation - Call for heat
2 Flashes
System lockout - failed to detect or sustain flame
3 Flashes
Pressure switch failed closed before CAI
is energized or failed open after CAI is
energized
4 Flashes
High limit (S10) switch open
5 Flashes
Flame sensed and gas valve (GV1) not energized
6 Flashes
On-board microprocessor fault.
7 Flashes
Pressure switch (S18) closed with inducer off.
8 Flashes
Rollout switch (S47/S195) open. Cycle-power to reset.
Steady On
Control board (A3) failure
Steady Off
Internal control board (A3) failure or not power.
High Altitude Adjustments
In Canada, certification for installation at altitudes over
4500 feet (1372m) above sea level is the jurisdiction of
local authorities. Lennox recommends derating 4%/1000
feet above 4,500 feet. Refer to table 7 for natural gas
manifold pressures and the Engineering Handbook for
high altitude kit part numbers.
Units may be fired at full input up to 2000 feet. (610m)
above sea level. Above 2000 feet (610m), manifold pres-
sure must be adjusted. Adjust pressure regulator to pres-
sure shown in table 7.
TABLE 7
CANADA - NATURAL GAS MANIFOLD PRESSURES
[inch w.g. (kPa)]
Unit
Altitude in Feet (Meters)
0-2000
(0- 610)
2001-
4500
(610-
1372)
4501-
5500
(1372-
1676)
5501-
6500
(1677-
2012)
6501-
7500
(2012-
2286)
7501-
9500
(2286-
2896)
125, 150,
175, 200
3.5
(0.87)
3.1
(0.77)
2.8
(0.70)
2.6
(0.65)
See Kit Instruction
250, 300,
350, 400
3.7
(0.92)
3.2
(0.80)
2.9
(0.72)
2.8
(0.70)
2.6
(0.65)
See Kit
Instruction
250, 300,
350
3.7*
(0.92)
3.3*
(0.82)
2.9*
(0.72)
2.8*
(0.70)
2.6*
(0.65)
See Kit
Instruction
1.6** (0.40)
400
1.7**(0.42)
* High Fire **Low Fire
NOTE -
A natural to LP/propane gas changeover kit is
required to convert the unit in the field. Refer to the in
-
stallation instructions supplied with the changeover kit for
conversion procedure.
In the US, units may be fired at full input up to 2000 feet
(610m) above sea level. Above 2000 feet (610m), unit
must be de-rated by four percent per 1000 feet for in-
stallation above 2000 feet. The de-rate may be accom-
plished by adjusting the manifold pressure. Refer to table
8 for natural gas manifold pressures and the Engineering
Handbook for high altitude kit part numbers.
TABLE 8
US - NATURAL GAS MANIFOLD PRESSURES
[inch w.g. (kPa)]
Unit
Altitude in Feet (Meters)
0-2000
(0- 610)
2001-3000
(610- 914)
3001-4000
(915- 1219
4001-5000
(1220-1524)
5001-10000
(1524-3048)
125, 150,
175, 200
3.5
(0.87)
2.9
(0.72)
2.7
(0.67)
See Kit Instruction
250, 300,
350, 400
3.7
(0.92)
3.1
(0.77)
2.8
(0.70)
2.6
(0.65)
See Kit
Instruction
250, 300,
350
3.7*
(0.92)
3.1*
(0.77)
2.8*
(0.70)
2.6*
(0.65)
See Kit
Instruction
1.6** (0.40)
400
1.7** (0.42)
* High Fire **Low Fire
In some cases, it is necessary to change the pressure
switch to ensure proper operation at higher altitudes. See
EHB for high altitude pressure switch kits.
The combustion air inducer proving switch is factory set.
No adjustment is necessary.
Gas Flow
To check for proper gas flow to the combustion chamber,
determine the Btu input from the appliance rating plate. Di-
vide this input rating by the Btu per cubic feet of available
gas. Result is the required number of cubic feet per hour.
Determine the flow of gas through the gas meter for two
minutes and multiply by 30 to get the hourly flow of gas.
Supply Gas Pressure Adjustment
Supply pressure should be checked with unit firing at max
-
imum rate. For Natural Gas, supply pressure should be
maintained in accordance with the specified minimum and
maximum supply pressures on the unit rating plate.
A natural gas to LP/propane gas changeover kit is re-
quired to convert the unit in the field. Refer to installation
instructions provided with changeover kit for conversion
procedure along with propane minimum and maximum
supply pressures.
Supply Pressure Measurement
1 -
Shut off the manual main supply valve (field
furnished) when installing or removing the measuring
device (Steps 2 and 6).
2 – Connect the measuring device based upon type of
gas valve.
For White Rodgers 36G valve (Figure 13), an inlet post lo-
cated on the gas valve provides access to the supply pres-
sure. Open the inlet port by backing out the 3/32” hex screw
one turn. Connect a piece of tubing over the inlet post and
route to a measuring device to measure supply pressure.
Содержание LS25 Series
Страница 5: ...Page 5 ...