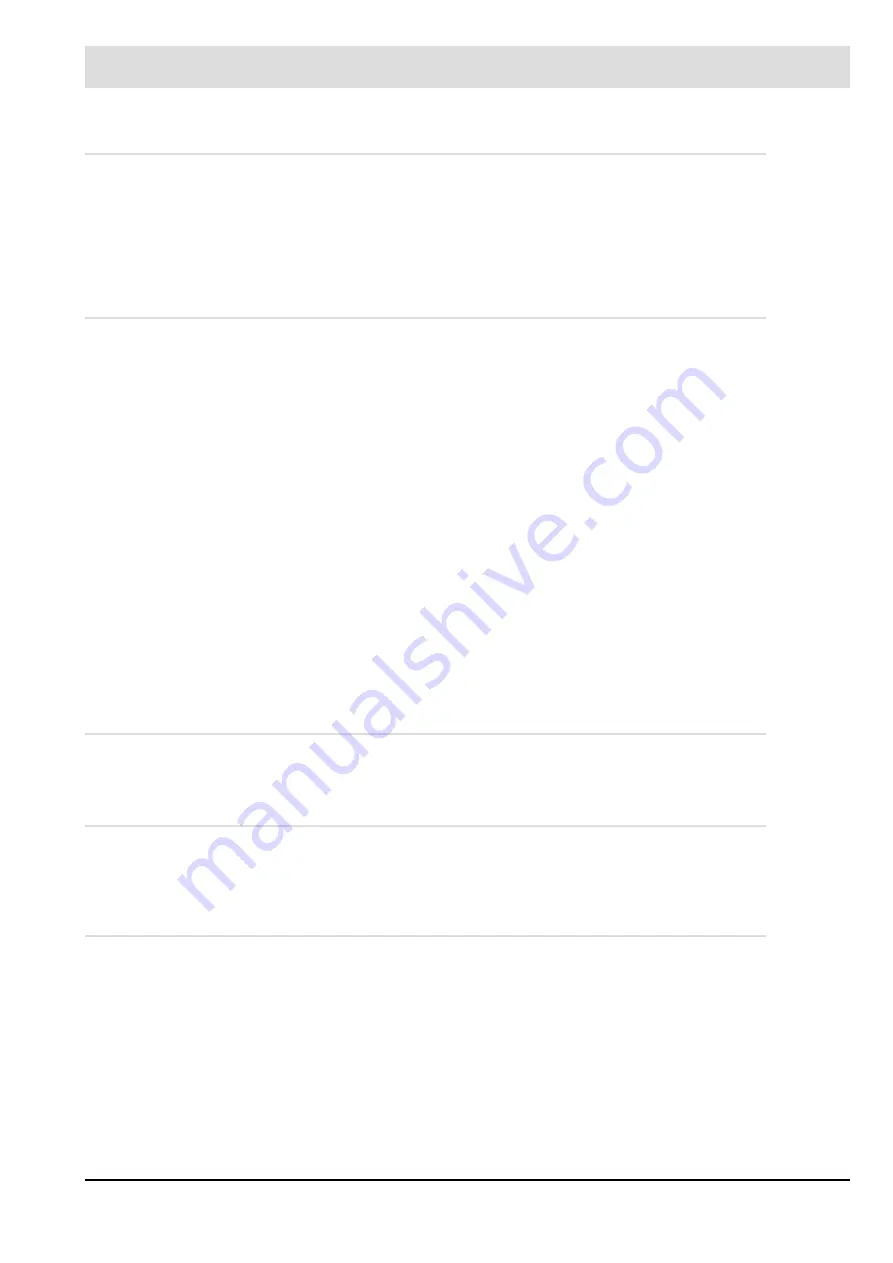
14
3
Operation
3.8
Flying Curve Change
If the select signal for the curve sets is changed whilst in operation, the VMS goes to fault 351.
With this option, however, it allows changing from one curve set to another.
The settings change abruptly.
The band monitorings are replaced for a period of 30 seconds by running direction monitoring.
After 30 seconds the control elements must have reached their new value.
3.9
Integrated Power Control Unit
An integrated power control unit is also available as an option. Where this (option) is used the
actual temperature or the actual pressure is directly switched instead of the firing rate signal.
The control parameters are adjusted via parameters. It is also possible to change the setting
(daytime/night time operation) and to control the atmospheric conditions by switching in the
outside temperature.
The integral output controller is a PID controller with special combustion technology functions.
It can be used as a fixed-value controller or as a weather-dependent controller. The following
signals can be set:
–
Actual value (analogue)
–
External temperature or some other analogue signal for target value shifting (only in
weather-dependent controllers)
–
Target value switching (via zero-potential contact)
Combustion enabling by the output controller takes place internally in the VMS
Boundary values that switch the burner on and off, need to be set via parameter setting. In this
case, the startup signal is removed internally from VMS via the output controller module.
The operator is alerted by the display (running text) that the output controller refuses to enable
a startup.
3.10
4 or 8 Curve Sets
The VMS has 2 curve sets as standard. 4 or 8 curve sets may be used, as an option.
3.11
Direct Connection to R. P. M. Sensor
An output for controlling the speed of a combustion air fan or a re-circulation fan etc. can be
monitored by switching the pulse output of a Namur transmitter directly to the VMS.
3.12
Fail-Safe Feedback
Continuous outputs and three-point step outputs have different feedback requirements.
In the case of continuous outputs comparisons are made between output and feedback values
in or to check the plausibility. The units therefore do not have to be intrinsically error-free in
order to form the feedback signal. For availability reasons (minimisation of interference) the
reproducibility of the values should be as good as possible.
For technical reasons this method cannot be used in the case of three-point step outputs. For
this reason TÜV approved potentiometers must be connected directly as feedback to the
VMS. These potentiometers must positively render the position of the damper.
Содержание VMS Series
Страница 1: ...www lamtec de Sensors and Systems for Combustion Technology Manual Fuel Air Ratio Control System VMS...
Страница 2: ......
Страница 119: ...118 10 Appendix...
Страница 121: ...120 10 Appendix 10 6 Process Sequence Charts Fig 10 3 Sequence of functions VMS digital inputs sequencer...
Страница 129: ...128 10 Appendix Fig 10 9 Ger t 4 Ger t 5 with output regulator...
Страница 141: ...140 10 Appendix 10 14 Declaration of Conformity...
Страница 142: ...141 10 Appendix...
Страница 143: ...142 10 Appendix 10 15 Protocol Example...
Страница 144: ...143 10 Appendix 10 16 O2 Setpoint Curves...
Страница 145: ...144 10 Appendix...