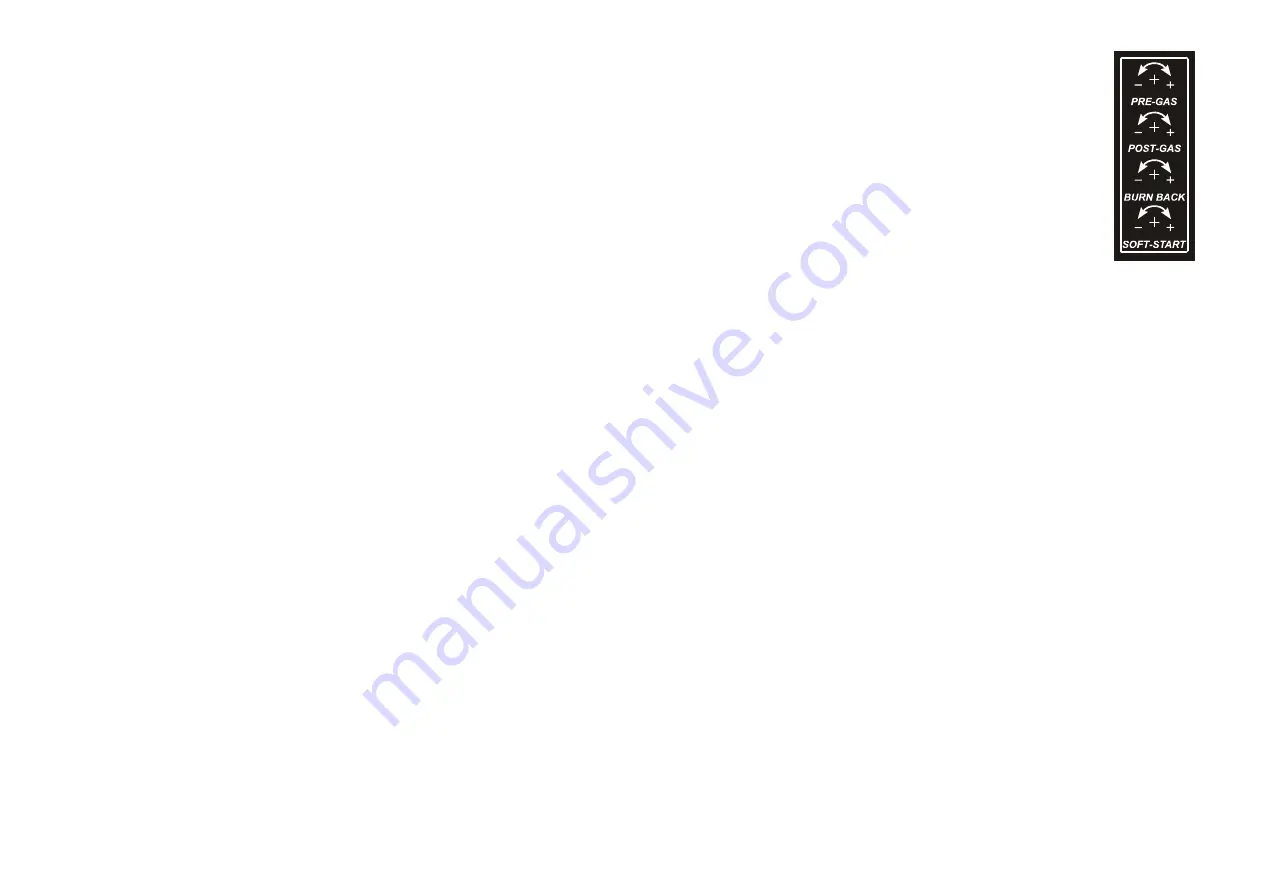
-18 -
English
Contents
Introduction
Description
Technical data
Usage limits
Safety standards
Installation
Equipment of KIT 169 machines
Connection to the electrical power sup-
ply
Control apparatus
Recommended adjustment of welding
parameters Processor and Synergic
Connection of the welding burner
Connection of the welding cable and
adjustment of the gas flow
Adjustment of welding standards
Welding work cycles
Prior to welding
Maintenance
The pointing out of any difficulties and
their elimination
Procedure for welder assembly and
disassembly
Ordering spare parts
Key to graphic symbols
Graphic symbols on the production plate
Electrical diagram
List of spare parts
Spare parts of wire feeder and list of
pulleys
Introduction
Thank you for purchasing one for our
products. Before using the equipment
you should carefully read the instructions
included in this manual. In order to get
the best performance from the system
and ensure that its parts last as long as
possible, you must strictly follow the
usage instructions and the maintenance
regulations included in this manual. In
the interest of customers, you are rec-
ommended to have maintenance and,
where necessary, repairs carried out by
the workshops of our service organisa-
tion, since they have suitable equipment
and specially trained personnel available.
