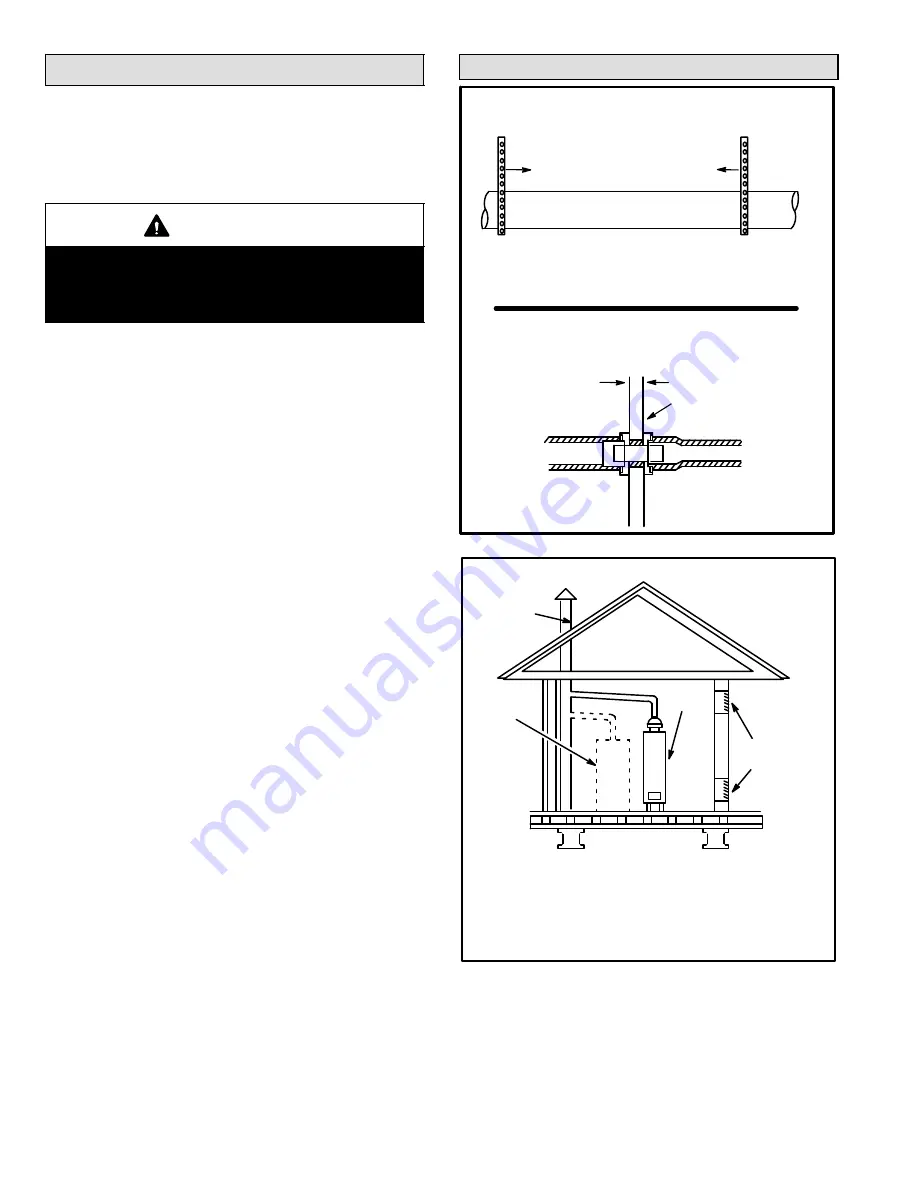
Page 20
Joint Cementing Procedure
All cementing of joints should be done according to the
specifications outlined in ASTM D 2855.
NOTE
− A sheet metal screw may be used to secure
the intake pipe to the connector, if desired. Use a drill
or self tapping screw to make a pilot hole.
DANGER
DANGER OF EXPLOSION!
Fumes from PVC glue may ignite during system
check. Allow fumes to dissipate for at least 5 minutes
before placing unit into operation.
1 − Measure and cut vent pipe to desired length.
2 − Debur and chamfer end of pipe, removing any ridges
or rough edges. If end is not chamfered, edge of pipe
may remove cement from fitting socket and result in a
leaking joint.
NOTE −
Check the inside of vent pipe thoroughly for
any obstruction that may alter furnace operation.
3 − Clean and dry surfaces to be joined.
4 − Test fit joint and mark depth of fitting on outside of pipe.
5 − Uniformly apply a liberal coat of PVC primer for PVC or
use a clean dry cloth for ABS to clean inside socket
surface of fitting and male end of pipe to depth of fitting
socket.
6 − Promptly apply solvent cement to end of pipe and in-
side socket surface of fitting. Cement should be ap-
plied lightly but uniformly to inside of socket. Take
care to keep excess cement out of socket. Apply sec-
ond coat to end of pipe.
NOTE
− Time is critical at this stage. Do not allow prim-
er to dry before applying cement.
7 − Immediately after applying last coat of cement to pipe,
and while both inside socket surface and end of pipe
are wet with cement, forcefully insert end of pipe into
socket until it bottoms out. Turn PVC pipe 1/4 turn dur-
ing assembly (but not after pipe is fully inserted) to dis-
tribute cement evenly. DO NOT turn ABS or cellular
core pipe.
NOTE
− Assembly should be completed within 20 sec-
onds after last application of cement. Hammer blows
should not be used when inserting pipe.
8 − After assembly, wipe excess cement from pipe at end
of fitting socket. A properly made joint will show a
bead around its entire perimeter. Any gaps may indi-
cate an improper assembly due to insufficient sol-
vent.
9 − Handle joints carefully until completely set.
Venting Practices
FIGURE 17
* See table 7 for allowable pipe.
Piping Suspension Guidelines
NOTE
− Isolate piping at the point where it exits the outside wall or
roof in order to prevent transmission of vibration to the structure.
SCHEDULE 40
PVC − 5’
all other pipe* − 3’
Wall
inside
outside
24" maximum
3/4" minimum
Wall Thickness Guidelines
CHIMNEY
OR GAS
VENT
(Check sizing
for water
heater only)
FURNACE
(Replaced
by EL193)
WATER
HEATER
OPENINGS
(To Adjacent
Room)
If an EL195DF furnace replaces a furnace which was com-
monly vented with another gas appliance, the size of the ex-
isting vent pipe for that gas appliance must be checked.
Without the heat of the original furnace flue products, the
existing vent pipe is probably oversized for the single water
heater or other appliance. The vent should be checked for
proper draw with the remaining appliance.
FIGURE 18
REPLACING FURNACE THAT
WAS PART OF A COMMON
VENT SYSTEM
2. In areas where piping penetrates joists or interior
walls, hole must be large enough to allow clearance on
all sides of pipe through center of hole using a hanger.