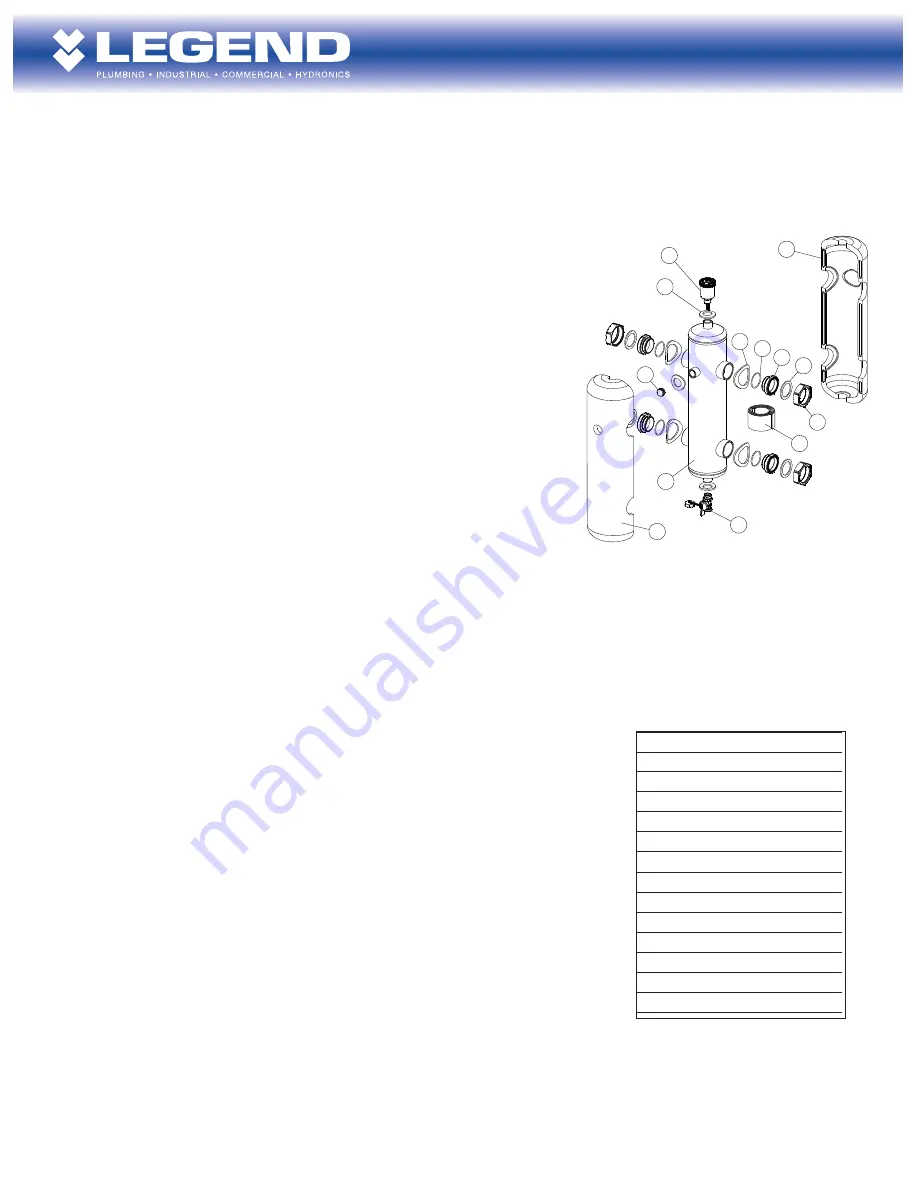
www.legendhydronics.com
1-866-752-2055
300 N. Opdyke Rd.
Auburn Hills, MI 48326
www.legendhydronics.com
866-752-2055
HS-808
HYDRAULIC SEPARATOR
Installation Guide
Installation / Assembly-continued
8. The Air Vent
(2)
should always be installed onto the 1/4” x 1/2” Service Check Adapter (included
with the Automatic Air Vent). Thread the male end of the Service Check Adapter into the top 1/2”
port on the HS-808. Thread the 1/4” male threads of the Air Vent into the Service Check Adapter
hand tight¹ only.
9. Thread the male end of the Fill/Purge Valve
(3)
into a lower 1/2” port of the HS-808 until tight¹.
Orient the Fill/Purge Valve so that the handle can be operated comfortably once the HS-808 is
installed. The opposite end of the Fill/Purge Valve has a 3/4” male garden hose thread (GHT) port
and includes a brass cap with plastic tether. The plastic tether should slide over the end of the GHT
port end of the Fill / Purge Valve. The brass cap, with EPDM gasket included, should be threaded on
to the GHT port of Fill / Purge Valve until ready to use.
10. Install the insulation shell,
(7) & (8)
on the back side first, then on the front side. Push the two
halves together and then use the aluminum tape
(9)
to seal the seams and keep the two halves of
the insulation shell together.
1Note: These parts seal together and to the manifold with an EPDM gasket (o-ring). One quarter (1/4) turn beyond
“hand-tight” is normally sufficient to seal properly. If turning beyond 1/4 turn is required to align gauges and
handles then do so, up to one (1) full turn beyond “hand-tight”.
PART
1 Body
2
Automatic Air Vent w/ Check
3
Drain Valve w/ GHT
4 Temp. / Pressure Port Plug
5
Adhesive Insulation Ring Lg (x4)
6
Adhesive Insulation Ring Sm (x3)
7
Insulation Shell, front
8
Insulation Shell, back
9 Insulation Tape
10 O-Ring
11 MPT body adapter
12 Adapter gasket
13
Union nut
1
2
6
8
4
5
11
10
12
13
9
3
7
Maintenance
A. Air Vent cleaning
(as recommended by system designer, typically once per year minimum) – Remove the
air vent from the 1/4” x 1/2” service check adapter by un-threading counter-clock wise, as quickly as possible.
While un-threading the air vent from the check valve, a small amount of system fluid may leak (drip) out, but
should stop upon final removal from the check valve. This is normal as the check valve mechanism does not
complete close off until the air vent is fully removed. Un-thread the cap on the air vent, counter-clock wise
and remove the internal plastic components. Rinse the plastic components with clean water to wash off any
debris. Check and rinse, as needed, any debris from within the brass air vent body prior to reinserting the plastic
components. Re-attached the air vent cap by tightly threading clock-wise onto the air vent body. Replace the air
vent back into the 1/4” female threads of the check valve, hand tight only.
B. Debris blow out
(as recommend by system designer, typically within 1 week of system start-up and a
minimum of once per year thereafter) – If possible, close the isolation valves for the HS-808 to isolate it from
system pressure. If isolation valves have not been installed, the following instructions can still be followed;
however special care should be used when opening the drain valve as excessive loss of system fluid may occur.
Remove the brass cap from the GHT on the drain valve. Attach a drain hose with GHT female connection to
the end of the drain valve and locate the open end of the hose in a bucket or suitable drain location. Open the
drain valve (no more than 2 seconds at a time if the HS-808 has not been isolated) to allow the debris collected
at the bottom of the HS-808 to blow out through the hose and into the bucket or suitable drain location. Once
completed, remove the hose from the drain valve and re-install the cap.
C. Check system pressure
into the HS-808, slowly reapply system pressure and check for leaks. Once it’s
confirmed that there are no leaks, the system can be put back into operation. Especially if no isolation valves were
used, you may need to repeat the fill/purge procedures recommended by the system designer to replace lost fluid
and repressurize the system.