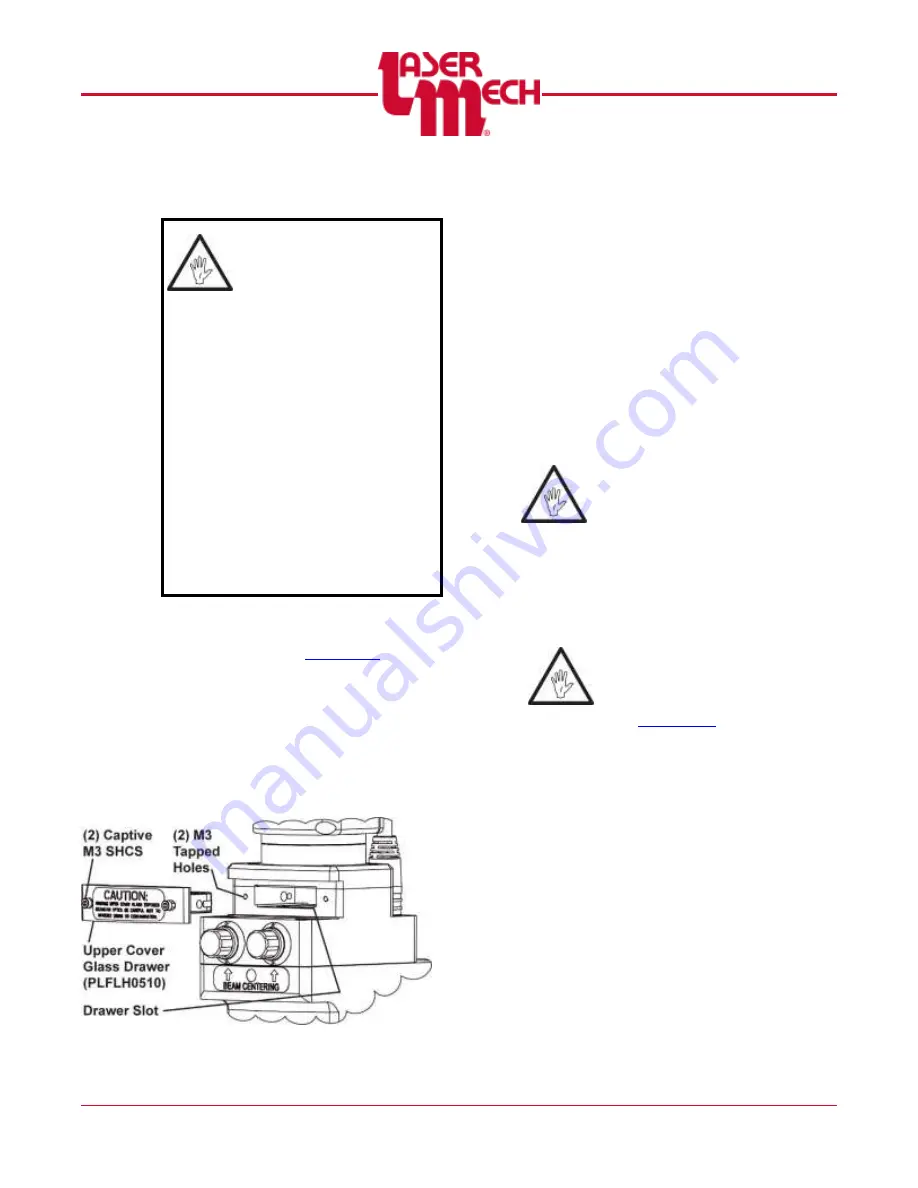
PLMNL0232 REV. H Effective Date: 01/14/19
41
FiberCUT
®
2D Operation Manual
5.3.2 Servicing the Upper Cover Glass
REMOVING THE UPPER
COVER GLASS DRAWER
RUNS THE RISK OF THE
FOLLOWING:
Contamination in the
collimating optics and/or
fiber.
Possible destruction of the
collimating optics and/or
fiber.
ONLY REMOVE THE UPPER COVER
GLASS DOOR WHEN:
The fiber has been removed.
The upper cover glass
experiences a temperature
fault.
1. Clean the outside of the head
2. Loosen the (2) captive M3
SHCS securing the upper cover
glass drawer (PLFLH0510) to
the head.
3. Pull the drawer straight out to
remove it from the head.
Figure 54
For steps 4 to 7, see
4. Protect the cover glass with
blue painter’s tape, or
equivalent, and take to a clean
area.
5. Remove the cover glass from
the drawer by applying
pressure with your fingers to
the surface of the cover glass,
opposite the seal.
The seal ring and cover
glass will pop out.
Inspect the seal ring.
There MUST be NO dirt, process
debris or any type of
contamination on the seal.
o
Replace the seal ring if
it is contaminated.
o
Save the seal ring if it is
in good condition.
Laser Mechanisms recommends
changing the seal ring
(PLMSR0030) on the upper lower
cover glass
EVERY
time you
replace the upper cover glass.
See
6. Install a new cover glass by
placing it into the drawer.