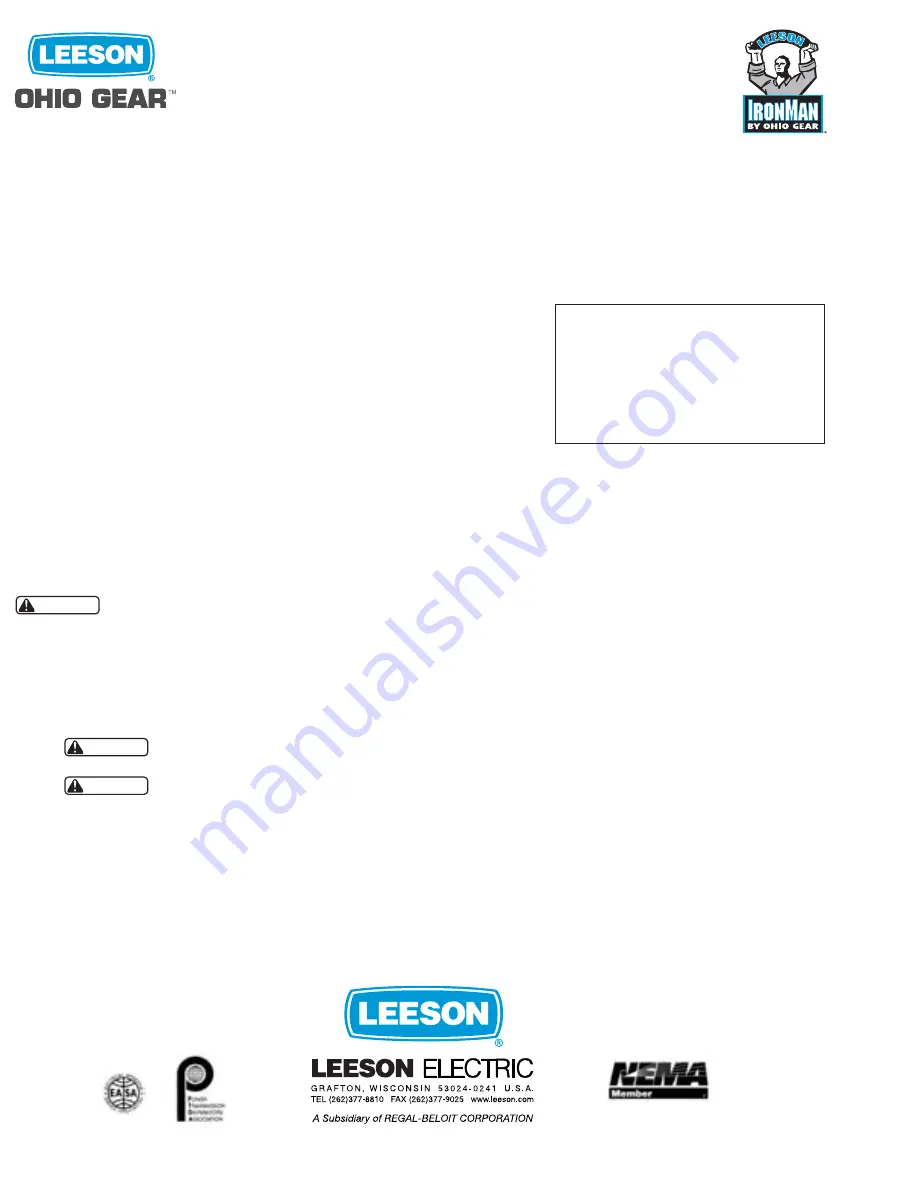
Maintenance
Your
IRONMAN BY OHIO GEAR™
reducer has been tested and adjusted at the factory. Dismantling or replacement of components must be
done by LEESON to maintain the warranty.
Inspect the stem of the Enviro-Seal often to ensure it is clean and operating properly.
Mounting bolts should be routinely checked to ensure that the unit is firmly anchored for proper operation.
Seals: The
IRONMAN BY OHIO GEAR™
line of speed reducers utilize premium quality seals which are state-of-the-art in sealing technology.
Seals are, however, a wear item and eventually need to be replaced. Replacement can easily be accomplished by following the procedure on page
5.
If seal leakage has resulted in the loss of a significant amount of oil, it may be necessary to add more lubricant. For normal ambient temperature
conditions, LEESON recommends Mobil SHC 634 synthetic gear oil for worm drives, and Mobil SHC 150 for helical drives.
CAUTION
Always check for proper oil level after filling. Do not overfill or underfill with oil, or injury to personnel, reducer, or
other equipment may result.
Do not mix different oils in the reducer.
Class of Service
All capacity ratings are based on proper application of American Gear Manufacturers Association (AGMA) service factors as given on page 174
of the IRONMAN BY OHIO GEAR™ 8050 Catalog. Load conditions must be within cataloged ratings published in the current LEESON Catalog
(available upon request).
Warranty From LEESON Electric -
See 8050 catalog pages 185-187 for warranty terms and conditions.
3395S/30M/9-02/SL/BH
CAUTION
CAUTION
Instruction Manual
Items Included in “C” Flange Adapter Kit
9/02 REV. 01
Specifications and prices are subject to change without notice.
© LEESON ELECTRIC, 2002
5.
Rotate input shaft of reducer to position the set screw (ref. 113) in line with access hole provided in the “C” flange adapter, tighten set screw
(make sure key is properly in place under set screw).
6.
Slide plastic sleeve (ref. 115) over reducer hub until it comes to a stop.
7.
Discard motor key and install key supplied in kit (ref. 118) flush with motor shaft end. Install coupling hub (ref. 117) flush with end of motor
shaft and tighten set screw (ref. 116), make sure key is under set screw.
8.
Install motor by sliding hub into sleeve until it comes to a stop. Install capscrews (ref. 47) and tighten to torque specified on tightening torque
chart.
9.
Install plastic plug (ref. 120) into the “C” Flange Adapter access hole.
1. One “C” Flange Adapter (ref. 110)
2. Four capscrews (ref. 42) adapter to reducer
3. One reducer coupling hub (ref. 114)
4. One reducer input key (ref. 112)
5. One reducer hub set screw (ref. 113)
6. Four capscrews (ref. 47), motor to adapter
7. One coupling sleeve (ref. 115)
8. One motor coupling hub (ref. 117)
9. One motor shaft key (ref. 118)
10. One motor hub set screw (ref. 116)
11. One access hole plug (ref. 120)
Capscrew Tightening Torque
Grade 5 Capscrews (dry, without lubricant)
Capscrew Size
Tightening Torque
(lb.-in.)
1/4 UNC
75
5/16 UNC
155
3/8 UNC
275
1/2 UNC
780