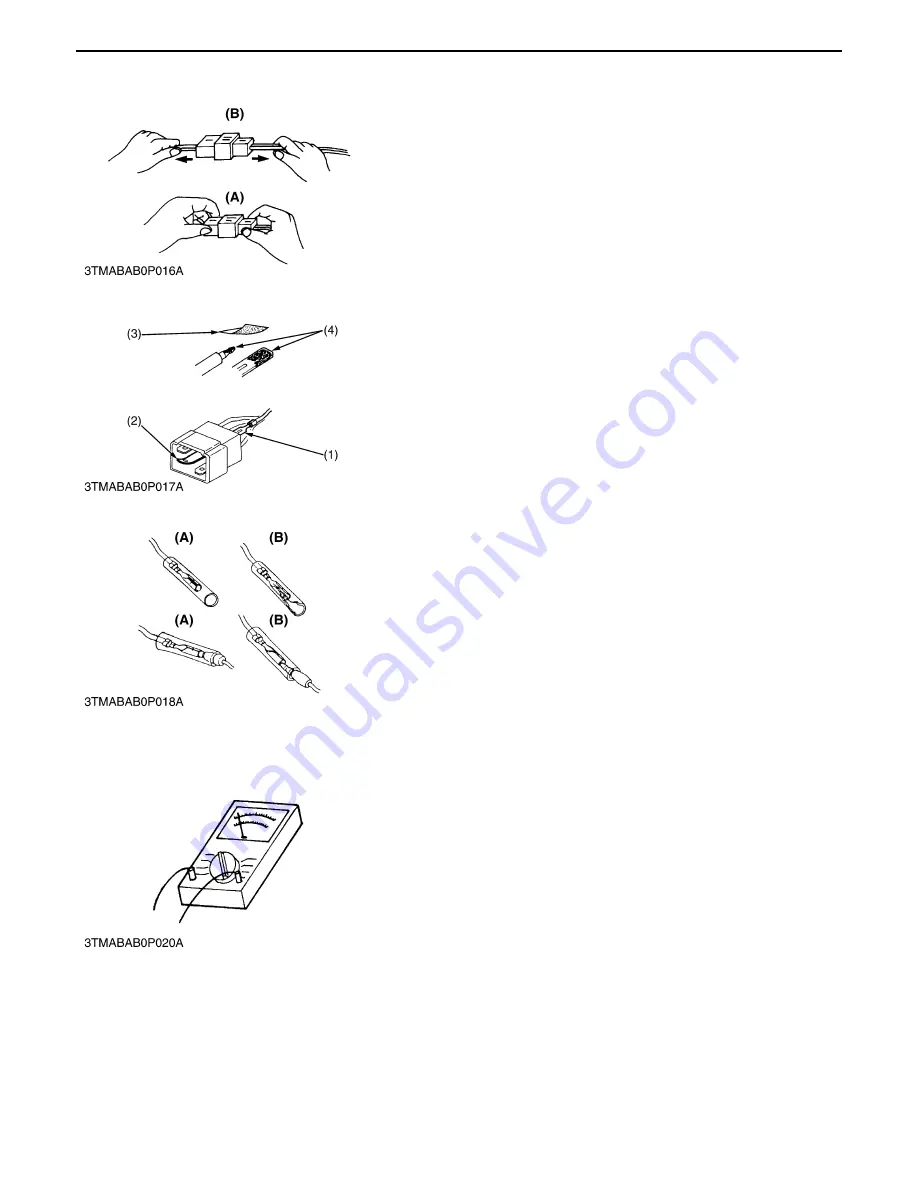
GZD15, WSM
GENERAL
G-6
A
In separating connectors, do not pull wire harnesses.
A
Hold connector bodies to separate.
A
Use sandpaper to remove rust from terminals.
A
Repair deformed terminal. Make certain there is no terminal
being exposed or displaced.
A
Make certain that there is no female connector being too open.
[5] HANDLING OF CIRCUIT TESTER
A
Use tester correctly following manual provided with tester.
A
Check for polarity and range.
(A)
Correct
(B)
Incorrect
0000000624E
(1)
Exposed Terminal
(3)
Sandpaper
(2)
Deformed Terminal
(4)
Rust
0000000625E
(A)
Correct
(B)
Incorrect
0000000626E
0000000628E
KiSC issued 04, 2006 A
Содержание GZD15
Страница 1: ...GZD15 WORKSHOP MANUAL KiSC issued 04 2006 A ...
Страница 7: ...GZD15 WSM SAFETY INSTRUCTIONS 5 KiSC issued 04 2006 A ...
Страница 8: ...GZD15 WSM SAFETY INSTRUCTIONS 6 KiSC issued 04 2006 A ...
Страница 9: ...GZD15 WSM SAFETY INSTRUCTIONS 7 0000001495E KiSC issued 04 2006 A ...
Страница 12: ...GZD15 WSM DIMENSIONS 10 DIMENSIONS KiSC issued 04 2006 A ...
Страница 13: ...GZD15 WSM DIMENSIONS 11 0000001694E KiSC issued 04 2006 A ...
Страница 14: ...G GENERAL KiSC issued 04 2006 A ...
Страница 72: ...1 ENGINE KiSC issued 04 2006 A ...
Страница 140: ...2 TRANSAXLE KiSC issued 04 2006 A ...
Страница 183: ...3 FRONT AXLE KiSC issued 04 2006 A ...
Страница 184: ...CONTENTS 1 STRUCTURE 3 M1 KiSC issued 04 2006 A ...
Страница 194: ...4 HYDRAULIC SYSTEM KiSC issued 04 2006 A ...
Страница 223: ...5 ELECTRICAL SYSTEM KiSC issued 04 2006 A ...
Страница 226: ...GZD15 WSM ELECTRICAL SYSYTEM 5 M2 0000001510E KiSC issued 04 2006 A ...
Страница 227: ...GZD15 WSM ELECTRICAL SYSYTEM 5 M3 0000001511E KiSC issued 04 2006 A ...
Страница 255: ...6 MOWER KiSC issued 04 2006 A ...
Страница 256: ...CONTENTS 1 POWER TRANSMISSION 6 M1 2 LIFTING MECHANISM 6 M2 KiSC issued 04 2006 A ...