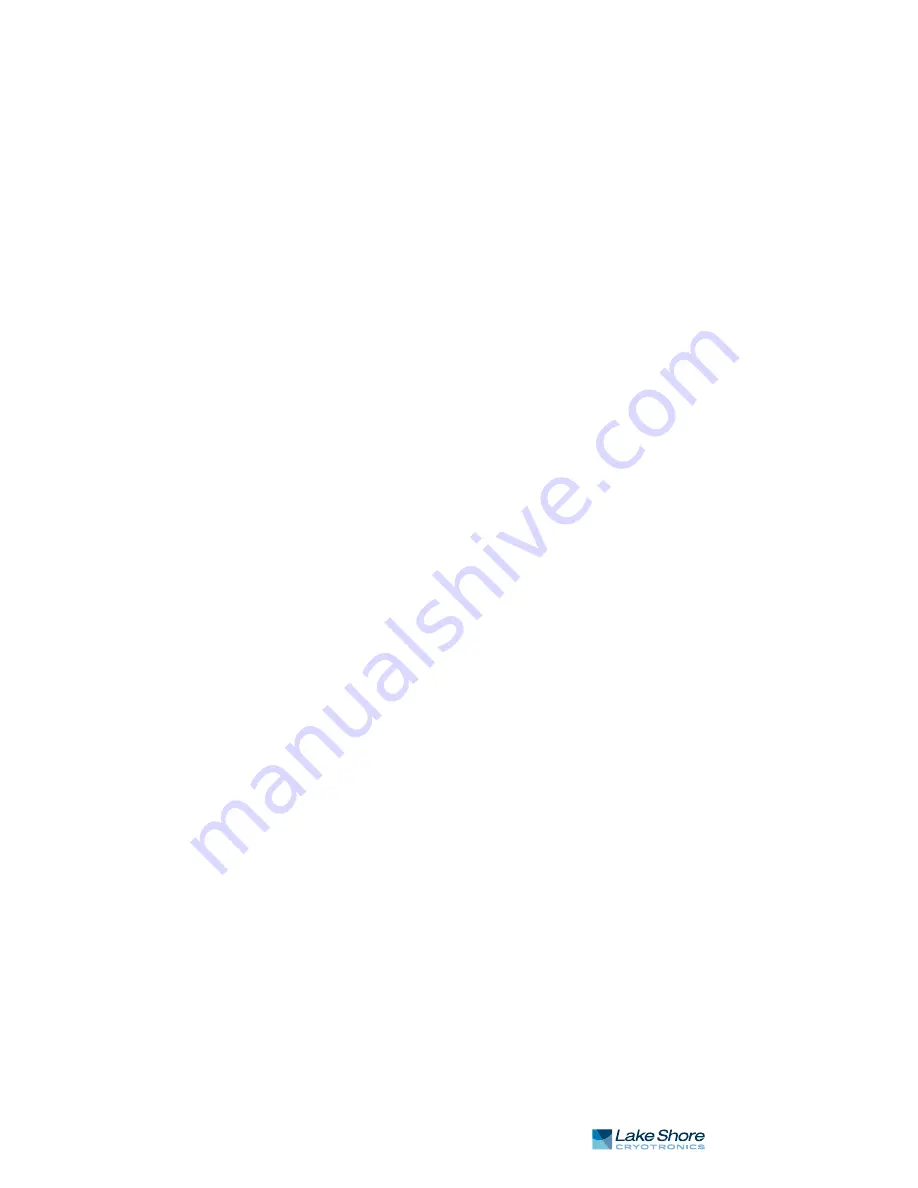
2.10.1 Mounting Materials
31
|
www.lakeshore.com
2.10.1 Mounting
Materials
Choosing appropriate mounting materials is very important in a cryogenic environ-
ment. The high vacuum used to insulate cryostats is one consideration. Materials
used in these applications should have a low vapor pressure so they do not evaporate
or out-gas and spoil the vacuum insulation. Metals and ceramics do not have this
problem, but greases and varnishes must be checked. Another consideration is the
wide extremes in temperature most sensors are exposed to. The linear expansion
coefficient of materials becomes important when temperature changes are large.
