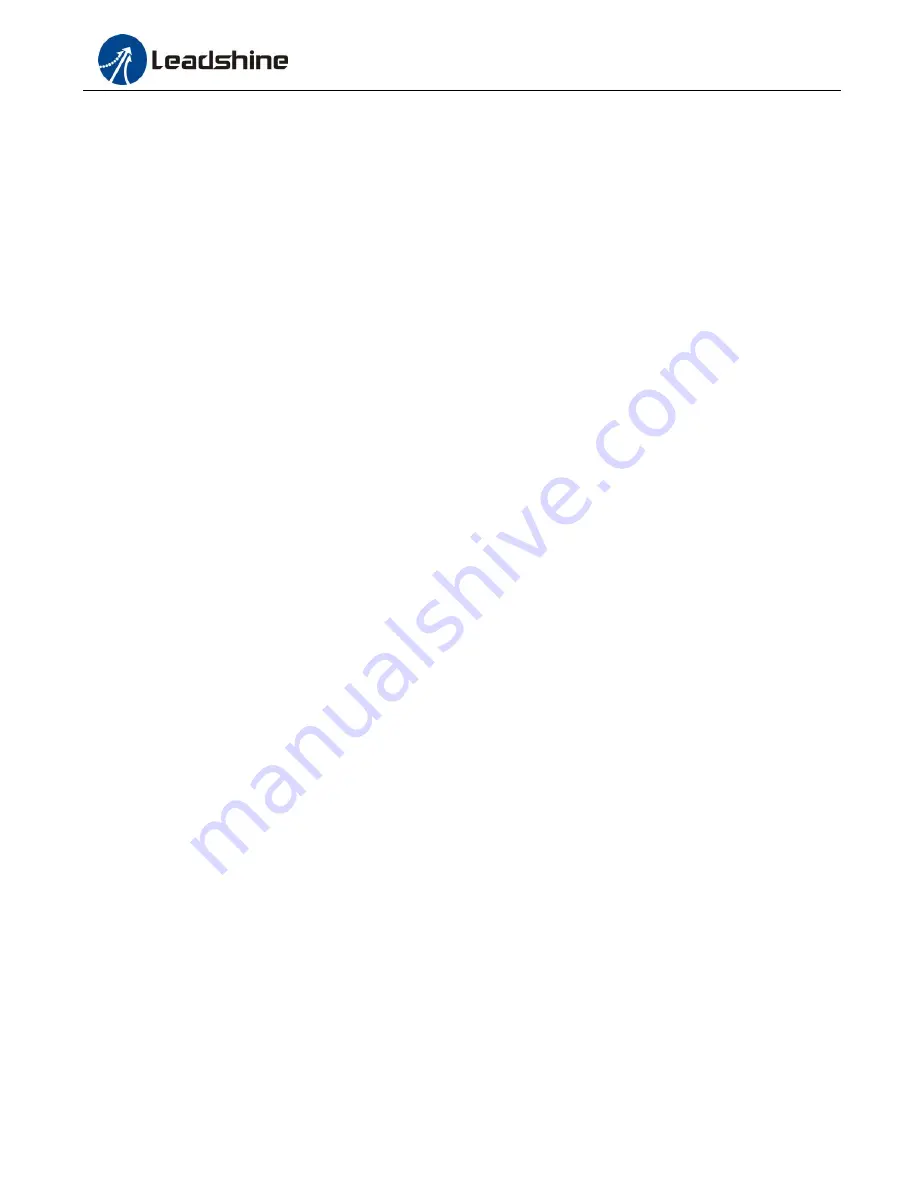
EM556S Digital Stepper Drive User Manual
Page | 10
7.6 Alarm Output Configuration (SW12)
DIP switch SW12 is used to configure the impedance state of alarm output (fault output). At OFF position (default) the
resistance between ALM+ and ALM- is set to low impedance in normal operation, and will change to high impedance
when the drive goes into over-voltage or over-current protection. When SW12 is set to ON position, that resistance will
be set to high impedance in normal condition and changed to low impedance under error protections.
7.7 Pulse Edge Configuration (SW13)
DIP switch SW13 is used to configure which voltage edge will activate a pulse signal. Set it to OFF position (default)
means that a pulse is activated at voltage rising edge, and ON position means a pulse is activated at falling edge. Make
sure this setting will match the pulse generator (controller, PLC, etc.)
7.8 Control Mode Configuration (SW14)
DIP switch SW14 is used to configure the control mode of EM556S. By default it is set to OFF position for single
pulse (step & direction, or pulse & direction) control. To change the control model to double pulse (CW/CCW) control
type, set its position to OFF.
7.9 Shaft Lock Configuration (SW15)
Use DIP switch SW15 to set shaft lock mode when EM556S is disabled (read ENA+ and ENA- explanation of control
connector for how to disable EM556S). Set it to OFF position (default) for no motor shaft lock (free spin) when drive
disabled. Set it to ON position for motor shaft lock.
7.10 Self-Test Configuration (SW16)
For test and system diagnosis purpose, EM42 is featured with Self-Test. Anytime DIP switch SW16 is switched to ON
position, the drive will automatically rotate the driven stepper motor back and forth for one round in each direction. Set
this switch position to OFF for normal operation.
8. Wiring Notes
In order to improve anti-interference performance of the drive, it is recommended to use twisted pair shield cable.
To prevent noise incurred in PUL/DIR signal, pulse/direction signal wires and motor wires should not be tied up
together. It is better to separate them by at least 10 cm; otherwise the disturbing signals generated by motor will
easily disturb pulse direction signals, causing motor position error, system instability and other failures.
If only one power supply serves multiple EM556S drives, separately connecting the drives to the power supply is
recommended instead of daisy-chaining.
It is prohibited to pull and plug connector P4 while the drive is powered ON, because there is high current flowing
through motor coils (even when motor is at standstill). Pulling or plugging connector P4 with power on will cause
extremely high back-EMF voltage surge, which may damage the drive.
9.
Typical Connection
A complete stepping system should include stepping motor, stepping drive, power supply and controller (pulse
generator). A typical connection is shown as figure 11.