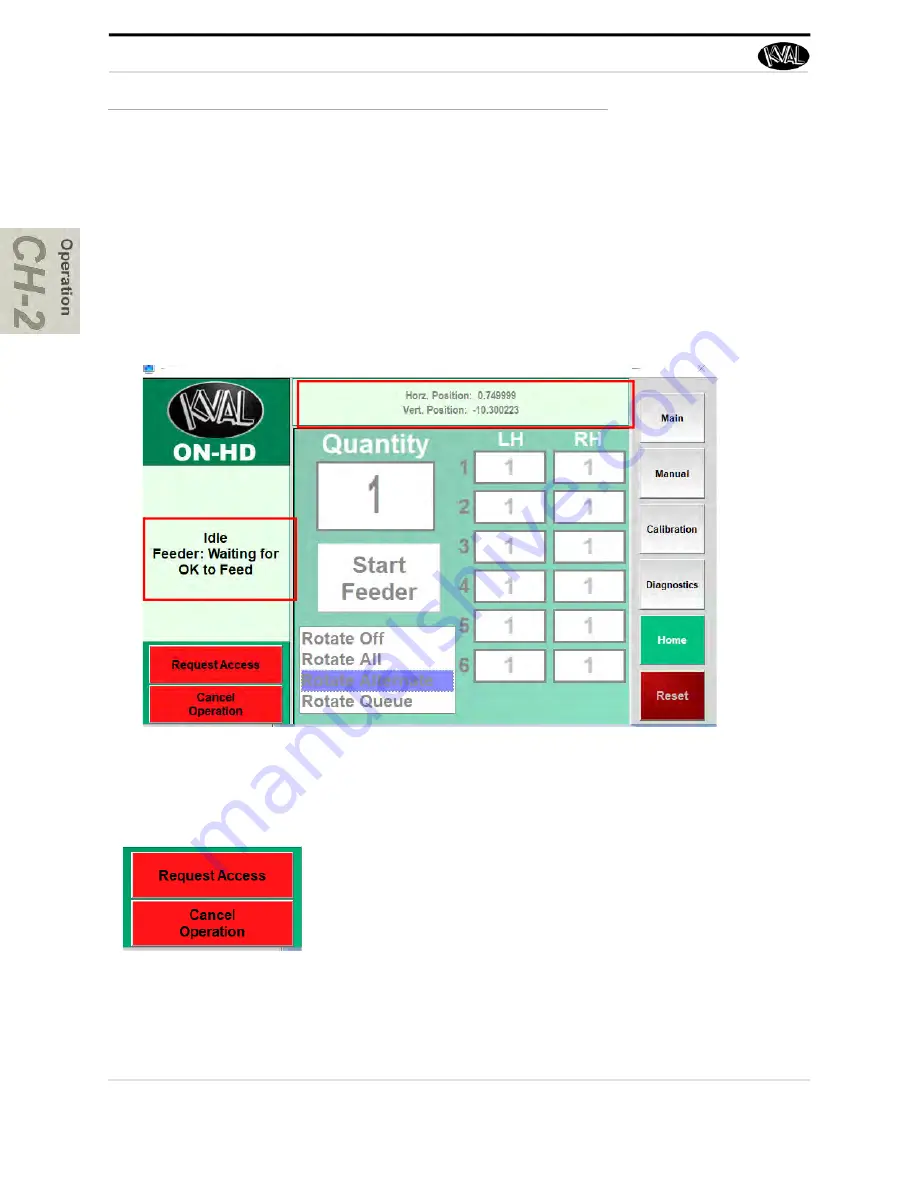
Universal Controls
KVAL ON-HD Operation Manual
2-10
Universal Controls
These controls are located on every screen
About Machine Status Feedback
At the right-hand side of the screen, feedback from the machine is displayed. The top window dis
-
plays servo locations. The machines are constantly polled, feeding back their state of operation.
This feedback is a great tool to instantly view the status of each machine.This information can be
used to troubleshoot any issues that may occur.
Request Access and Cancel Operation
Machine Feedback
Machine Feedback
Request Access: P
ress to request access to the machine.
This software button simulates the same action as pushing the
request access button at the Feeder entrance.
Cancel Operation
I Press to stop the operation of a door
being lifted. If pushed during the lift sequence, the gantry will
move the door back to the stack. If pushed before the door is
picked up, the gantry will go into the park position N
ote
: This
operation must be utilized before the door is placed on the
table.
Содержание ON-HD
Страница 4: ...KVAL ON HD Operation Manual ...
Страница 8: ...KVAL ON HD Lift Manual Table of Contents ...
Страница 13: ...Safety First KVAL ON HD Operation Manual 1 5 ...
Страница 28: ...How to Download the Service Application KVAL ON HD Operation Manual 1 20 Page Intentionally Left Blank ...
Страница 30: ...Safety Sign Off Sheet KVAL ON HD Operation Manual 1 22 ...
Страница 54: ...About the Safety Curtain KVAL ON HD Operation Manual 2 24 ...
Страница 70: ...Index Kval ON HD ...
Страница 71: ......