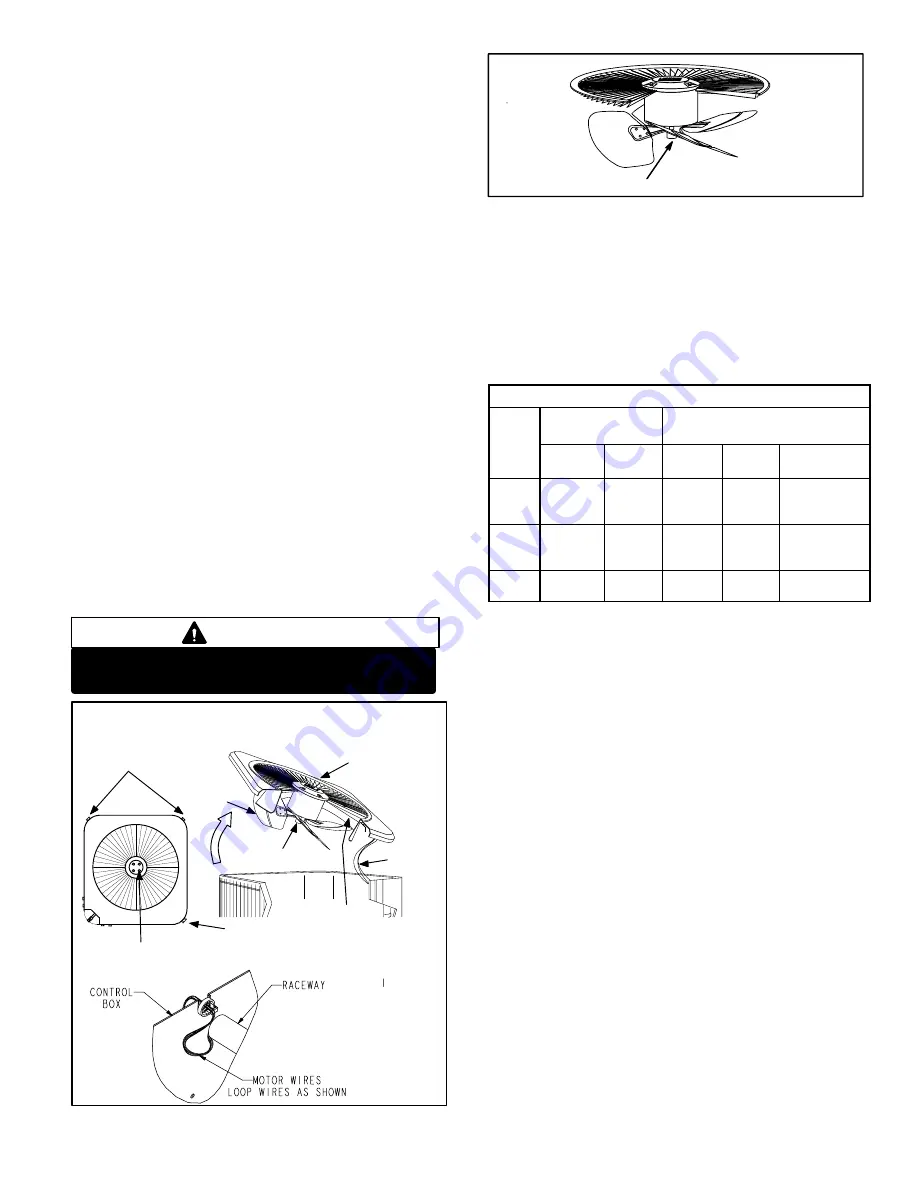
Page 5
Due to its efficiency, the scroll compressor is capable of draw-
ing a much deeper vacuum than reciprocating compres-
sors. Deep vacuum operation can cause internal fusite
arcing resulting in damaged internal parts and will result
in compressor failure. Never use a scroll compressor for
evacuating or to pump system into a vacuum. This type
of damage can be detected and will result in denial of
warranty claims.
The scroll compressor is quieter than a reciprocating com-
pressor, however, the two compressors have much different
sound characteristics. The sounds made by a scroll compres-
sor do not affect system reliability, performance, or indicate
damage.
See compressor nameplate or ELECTRICAL DATA for
compressor specifications.
C − Condenser Fan Motor
All units use single−phase PSC fan motors which require a run
capacitor. In all units, the condenser fan is controlled by
the compressor contactor.
ELECTRICAL DATA tables in this manual show specifi-
cations for condenser fans used in 13ACDs.
Access to the condenser fan motor on all units is gained
by removing the seven screws securing the fan assem-
bly. See figure 6. The condenser fan motor is removed
from the fan guard by removing the four nuts found on the
top panel. Drip loops should be used in wiring when ser-
vicing motor. See figure 7 if condenser fan motor re-
placement is necessary.
Make sure all power is disconnected before
beginning electrical service procedures.
DANGER
FAN
CONDENSER FAN MOTOR
AND COMPRESSOR ACCESS
Remove (7) screws
REMOVE (7) SCREWS
SECURING FAN GUARD.
REMOVE FAN GUARD/FAN
ASSEMBLY.
MOTOR
FAN GUARD
WIRING
FIGURE 6
RACEWAY
Remove (4) nuts
ALIGN FAN HUB FLUSH WITH END OF SHAFT
FIGURE 7
II − REFRIGERANT SYSTEM
A − Plumbing
Field refrigerant piping consists of liquid and suction lines
from the condensing unit (sweat connections) to the indoor
evaporator coil (flare or sweat connections). Use Lennox
L15 (sweat) series line sets as shown in table 1.
TABLE 1
Refrigerant Line Sets
Model
Valve Field Size
Connections
Recommended Line Set
Model
Liquid
Line
Vapor
Line
Liquid
Line
Vapor
Line
L15
Line Sets
−018
−024
−030
3/8 in.
(10 mm)
3/4 in.
(19 mm)
3/8 in
(10 mm)
3/4 in.
(19 mm)
L15−41
15 ft. − 50 ft.
(4.6 m − 15 m)
−036
−042
−048
3/8 in.
(10 mm)
7/8 in
(22 mm)
3/8 in.
(10 mm)
7/8in
(22 mm)
L15−65
15 ft. − 50 ft.
(4.6 m − 15 m)
−060
3/8 in.
(10 mm)
1−1/8 in.
(29 mm)
3/8 in.
(10 mm)
1−1/8 in.
(29 mm)
Field
Fabricated
NOTE − Units are designed for line sets of up to fifty feet (15
m). For applications longer than fifty feet, consult the Len-
nox Refrigerant Piping Guide (Corp. 9351−L9)
.
Select line
set diameters from table 1 to ensure that oil returns to the
compressor.
B − Service Valves
The liquid line and vapor line service valves (figures 9 and
8) and gauge ports are used for leak testing, evacuating,
charging and checking charge. See table 2 for torque re-
quirements.
Each valve is equipped with a service port which has a fac-
tory−installed Schrader valve. A service port cap protects
the Schrader valve from contamination and serves as the
primary leak seal.