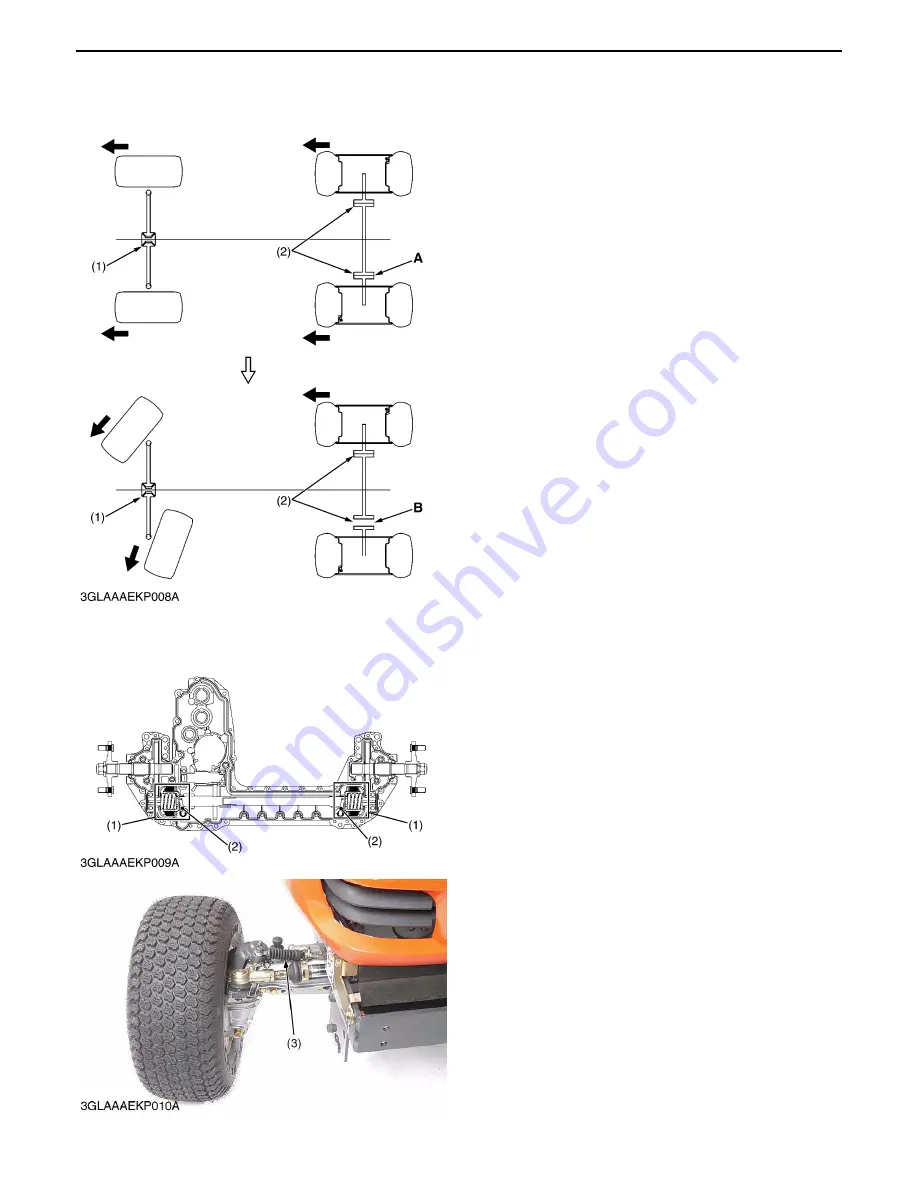
GR2100EC, WSM
TRANSAXLE
2-M9
[2] GLIDE STEER SECTION
(1) General
This machine is equipped with the Glide Steer
system.
On turning, the Glide Steer system provides a
mechanism that allows a turf-friendly minimum turn by
driving the front wheels and the rear wheel on the
outside of the turn at the same time.
This machine has left and right steering clutches (1)
in the rear transaxle.
The clutch lever (2) is connected to the king pin
support on the front axle with the wire (3). When turning
left or right, the wire connecting to the king pin support
on the front axle disengages only the steering clutch of
the turn side. This shuts off driving power to the rear
wheel on the inside of the turn.
On the other hand, the rear wheel on the outside of
the turn has driving power.
(1)
Differential Gear (Front)
A :
Engage
(2)
Steering Clutch
B :
Disengage
0000010102E
(1)
Steering Clutch
(3)
Wire
(2)
Clutch Lever
0000010103E
KiSC issued 04, 2006 A
Содержание WSM GR2100EC
Страница 1: ...GR2100EC WORKSHOP MANUAL KiSC issued 04 2006 A ...
Страница 7: ...GR2100EC WSM SAFETY INSTRUCTIONS 5 0000009633E KiSC issued 04 2006 A ...
Страница 8: ...GR2100EC WSM SAFETY INSTRUCTIONS 6 0000009634E KiSC issued 04 2006 A ...
Страница 11: ...GR2100EC WSM DIMENSIONS 9 DIMENSIONS 0000009634E KiSC issued 04 2006 A ...
Страница 12: ...G GENERAL KiSC issued 04 2006 A ...
Страница 65: ...1 ENGINE KiSC issued 04 2006 A ...
Страница 129: ...2 TRANSAXLE KiSC issued 04 2006 A ...
Страница 179: ...3 BRAKES KiSC issued 04 2006 A ...
Страница 189: ...4 FRONT AXLE KiSC issued 04 2006 A ...
Страница 190: ...CONTENTS 1 STRUCTURE 4 M1 KiSC issued 04 2006 A ...
Страница 208: ...5 STEERING KiSC issued 04 2006 A ...
Страница 209: ...CONTENTS 1 HYDRAULIC CIRCUIT 5 M1 2 STEERING CONTROLLER 5 M2 3 STEERING CYLINDER 5 M4 KiSC issued 04 2006 A ...
Страница 226: ...6 HYDRAULIC SYSTEM KiSC issued 04 2006 A ...
Страница 251: ...7 ELECTRICAL SYSTEM KiSC issued 04 2006 A ...
Страница 253: ...GR2100EC WSM ELECTRICAL SYSTEM 7 M1 1 WIRING DIAGRAM 0000009632E KiSC issued 04 2006 A ...
Страница 281: ...8 MOWER KiSC issued 04 2006 A ...
Страница 282: ...CONTENTS 1 POWER TRANSMISSION 8 M1 2 LIFTING MECHANISM 8 M2 KiSC issued 04 2006 A ...