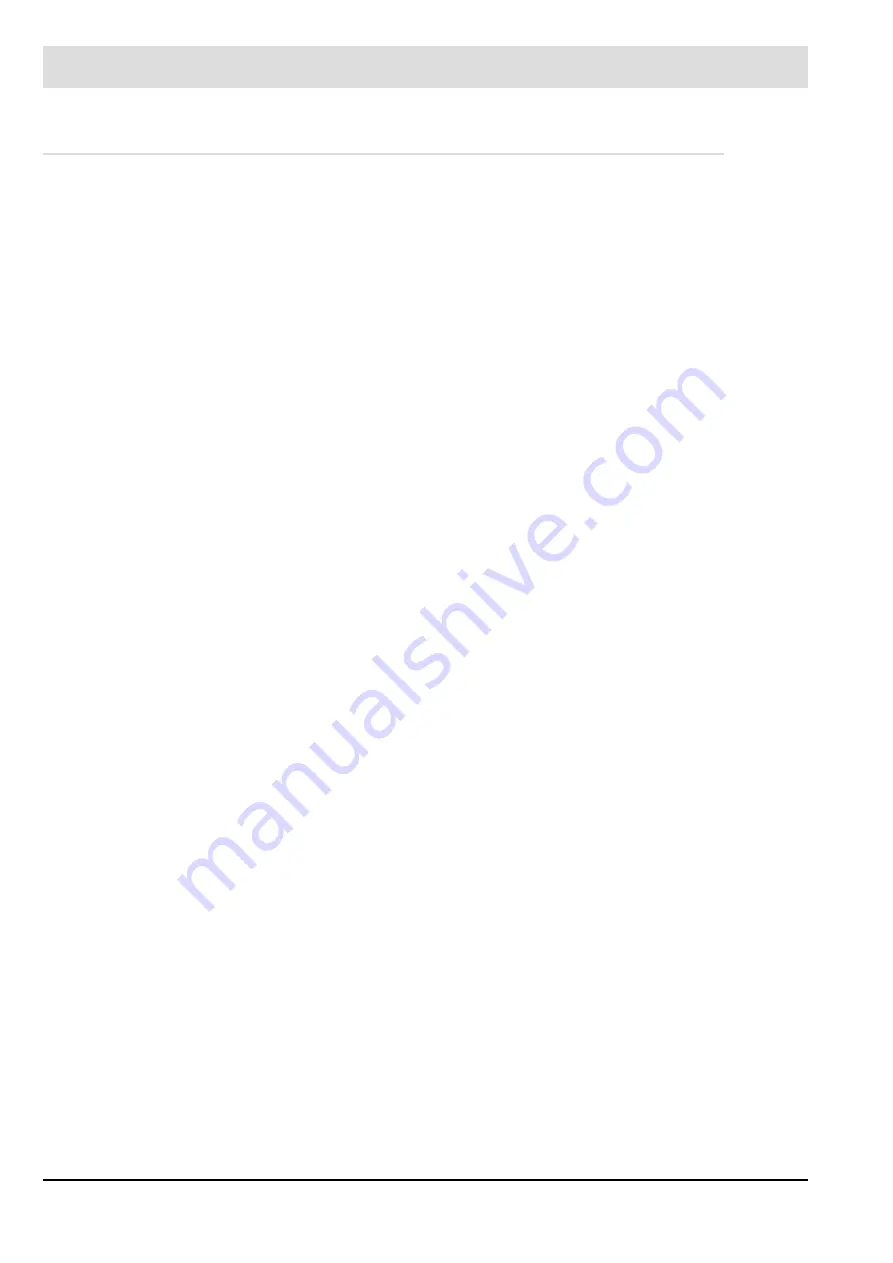
7
3
For Your Safety
3.1
Mounting Notes
•
Please consider protection against contact when installing the Gerät. Protection classes
as IP 40 - IP 54 are minimum requirements for outdoor use in accordance with EN 60529
and therefore obligatory.
•
The protective cover of the BurnerTronic may only be opened by trained, qualified person-
nel.
•
Make sure that settings for safety-relevant parameters are set in line with the requirements
applicable to each type of combustion requiring monitoring and conform to the applicable
standards (by checking device parameters via operating elements or using remote-control
software after commissioning). To verify settings you should also refer to manufacturer’s
documentation of the combustion plant. Protecting the parameters in level 1 by setting a
password will prevent any unauthorised change.
•
Save setting values for the actuating elements across the power range of the burner as
follows:
–
Quantity of fuel
–
Quantity of air
–
All additional, safety-relevant actuating variables of the combustion
–
While burner is modulating with at least five different firing-rate points
•
Make sure that the combustion equipment operates stably and safely throughout the pow-
er range and in all combustion modes. For this purpose you should adjust the following
values correctly:
–
Actuating elements
–
Parameter settings of the CO/O
2
controller
–
Combustion chamber pressure
–
Fuel pressure
–
Temperature
–
Pressure of combustion air
–
Heating value of fuel
•
Ensure the connection between the actuators and control valves is form-fit throughout,
gearing this towards the maximum controlling torques of the actuators.
•
Only use external flame monitors compliant with DIN EN 298 or DIN EN 230 and author-
ised for continuous operation. Safety time of flame monitor must not extend 1 s.
•
If the valve testing system is activated, connect the supply-side solenoid valve to terminal
X01 and the burner-side solenoid valve to terminal X02. Connect the pressure monitor of
the valve testing system to terminal X05. Adjust the gas pressure monitor and the dimen-
sions of the test section in order to make sure that the valve testing system is detecting a
maximum leakage gas volume of 0.1 % in relation to the gas flow rate (minimum 50 dm³/
h) at maximum combustion heat output.
•
Consider the potential danger depending on installation situation and position where the-
pressure equipment is being installed. Bear in mind the risk of external fire and the impact
from traffic, wind and earthquake.
•
When fixing duomodul plug-in connectors to insulation displacement technology (IDT) use
HZ-M35 a modular crimping tool from Lumberg (see www.lumberg.com).
Содержание BT300 BurnerTronic
Страница 2: ......
Страница 39: ...38 6 Leakage Test for Main Gas Valves Fig 6 2 Leakage test process diagram...
Страница 46: ...45 7 Technical Data...
Страница 47: ...46 7 Technical Data...