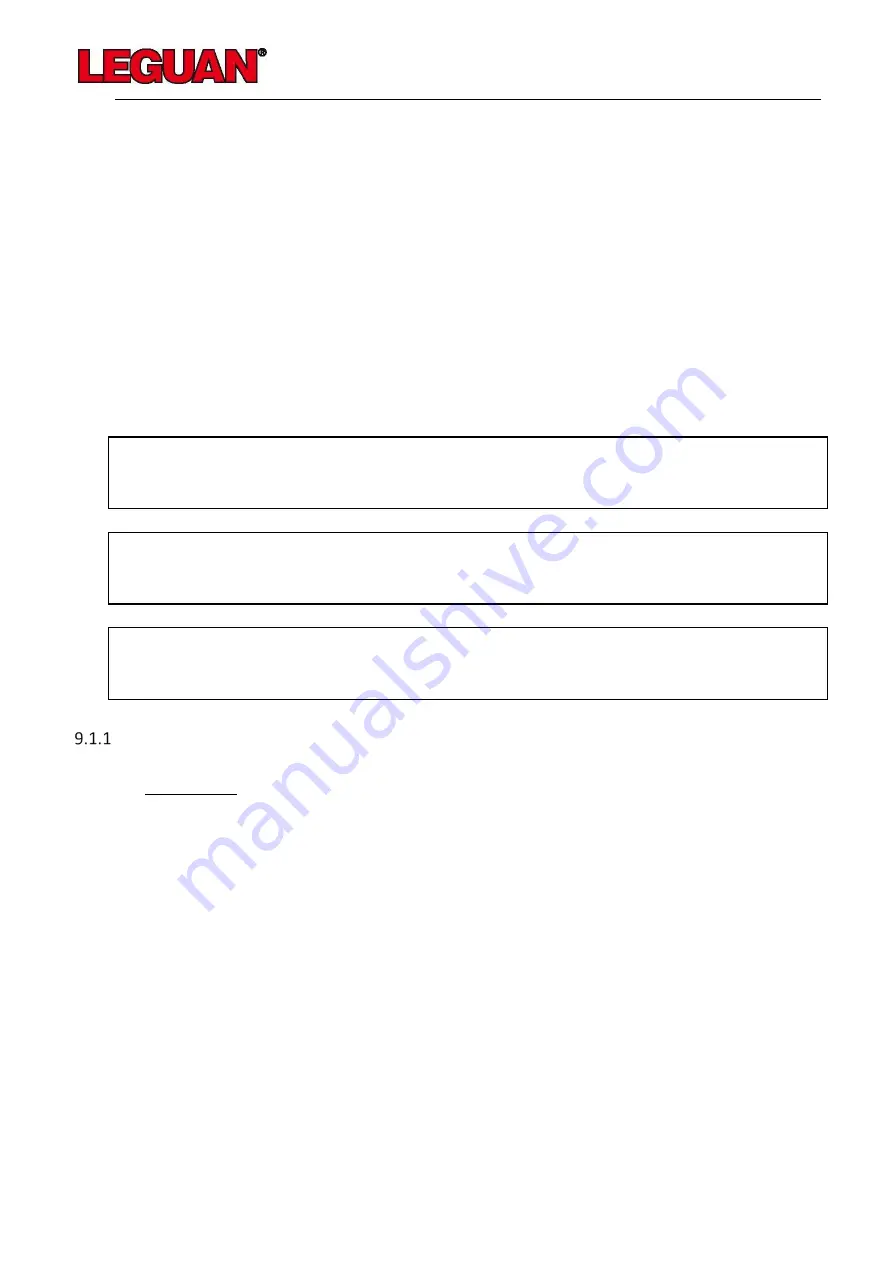
39
Recommended oil:
FUCHS HYDRAULIC OIL 131 HP
Hydraulic system oil volume:
Oil tank 25 l, complete system 55 l
Engine oil:
See engine manufacturer’s manual
Grease:
Lithium NLGI 2 grease (not MoS2),
Slewing ring grease:
grease containing EP (extreme pressure)
component (e.g. Mobil Mobilith SHC 220)
Pressure settings of hydraulic system:
main pressure 206 bar
slewing pressure 120 bar
drive motor brake pressure 25 bar
Tyre pressure:
3 bar
Backlash of the wear pads on the telescopic boom must be checked every year and the wear
pads must be replaced every 5 years.
The pulley chains and/or cables of the telescope booms, their pulley
wheels and fasteners must be replaced during the access platform’s 10-
year service.
The abovementioned service intervals are recommendations. If the
operating conditions are challenging and/or the machine is in heavy duty
use, the service and change intervals must be shortened.
Tightening torque of the M16 fastening bolts of the slewing ring is 210 Nm
– torque must be checked once a year and bolts must be changed every 10
years. If a bolt has loosened, it must be replaced with a new bolt.
Crawler track and 4WD wheel nuts
For 4WD chassis machines the tightening torque for the wheel nuts is as follows:
-
First tighten the nuts to 150 Nm ± 25Nm
-
Then retighten the nuts to
200 Nm ± 25Nm
-
We recommend inspecting the tightness of the nuts once a week
It is important to check the tightening of nuts on the track wheels 2 days after commissioning
the access platform. When driving with a new machine, the parts in the track system adapt to
each other and “find their place”. Because of this, the nuts may loosen during operation. Loose
nuts can cause serious damage to the crawler track chassis. Tighten the track sprocket nuts:
-
First tighten the nuts to 200 ± 25 Nm diagonally opposite.
-
Then retighten the nuts to
250 ± 25 Nm
diagonally opposite.
-
We recommend inspecting the tightness of the nuts once a week
Содержание 135 NEO
Страница 1: ...Operator and Service manual Version 7 2020 July 2020 ...
Страница 9: ...9 Main dimensions Figure 2 135 NEO Main dimensions side Figure 3 135 NEO main dimensions rear ...
Страница 10: ...10 Reach diagram and support dimensions Figure 4 Reach diagram Figure 5 Support dimensions ...
Страница 59: ...59 Figure 37 Load control of the platform Figure 38 Boom position monitoring ...
Страница 60: ...60 Figure 39 Platform levelling monitoring Figure 40 Outrigger monitoring ...
Страница 61: ...61 Figure 41 Transport position monitoring Figure 42 Prevention of drive function ...
Страница 62: ...62 Figure 43 Selection of the platform control position Figure 44 Selection of the lower control position ...
Страница 63: ...63 Figure 45 Selection of the remote control position Figure 46 Platform emergency stop button override ...
Страница 64: ...64 Figure 47 Platform load monitoring override Figure 48 Override of Safety Functions ...