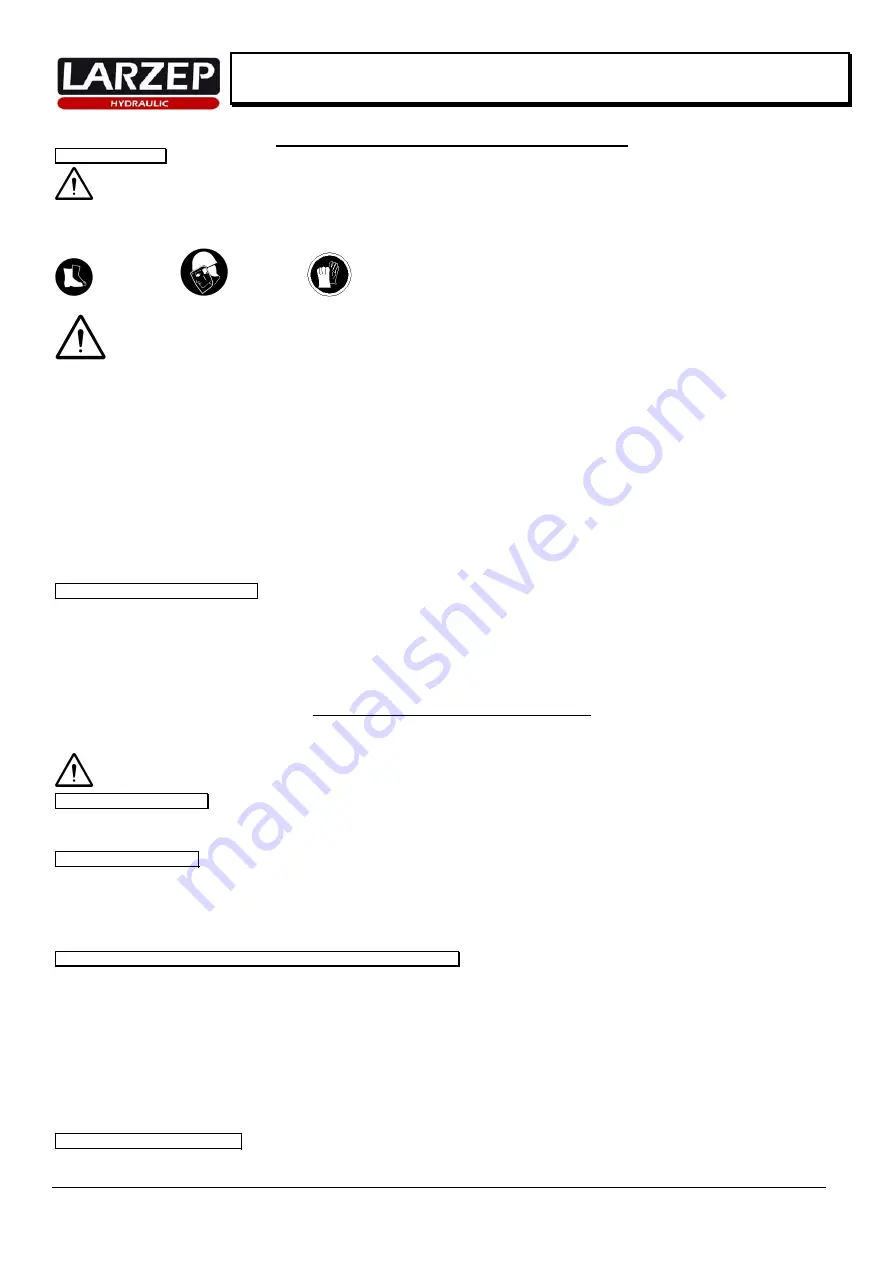
3
Instruction Manual
Bench Handpump press 20 ton “ECM02013”
3. ESSENTIAL SAFETY REQUIREMENTS.
DANGEROUS AREA
Due to the
FUNCTIONAL REASONS
it is considered to be the space between the columns, the bed and the hydraulic cylinder piston.
Due to the
MATERIAL PRESSED
it is supposed to be surrounding area to the machine in case of metal parts being ejected during pressing.
The speed of the hydraulic cylinder during its extension is less than 30 mm/second. Therefore then machine should be considered by the application of ANNEX V of
the Declaration of CE Conformity.
Operators standing in the dangerous area around the machine should protect their feet, faces and hands from metal pieces being ejected during pressing.
Feet protection
Face protection
Hands protection
Used materials and components are not for the health and safety of operators. The hand pump contains LARZEP hydraulic oil ISO:HV46.