All our machinery and systems are sub-
ject to continual development. We must
therefore reserve the right to modify their
construction and properties.
Description
KIT 2 and 3 are removable feeding ma-
chines specified for machines to the
welding of methodsfor MIG (Metal Inert
Gas) and MAG (Metal Active Gas)
welding. That is they are sources of
welding current with flat characteristics.
It concerns welding in protection atmos-
phere of active and intact gases when
added material is in a form of „infi-
nite“ wire supplied into the weld by the
wire feeding. These methods are very
productive, especially for the welds of
construction steel, low steel, aluminium
and its alloys. The source of welding
current, wire supply and feed are in one
compact metal case with two fixed and
two turning wheels. The removable
feeding machine KIT 3 has built in water
cooling of welding burner in addition.
The water cooling is built as closed water
circle equipped pump, cooler, reservoir
and air-pressure switch. The entry and
the exit of cooling liquid is equipped
gladhands.
-31 -
after finishing the welding, it is neces-
sary to adjust suitably the time of pre-
blow or afterblow of gas. Regulation is
carried out by potentiometers on front
panel of the machine next EURO con-
nector (picture 4). The lenght of the
preblow and afterblow is adjusted in the
interval 0-5 seconds.
ADJUSTMENT OF BURN BACK
TIME
The time of final wire burning prevents
thanks to the right adjustment of sticking
welding wire to the melt or contact tip.
The lenght of combustion can be ad-
justed in the interval of 0-1 second. The
adjustment of this function influences the
size of the „ball“ at the end of welding
wire and so the quality of further light-
ing-up the arc. It is required to adjust
parameters of combustion so that the ball
at the end of wire was as small as possi-
ble. Parameters differ according to dif-
ferent welding materials.
ADJUSTMENT OF SOFT START
This function enables when suitably
adjusted lighting-up of the arch without
any problems and no unnecessary spatter
and „movement“ of the welding torch.
Welding wire is after pressing the button
of the welding torch shifted at a small
approaching speed adjusted by potenti-
ometer SOFT START (picture 4). At the
time of the contact of welding wire and
material, arc is lighted-up and there is an
automatic switch-ing to the shift value
adjusted with the potentiometer on panel
inside of the wire feeder (picture 1, posi-
tion 5) – so called SOFT START.
Picture 4
Prior to welding
IMPORTANT:
before switching on the
welder, check once again that the voltage
and frequency of the power network
correspond to the rating plate.
1.
Adjust the welding voltage using the
switch (pos. 2,4 pict. 1) and welding
current/wire speed using the panel
potentiometer (pos. 5 pict. 1).
2.
Adjust the PROCESS switch (pos.6
and 7 pict. 1) to the most suitable po-
sition according to the type of weld-
ing to be carried out.
3.
Turn on the welder by selecting pos.
1 on the supply switch (pos. 1 pict.
1).
Maintenance
Warning: Before carrying out any
inspection of the inside of the genera-
tor, disconnect the system from the
supply.
SPARE PARTS
Original spare parts have been specially
designed for our equipment. The use of
non-original spare parts may cause varia-
tions in performance or reduce the fore-
seen level of safety. We decline all re-
sponsibility for the use of non-original
spare parts. As these systems are com-
pletely static, proceed as follows:
•
Periodic removal of accumulated dirt
and dust from the inside of the gen-
erator, using compressed air. Do not