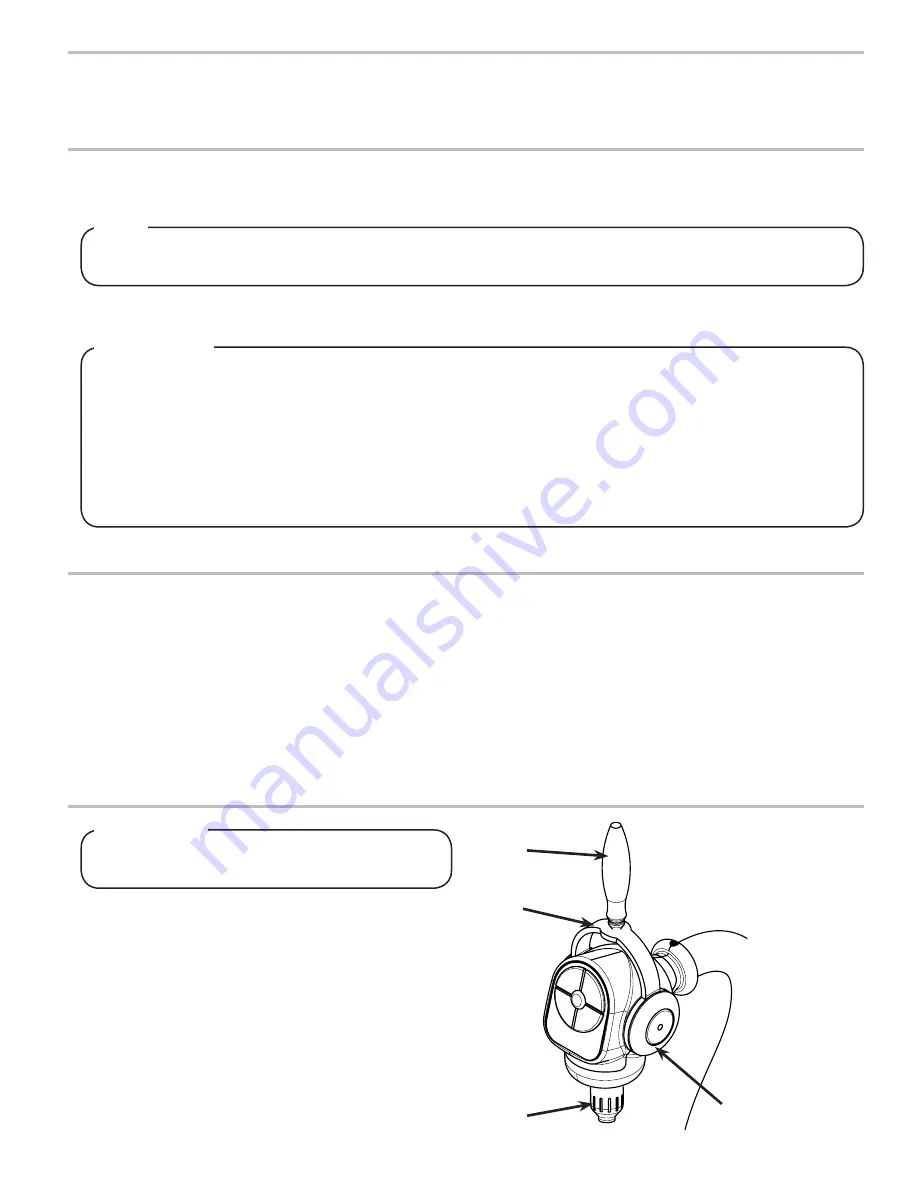
15
General Information
CLEANING AND SANITIZING
•
Lancer equipment (new or reconditioned) is shipped from the factory cleaned and sanitized in accordance with NSF guidelines.
The operator of the equipment must provide continuous maintenance as required by this manual and/or state and local health
department guidelines to ensure proper operation and sanitation requirements are maintained.
The cleaning procedures provided herein pertain to the Lancer equipment identified by this manual. If other
equipment is being cleaned, follow the guidelines established by the manufacturer for that equipment.
• Use sanitary gloves when cleaning the unit and observe all applicable safety precautions.
• DO NOT
use a water jet to clean or sanitize the unit.
• DO NOT
disconnect water lines when cleaning and sanitizing syrup lines, to avoid contamination.
• DO NOT
use strong bleaches or detergents; These can discolor and corrode various materials.
• DO NOT
use metal scrapers, sharp objects, steel wool, scouring pads, abrasives, or solvents on the dispenser.
• DO NOT
use hot water above 140° F (60° C). This can damage the dispenser.
• DO NOT
spill sanitizing solution on any circuit boards. Insure all sanitizing solution is removed from the system.
NOTE
•
Cleaning should be accomplished only by trained personnel. Sanitary gloves are to be used during cleaning operations.
Applicable safety precautions must be observed. Instruction warnings on the product being used must be followed.
!
ATTENTION
Unplug the dispenser before servicing, cleaning, or
sanitizing any of the equipment.
!
WARINING
Cleaning and Sanitizing Solutions
Cleaning Solution
Mix a mild, non-abrasive detergent (e.g. Sodium Laureth
Sulfate, dish soap) with clean, potable water at a temperature
of 90°F to 110°F (32°C to 43°C). The mixture ratio is one
ounce of cleaner to two gallons of water. Prepare a minimum of
five gallons of cleaning solution. Do not use abrasive cleaners
or solvents because they can cause permanent damage to the
unit. Ensure rinsing is thorough, using clean, potable water at a
temperature of 90°F to 110°F. Extended lengths of product lines
may require additional cleaning solution.
Sanitizing Solution
Prepare sanitizing solutions in accordance with the
manufacturer’s written recommendations and safety guidelines.
The solution must provide 100 parts per million (PPM) chlorine
(e.g. Sodium Hypochlorite or bleach). A minimum of five
gallons of sanitizing solution should be prepared. Any sanitizing
solution may be used as long as it is prepared in accordance
with the manufacturer’s written recommendations and safety
guidelines, and provides 100 parts per million (PPM) chlorine.
Daily Cleaning
1. Disconnect power to the unit.
2. Mix an appropriate amount of cleaning solution in a clean
container, then pour a small portion of the cleaning solution
in separate clean container (at least 3 inches deep).
3. Remove nozzle by twisting counterclockwise and pulling
down.
4.
Submerge the nozzle in the container with the smaller
portion of solution.
5.
Use a clean cloth soaked in the cleaning solution to
clean the tower and all exterior stainless steel surfaces.
6. Use the soaked cloth to wipe clean all splash areas.
7. Rinse nozzle in warm water then re-install on tower.
A
B
C
D
A. Ceramic Lever
B. Handle
C. Nozzle
D. Chrome Disk
Содержание UNICORN TOWER
Страница 27: ...27 Wiring Diagram LFCV...
Страница 28: ...28 Wiring Diagram VV...
Страница 29: ...29 Counter Cutout Not to Scale...