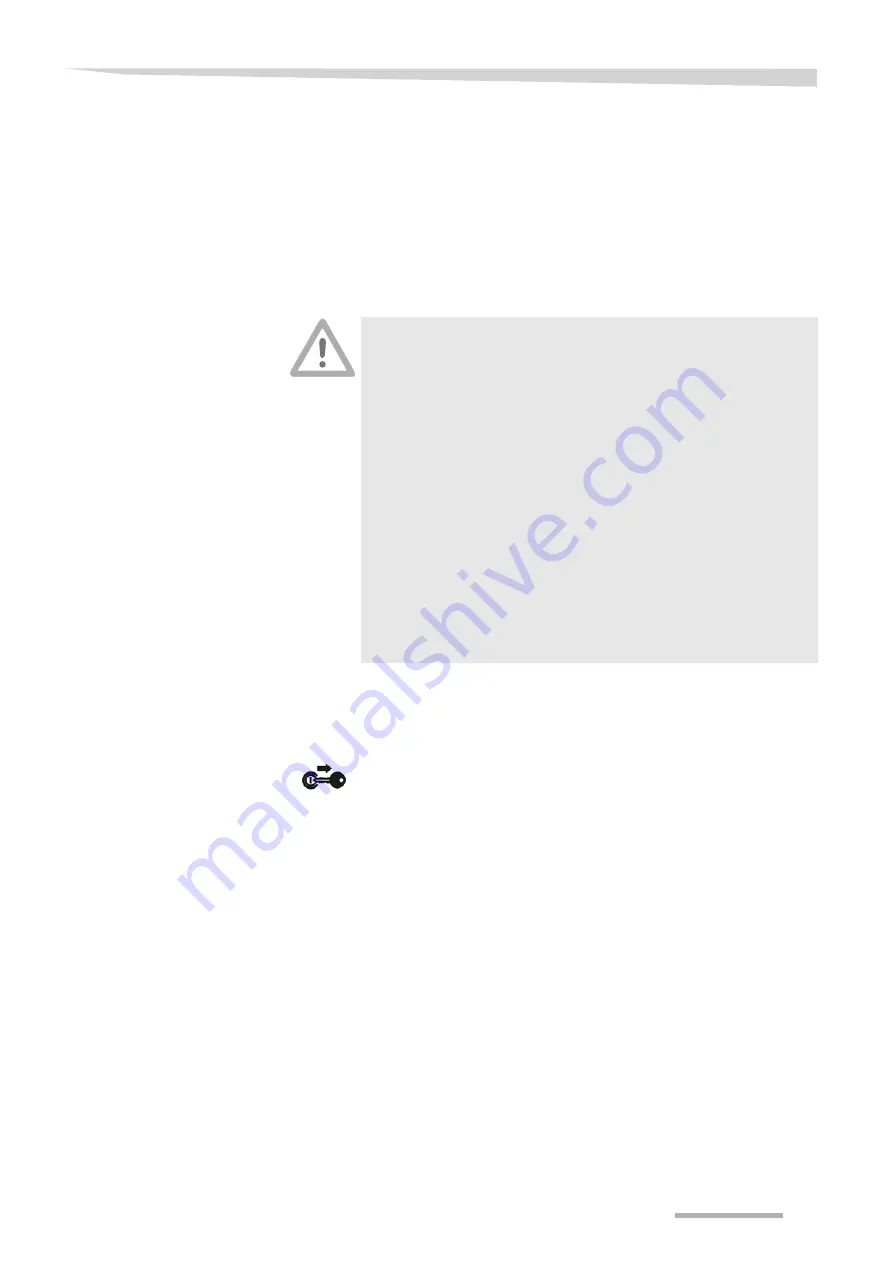
Setting up work
55
Setting up work
PTO shaft length
The length of the PTO shaft was selected at the factory to suit almost
all types of tractor. Only in exceptional cases is a correction of the PTO
shaft length required on individual tractors. Check the length of the
PTO shaft for each tractor prior to first use.
The operating manual from the PTO shaft manufacturer is included.
This includes detailed information on the relevant version of the PTO
shaft and must be observed.
Safety
Checking the PTO
shaft length
Couple the machine to the tractor without the PTO shaft.
Lower the tractor's lower link.
Set the tractor and machine to the smallest angle of lock.
Secure the tractor against rolling away, shut off the engine and
remove the ignition key.
Switch off the tractor and secure it
Before you dismount:
Switch off the tractor.
Remove the ignition key.
Secure the tractor against rolling away.
An unsecured tractor can run you over or trap you. Serious or fatal
injury would be caused as a result.
Check the angle of lock
The tractor's PTO shaft has a wide hinge joint, allowing an angle
of lock of up to 80°. Make sure that the PTO shaft is not damaged
during sharp cornering. The machine may be damaged as a
result.
Correct length
A PTO shaft that is too long must not be used. Damage to the drive
bearings on the tractor and machine will be caused as a result.
Содержание Vicon Andex 724
Страница 31: ...Crate packaging 31 Standard version with hydraulic transport chassis ...
Страница 72: ...Final operations 72 ...