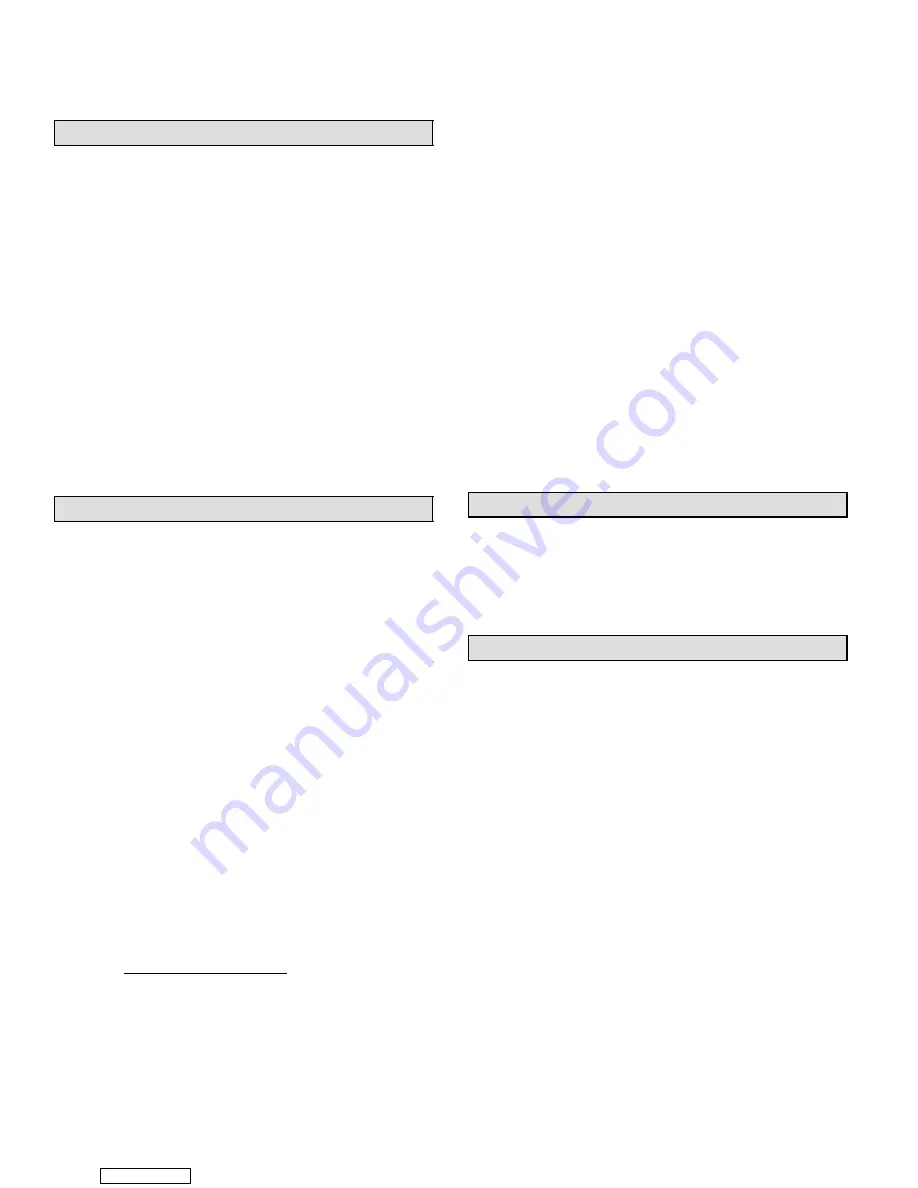
Page 14
4 − Adjust temperature rise to the range specified on the
rating plate.
Burner Adjustments
To check or change burners or orifices,
CLOSE MAIN
MANUAL SHUTOFF VALVE AND SHUT OFF ALL
POWER TO THE UNIT.
1 − Open the union fitting in the gas supply line just up
stream of the unit gas valve and downstream from the
manual shutoff valve.
2 − Remove Burner Access Panel.
