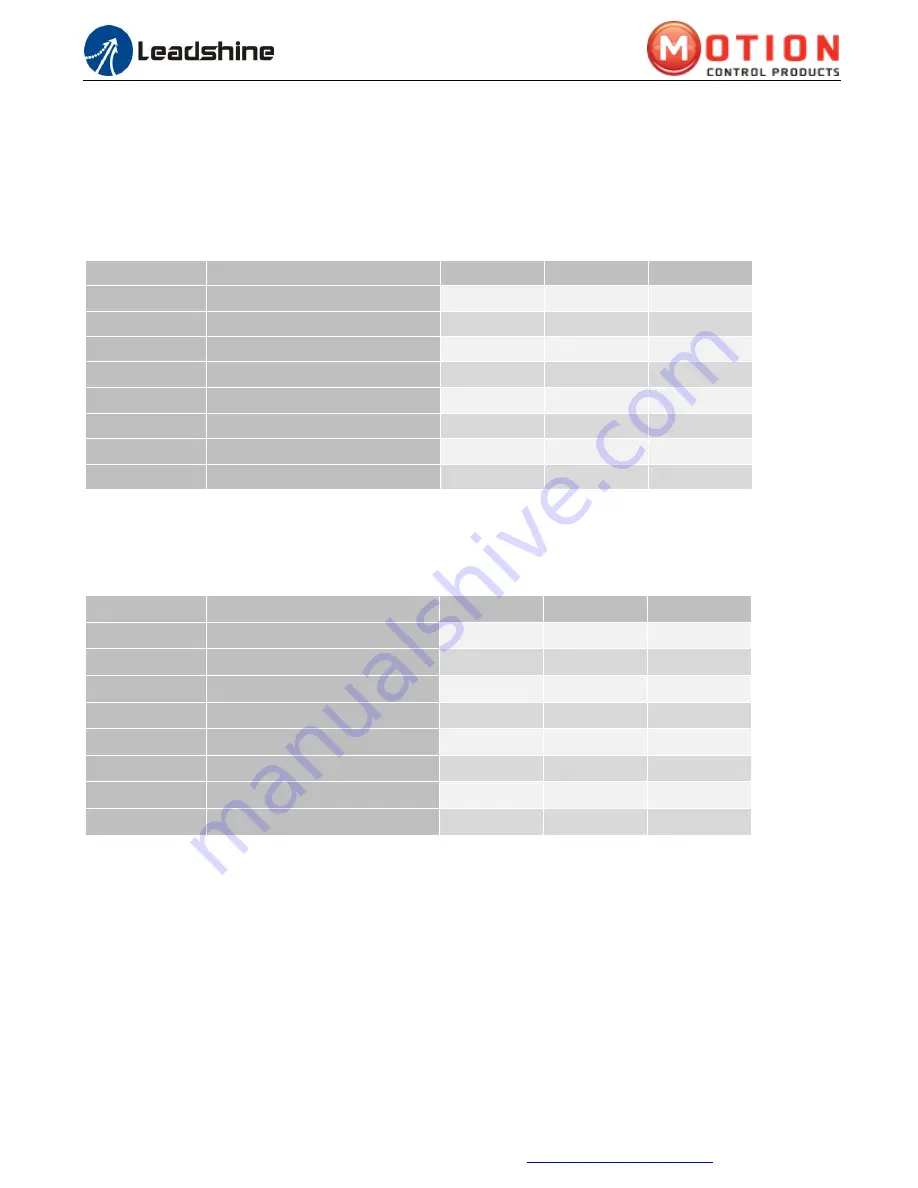
EM415S Digital Stepper Drive User Manual
Motion Control Products Ltd.
Tel.: (+44) 01202 599922
For a given stepper motor, as normal setting the output current to 1.4 times of motor phase current, will make it
output larger torque, but at the same time cause more heating for both the motor and drive. Therefore, it is
suggested to set a output current
(peak of sinusoidal) to no more than 1.2 times the stepper motor’s
(for 4-lead
motor) phase current to prevent overheating .
The SW1, SW2 and SW3
are used to set the dynamic current. Select a setting closest to your motor’s required curr
ent.
When they are set to
ON, ON, ON,
the output current can be set by Leadshine ProTuner.
Peak Current
RMS Current
SW1
SW2
SW3
0.3A
0.21A (default)
ON
ON
ON
0.5A
0.35A
OFF
ON
ON
0.6A
0.42A
ON
OFF
ON
0.7A
0.49A
OFF
OFF
ON
0.8A
0.57A
ON
ON
OFF
1.0A
0.71A
OFF
ON
OFF
1.2A
0.85A
ON
OFF
OFF
1.5A
1.06A
OFF
OFF
OFF
7.2 Micro Step Configuration (SW4-6)
Each EM415S has 8 micro step settings which can be configured through DIP switch SW4, SW5, SW6. See the
following table for detail. When they are set to
ON, ON, ON
, the microstep can be set via Leadshine ProTuner.
Micro step
Pulses/Rev. (for 1.8°motor)
SW4
SW5
SW6
1
200 (default)
ON
ON
ON
2
400
OFF
ON
ON
4
800
ON
OFF
ON
8
1600
OFF
OFF
ON
16
3200
ON
ON
OFF
32
6400
OFF
ON
OFF
64
12800
ON
OFF
OFF
128
25600
OFF
OFF
OFF
7.3 Pulse Mode Configuration (SW7)
DIP switch SW7 is used to configure the control mode. Factory setting is single pulse (step & direction, or pulse &
direction) control. Setting to ON to change the control model to double pulse (CW/CCW) control type.
7.4 Self-Test Configuration (SW8)
For test and system diagnosis purpose, EM442S is featured with Self-Test. Anytime DIP switch SW8 is switched to ON
position, the drive will automatically rotate the driven stepper motor back and forth for one round in each direction.
Set this switch position to OFF for normal operation.