Never try to permanently bond materials with linear expansion coefficients that dif-
fer by more than three. Use a flexible mounting scheme or the parts will break apart,
potentially damaging them. The thermal expansion or contraction of rigid clamps or
holders could crush fragile samples or sensors that do not have the same coefficient.
Thermal conductivity is a property of materials that can change with temperature. Do
not assume that a thermal anchor grease that works well at room temperature and
above will do the same job at low temperatures.
2.10.2 Sensor Location
Finding a good place to mount a sensor in an already crowded cryostat is never easy.
There are fewer problems if the entire load and sample holder are at the same tem-
perature. Unfortunately, this not the case in many systems. Temperature gradients
(differences in temperature) exist because there is seldom perfect balance between
the cooling source and heat sources. Even in a well-controlled system, unwanted heat
sources like thermal radiation and heat conducting through mounting structures can
cause gradients. For best accuracy, position sensors near the sample, so that little or
no heat flows between the sample and sensor. This may not, however, be the best
location for temperature control as discussed below.
2.10.3 Thermal
Conductivity
The ability of heat to flow through a material is called thermal conductivity. Good
thermal conductivity is important in any part of a cryogenic system that is intended
to be the same temperature. Copper and aluminum are examples of metals that have
good thermal conductivity, while stainless steel does not. Non-metallic, electrically-
insulating materials like alumina oxide and similar ceramics have good thermal con-
ductivity, while G-10 epoxy-impregnated fiberglass does not. Sensor packages, cool-
ing loads, and sample holders should have good thermal conductivity to reduce
temperature gradients. Surprisingly, the connections between thermally conductive
mounting surfaces often have very poor thermal conductivity (refer to section 2.10.4
and section 2.10.5).
2.10.4 Contact Area
Thermal contact area greatly affects thermal conduction because a larger area has
more opportunity to transfer heat. Even when the size of a sensor package is fixed,
thermal contact area can be improved with the use of a gasket material like indium
foil and cryogenic grease. A soft gasket material forms into the rough mating surface
to increase the area of the two surfaces that are in contact. Good gasket materials are
soft, thin, and have good thermal conductivity. They must also withstand the environ-
mental extremes. Indium foil and cryogenic grease are good examples.
2.10.5 Contact
Pressure
When sensors are permanently mounted, the solder or epoxy used to hold the sensor
act as both gasket and adhesive. Permanent mounting is not a good solution for
everyone because it limits flexibility and can potentially damage sensors. Much care
should be taken not to over heat or mechanically stress sensor packages. Less perma-
nent mountings require some pressure to hold the sensor to its mounting surface.
Pressure greatly improves the action of gasket material to increase thermal conduc-
tivity and reduce thermal gradients. A spring clamp is recommended so that different
rates of thermal expansion do not increase or decrease pressure with temperature
change.
Содержание 350
Страница 4: ...Model 350 Temperature Controller ...
Страница 6: ......
Страница 14: ...Model 350 Temperature Controller ...
Страница 28: ...14 cHAPTER 1 Introduction Model 350 Temperature Controller ...
Страница 53: ...Examples of PID control 2 13 4 ManualOutput 39 www lakeshore com FIGURE 2 4 ...
Страница 58: ...44 cHAPTER 2 Cooling System Design and Temperature Control Model 350 Temperature Controller ...
Страница 118: ...104 cHAPTER 5 Advanced Operation Model 350 Temperature Controller ...
Страница 178: ...164 cHAPTER 7 Options and Accessories Model 350 Temperature Controller ...
Страница 192: ...178 cHAPTER 8 Service Model 350 Temperature Controller ...