3 − Remove the four (4) screws, two (2) on the side and
two (2) on bottom that mount the burner rack assembly
to the burner plate.
4 − Disconnect wiring to the gas valve and the elec
trode/flame sensor. Remove burner rack assembly
from the unit by pulling back. Burners are now ac
cessible to service.
5 − Reverse the above procedure to replace the assem
bly. Make sure that burners are level and centered into
each burner’s corresponding heat exchanger tube.
Manifold Gas Pressure Adjustment
For Natural Gas Applications
The minimum permissible gas supply pressure is 5.0
inches W.C. for purpose of input adjustment.
Gas input must never exceed the input capacity shown on
the rating plate. The furnace is equipped for rated inputs
with manifold pressures as follows:
Natural Gas 3.5 inches W.C.
The manifold pressure can be measured by removing the
pipe plug in the downstream side of the gas valve and
connecting water manometer or gauge.
In no case should the final manifold pressure vary more
than 0.3 inch W.C. from the above specified pressures.
See figures 11 and 12. To adjust the regulator, turn the
adjusting screw on the regulator, turn the adjusting screw
on the regulator clockwise to increase pressure and input;
counterclockwise to decrease pressure and input.
Check the furnace rate by observing gas meter, making
sure all other gas appliances are turned off. The test hand
on the meter should be timed for at least one revolution.
Note the number of seconds for one revolution.
BTU/HR =
Cubic Feet Per Revolution
X 3600 X Heating Value
INPUT
No. Seconds Per Revolution
The heating value of your gas can be obtained from your
local utility.
Example: By actual measurement, it takes 38 seconds for
the hand on the 1−cubic foot dial to make a revolution with a
100,000 Btuh furnace running. The result is 99,750 Btuh,
which is close to the 100,000 Btuh rating of the furnace.
For LPG / Propane Gas Applications
L.P.G./Propane units require a regulator, and a regulator on
the L.P.G./Propane tank is also required.
The minimum permissible gas supply pressure is 11 inches
W.C. for purpose of input adjustment.
If at any time ignition is slow and burner does not seem to
be operating correctly, check manifold pressure. It should
be 10.0 inches to 10.5 inches W.C. PRESSURE FOR
LPG/PROPANE.
Furnace is designed to obtain rated input at 10.0 inches
W.C. To check this pressure:
1 − Turn off gas valve.
2 − Remove plug on valve marked OUTLET PRES
SURE"
3 − Install water manometer.
Turn gas valve ON. If manifold pressure must be adjusted,
remove cap from pressure regulator and turn adjustment
screws clockwise to increase pressure, counterclockwise
to reduce pressure. After checking pressure, turn gas off,
remove manometer fitting and replace pipe plug and
regulator cap. Put furnace in operation and leak check plug
for leaks using soapy solution.
High Altitude Information
Ratings shown on the rating plate for elevations up to 4,500
feet. For elevations above 4,500 feet, ratings should be
reduced at a rate of four (4) percent for each 1,000 feet
above sea level. See National Fuel Gas Code Z223.1
(latest edition) or the requirements of the
CAN/CGA−B149.1 or B149.2 Installation Code.
Unit Controls
Limit Control
This control is located inside the heating compartment and
is designed to open at abnormally high air temperatures. It
resets automatically. The limit switch operates when a high
temperature condition, caused by inadequate blower
supply airflow, occurs, thus shutting down the
blower/ignition control and closing the main gas valve. The
circulating air blower will continue to operate.
Pressure Switch
If the draft motor should fail, the pressure switch prevents the
blower/ignition control and gas valve from being energized.
Spark Electrode and Flame Sensor Rod
The spark electrode and flame sensor rod are part of the
burner assembly. The burner position of the spark
electrode varies by model. The flame sensor rod is always
adjacent to the spark electrode. If the blower/ignition
control does not receive a signal from the flame sensor
indicating that the burners have established flame, the
main gas valve will close after the 10 second ignition trial
period built into the ignition control.
Rollout Switch
The switch is located above the main burners which in the
event of a sustained main burner rollout shuts off the
Downloaded from