HIDRAULIC OIL IS TOXIC IF IT ENTERS THE BLOODS STREAM. NEVER PLACE A FINGER OVER ANY ORIFICE OR LEAK, WHICH
COULD BE PRESSURIZED, SUCH AS THE HYDRAULIC LINE, AS THIS COULD CAUSE OIL TO BE INJECTED INTO BLOOD STREAM.
The pump lever performs the advance of the cylinder.
The pump includes an operating screw to relief the cylinder pressure that allows the oil return to the pump.
For the equipment working the connection of the pump to the cylinder is necessary.
In order to stop the advance pushing of the cylinder, we must stop operating the pump pedal. For a new start-up it is necessary to operate the pump pedal.
The construction of machine has been calculated to bear without any breaking under conditions of foreseen utilization and for the whole life of the machine.
The hydraulic components have been designed and calculated in compliance with the ANSI B30.1, and have been proved to 875Kg/cm
²
of pressing.
The frame of the machine does not cause to be dangerous in that sense.
The hydraulic pump is equipped with an internal security valve in the tank, out of operator’s control and rated at 700 Kg/ cm
²
. The hydraulic cylinder is also
furnisher with a pressure relief valve, rated at 700 Kg/ cm
²
, which prevents the retraction chamber of the cylinder from overpressures in case of obstruction
of the return way.
All the maintenance operations must be performed while the machine is stopped, thus avoiding this way any potentially dangerous situation. A poor
maintenance program of the press does not increase the risk, but obviously will revert in a lower performance.
The hydraulic pump is mounted out of the frame and access is very easy. To disassemble the pump unscrews the bolts in the tap cover. In order to
disassemble the cylinder it is required first to disassemble the hose and the cylinder from the frame.
ISOLATION OF THE POWER SUPPLY
Release the rapid coupling from the pump.
The machine is designed to assure that the operator performs all maintenance tasks in an easy and safe way. All the components that would require any
maintenance operation are easy accessible.
The press, the cylinder and the pump have their corresponding serial numbers marked on them. In addition to it, you can find a sticker label showing the commercial
reference, capacity, working pressure, name and address of the manufacturer.
4. TRANSPORT AND ERECTION.
The machine is delivered properly packed in a wooden ballet. For it’s handling, it is recommended to use a forklift truck or a crane. In the last case, it is necessary to
make the slings trespass the arc of the frame. When doing this operation, you should be cautious and prevent the flexible hoses and couplings from any damage.
The machine is stable enough to operate without fixing, but if is placed in an area commonly operated by mobile machinery (cranes, lifting equipment…)
it is strongly recommended to fix it to the desired place by drilling the supporting plates.
HYDRAULIC CONNECTION
Unscrew the rapid coupler site in the cylinder, and connect the hose, screwing the rapid coupler to the limit with the hand.
INSTALLING THE GAUGE
1-Replace the threaded tap in the top of the cylinder by the gauge. (Supplied separately)
2-Tighten the gauge cone to the gauge adaptor seat by using a flan wrench size 22.
3-Hold the gauge screen by hand during threading process and after reaching a comfortable reading position set the gauge screen free so that it turns the last quarter
solidarily with the thread.
CHECKING THE RIGHT OPERATION OF ALL DEVICES AND MECHANISM
1.
Select the working maximum pressure. In manual presses 700 Kg/cm
²
.
2.
With the hand in the lever, pump several times.
3.
Check the cylinder advance.
4.
Check that the cylinder piston return by internal spring. In both cases, to maintain the movement is necessary act over the lever.
5.
Without any material in the press, repeat the advance movement, pumping until reach the cylinder full stroke. In that moment the pressure will start to be
increased and we can observe it now in the gauge. This pressure will go on increasing until reach the installation maximum pressure, previously chosen.
In this stage, the cylinder maintains the reached pressure, (the gauge maintains the reading). Check there are no leaks in the installation (gauge intake,
couple, etc.)
6.
To return the cylinder and eliminate the installation pressure, open the washer turning it to the left. The return may be slower at the end of the backstroke.
7.
Put the material to be treated in the press.
MAXIMUM WORKING PRESSURE
The maximum pressure developed by the hydraulic system is 700 Kg/cm
²
. An internal security valve discharges when the system reaches that pressure.
Содержание KC02013
Страница 5: ...5 Instruction Manual Bench Handpump press 20 ton ECM02013 7 DECLARATION OF CONFORMITY ...
Страница 6: ...6 Instruction Manual Bench Handpump press 20 ton ECM02013 GENERAL DRAWING Nº 1 ...
Страница 7: ...7 Instruction Manual Bench Handpump press 20 ton ECM02013 GENERAL DRAWING Nº 2 ...
Страница 8: ...8 Instruction Manual Bench Handpump press 20 ton ECM02013 GENERAL DRAWING Nº 3 ...