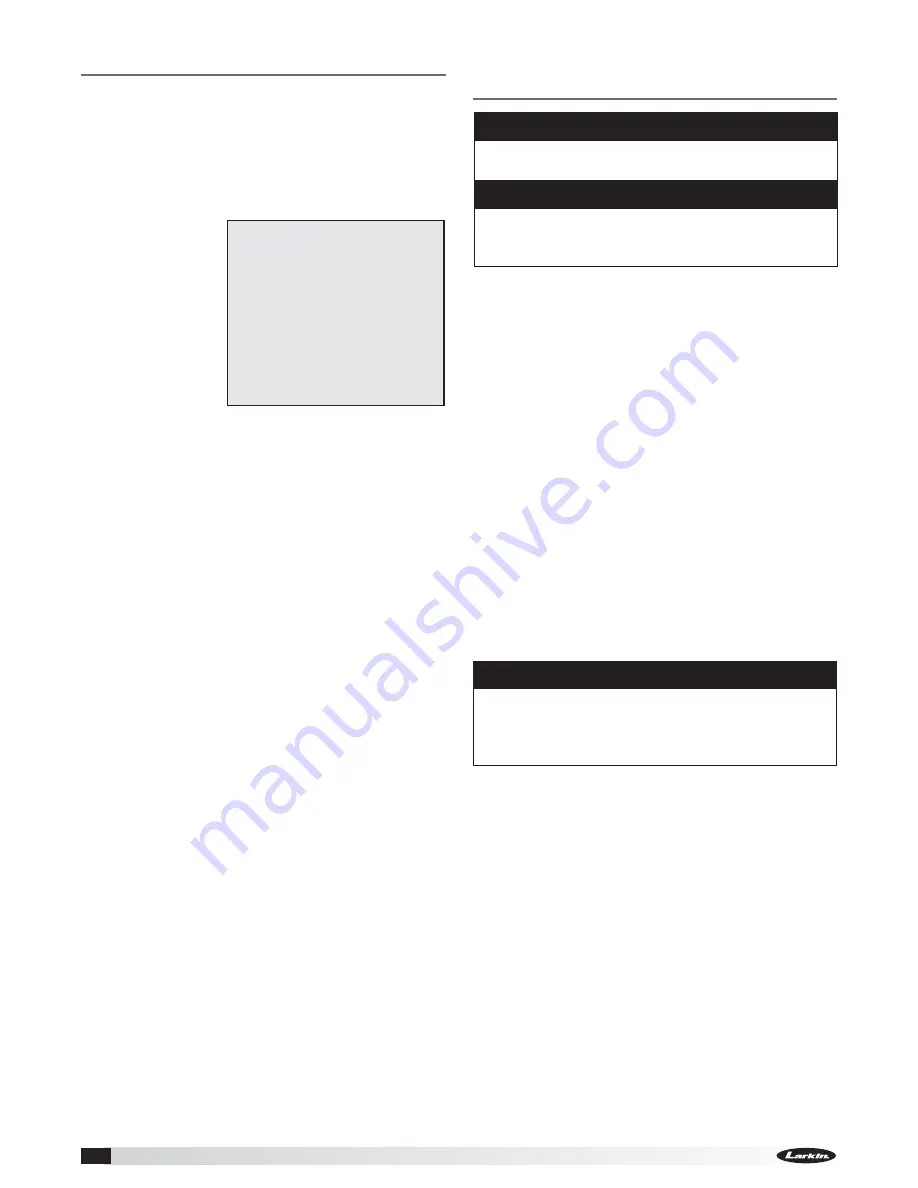
Utility Fans
12
Vibration
On start-up and during operation, the unit should
operate smoothly with minimal vibration. It is possible
that a higher degree of vibration may be experienced.
Excessive vibration if left unchecked, can cause a
multitude of problems, including structural and/or
component failure. The most common sources of
vibration are listed.
Many of these
conditions can
be discovered by
careful observation.
Refer to the
troubleshooting
section of this
manual for
corrective actions.
If observation
cannot locate
the source of vibration, a qualified technician using
vibration analysis equipment should be consulted. If
the problem is wheel unbalance, in-place balancing
can be done through the access panel located on
the side of each fan’s tubular housing. Any correction
weights added to the wheel should be welded to
either the wheel back (single-plane balance) or to the
wheel back and wheel cone (two-plane balance).
Common Sources of Vibration
1. Wheel unbalance
2. Drive pulley misalignment
3. Incorrect belt tension
4. Bearing misalignment
5. Mechanical looseness
6. Faulty belts
7. Drive component unbalance
8. Poor inlet/outlet conditions
9. Foundation stiffness
Once the unit has been put into operation, a
routine maintenance schedule should be set up to
accomplish the following:
1. Lubrication of bearings and motor.
2. Wheel, housing, bolts and set screws on the entire
fan should be checked for tightness.
3. Any dirt accumulation on the wheel or in the
housing should be removed to prevent unbalance
and possible damage.
4. Inspect fan impeller and housing looking for fatigue,
corrosion, or wear.
Fan Operation
All fans should be run every thirty (30) days, or at least
“bumped” every thirty days. It is preferred that each
fan is run as this causes all electrical and mechanical
components to get up to temperature, displacing any
formed condensation, redistributes load on bearings,
and redistributes grease in the bearings (motor and
shaft bearings).
IMPORTANT
When operating conditions of the fan are to be
changed (speed, pressure, temperature, etc.),
consult manufacturer to determine if the unit can
operate safely at the new condition.
Motors
Motor maintenance is generally limited to cleaning
and lubrication. Cleaning should be limited to exterior
surfaces only. Removing dust and grease buildup
on the motor housing assists proper motor cooling.
Never wash down motor with high pressure spray.
Greasing of motors is only intended when fittings are
provided. Many fractional motors are permanently
lubricated for life and require no further lubrication.
Motors supplied with grease fittings should be
greased in accordance with the manufacturer’s
recommendations. When motor temperature does not
exceed 104ºF (40ºC), the grease should be replaced
after 2000 hours of running time.
Direct drive systems have extended grease lines to
lubricate the motor without removal of any guarding.
Routine Maintenance and
Operation
WARNING
Before taking any corrective action, make certain
unit is not capable of operation during repairs.
AVERTISSEMENT
Avant d’entreprendre toute action corrective,
s’assurer que l’appareil ne pourra pas fonctionner
durant les réparations.