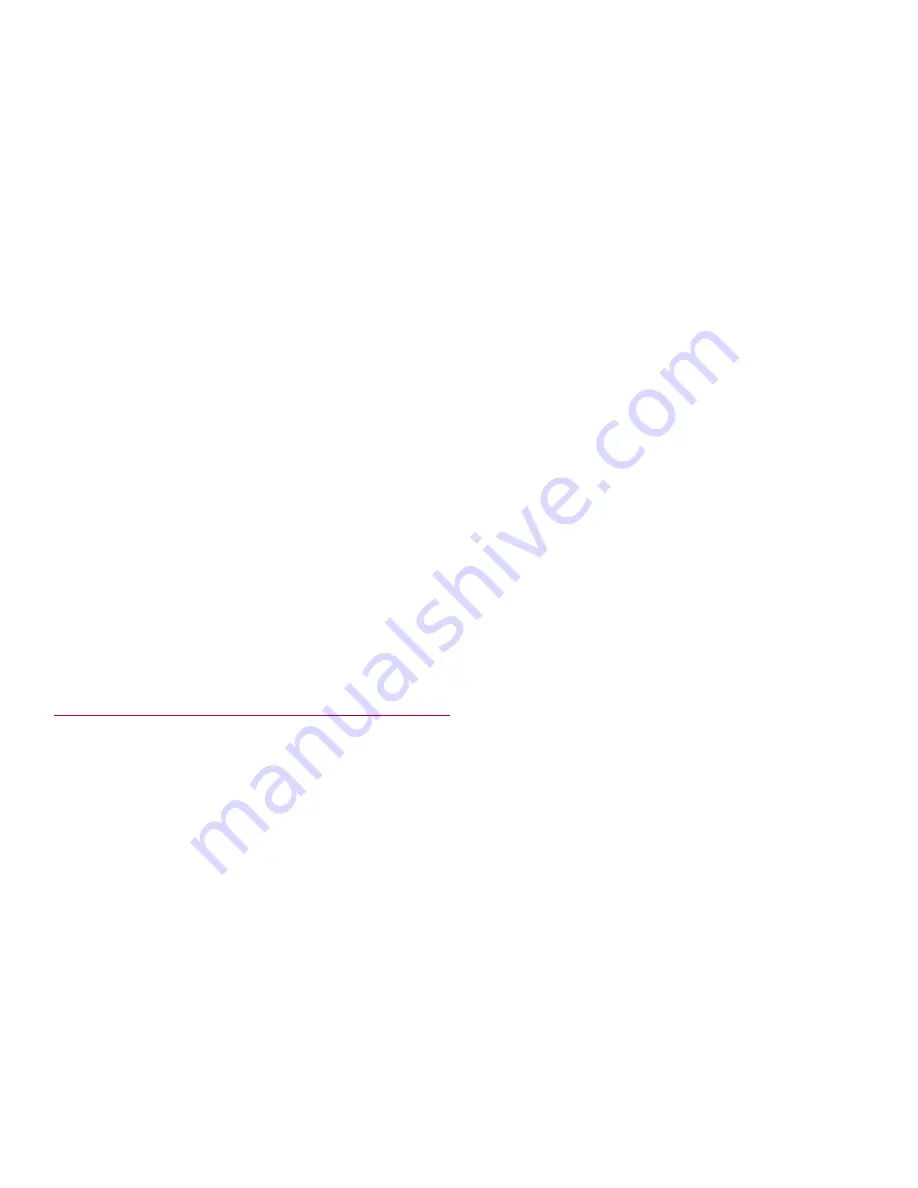
3
Limit Switches
– These switches are located on the
platform behind the water chamber.
Adjustment of these switches is made by loosening the
Phillips-head screws and moving the limit switch as-
sembly in the direction desired. The home position has
been set so that the load crossarm is in the middle of
the shear rings.
Note: The limit of travel of the drive shaft is dependent
on the limit switch settings. Do not operate the drive
motor with the water chamber disconnected because
this will make the limit switches inoperable.
Stop Switch
– Momentary push button to stop the
motor.
Direction Switch
– Momentary (spring loaded) switch.
After setting the desired shear rate, moving the switch
in the desired direction will initiate movement. This
switch will then become inactive until the stop button is
pressed, or a limit switch is activated. The left position
will move the water chamber to the left. It will continue
until the water chamber activates the limit switch. At
this time, the limit indicator light will be lit. The right
switch position will move the shear box to the right until
the home limit switch is made. See above note…
Home & Limit Indicators
– Used to indicate the limit
of travel of the shear box.
Fuse
– 4 amp SLO BLO fuse located in the cabinet
rear.
OPERATING INSTRUCTIONS
Read all operating instructions before performing a test
and refer to ASTM D3080 or AASHTO T 236 for com-
plete test procedures and calculations.
Set Up
1. Place the shear box into the water chamber and se-
cure the load cell shaft to the top of the shear box.
2. Tighten the two shear ring clamping knobs located
on the left side of the water chamber.
3. Install the counterbalance, Model 2000-75, if nec-
essary.
4. Tare the load cell by pressing the “Tare” button on
the digital readout.
5. Adjust the top cross arm and dial gauge so there is
1/8in gap between the cross arm and loading ball.
Align the cross arm pin so it is above the loading
ball. Make sure the cross arm is level.
6. Adjust the LVDT by raising or lowering the indicator
rod and holder so the tip of the LVDT is resting on
the cross arm pin.
Consolidation
1. Select a seating load with the load setting calibration
chart. Set the HIGH LOAD or LOW LOAD knob to
LOW and the Load Valve to “LOAD.”
2. Adjust the Fairchild Pressure Regulator to the de-
sired seating load per the load setting calibration
chart, this value is displayed on the digital readout
box, channel 4.
3. Turn the “LOAD” knob to “OFF” and adjust the Pres-
sure Regulator to the desired normal load based
on the load calibration chart. If reading from the
“LOW” calibration chart keep the knob on the LOW
LOAD position. If reading from the “HIGH” calibra-
tion chart, turn the knob to “HIGH LOAD”
4. Tare the LVDT on channel 3 before beginning con-
solidation.
5. Turn the Load Valve to “LOAD” to begin consolida-
tion.
6. Load and swell readings will be displayed on chan-
nels 3 and 4 of the readout box and transferred to
an Excel file or the Direct Shear Data Acquisition
Software on the users connected computer.
Direct Shear
1. After consolidation phase is complete, add a small
seating shear load by adjusting the two knurled nuts
on the load cell support.
2. Tare the shear load cell which is displayed on chan-
nel 1 of the digital readout box.
3. Remove the two holding screws on the shear box
to separate the top and bottom sections. Adjust the
four adjusting screws on the shear box to set the
gap between the top and bottom of the shear box.
One full turn of these adjusting screws will give a
0.031in (0.78mm) gap.
4. Set the shear/strain rate with the thumbwheels on
the left side of the machine. Each number is set by
pushing the thumbwheel button, the rate is in inches
per minute (0001 = 0.0001 in/min).
5. Tare the horizontal displacement LVDT on channel
2 of the readout box. To begin shear, switch the DI-
RECTION toggle switch to the left towards the LIMIT
light.