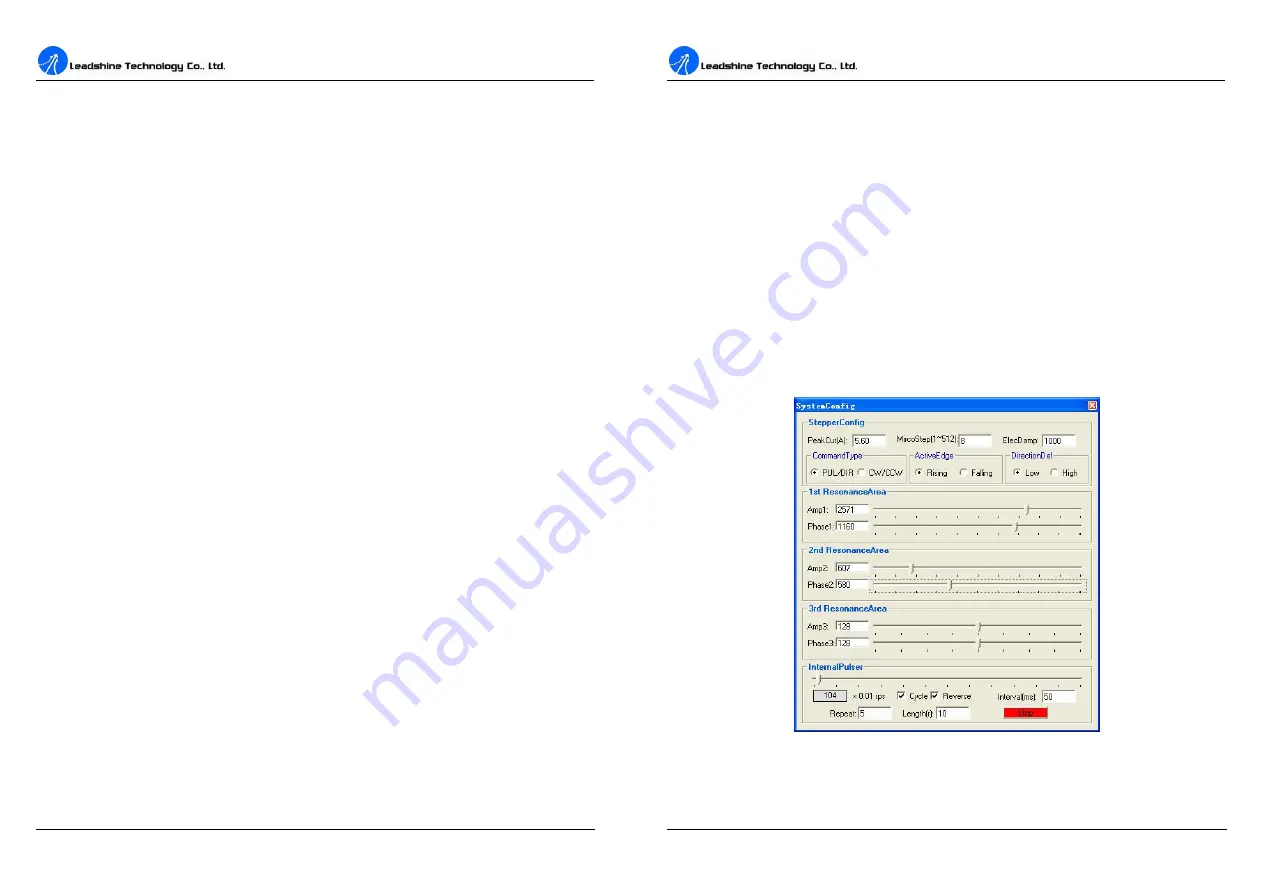
DM856 Digital Stepping Driver Manual V1.0
Tel: +000 0000-00000000 25
Anti-Resonance Introduction
Step motors are highly resonant, which results in vibration and ringing. The ringing utilizes a large
fraction of the motor's available torque
–
thereby wasting performance. Furthermore, at mid-range
velocities, the resonance can become so severe that the motor looses synchronization and stalls. The
DM856 driver provides robust anti-resonance control to stop the vibrations and maintain equilibrium.
This feature requires that the driver be configured with respect to the total inertia in the system. If set
improperly, the effectiveness of the feature may be diminished.
The user can invoke or disable the feature by setting
Amp
and
Phase
values in
SystemConfig
window.
Amp
and
Phase
values all zero is to disable the feature, otherwise is to invoke the feature. It
should be enabled unless the system configuration either does not need it or cannot tolerate it. A
system with loose couplings or viscous loading generally does not need this feature. If a system has
compliant (springy) coupling and is absent appreciably viscosity, it may not respond well to the active,
anti-resonant loop in the drive. The anti-resonant feature is not designed to damp such a 4
th
order
system. If the application of anti-resonance results in degradation or instability, it should be disabled.
1
st
ResonanceArea: Parameters for 1
st
resonance area.
Usually between 0.6rps and 1.2rps.
Amp1
is Amplitude adjustment for 1
st
resonance area.
Phase1
is Phase adjustment for 1
st
resonance area. The user can enter a value directly in the text box
or move the slider bar back and forth to get an optimum value.
2
nd
ResonanceArea: Parameters for 2
nd
resonance area.
Usually between 1.2rps and 2.4rps.
Default
Amp2
and
Phase2
values are zero.
3
rd
ResonanceArea: Parameters for 3
rd
resonance area.
Usually between 2.4rps and 4.8rps. Default
Amp3
and
Phase3
values are 128.
InternerPulser:
There is an internal pulse generator designed for driver self-testing and
anti-resonance tuning. You can issue a motion by this simple controller.
Cycle
check box: The motion will repeat if this box is checked.
Reverse
check box: The motor shaft will reverse direction if this box is checked.
Interval
edit box: The stop time between each cycle, unit is
millisecond
.
Repeat
edit box: Total
motion cycles.
DM856 Digital Stepping Driver Manual V1.0
Tel: +000 0000-00000000 26
Length
edit box: Move distance of each cycle, unit is
revolution
.
Start/Stop
button: The user can Start/Stop a motion test by clicking this button.
Procedure for Achieving Optimum Performance
Step 1:
Start the motion test by clicking
Start/Stop
button. Find an resonance speed by slightly
moving the slider bar of internal pulse generator back and forth. See Figure 26.
Step 2:
Run the motor at the resonance speed and verify the motor smoothness. You may find a better
smoothing value by slightly moving the slider bars of
AMP
(s) and
Phase
(s) back and forth.
It is very important to make the
AMP
(s) and
Phase
(s) adjustments at the proper test speeds with an
unloaded motor. Running at an incorrect test speed will not excite the motor at its peak resonance,
making it more difficult to find proper adjustment values. Optimum
AMP
(s) and
Phase
(s) values may
be a little different between running the tests with an unloaded motor and a load motor.
Please remember to click
SavetoDrive
to download the final parameter settings to the driver when
finish tuning. See Figure 27.
Figure 26: Anti-resonance tuning