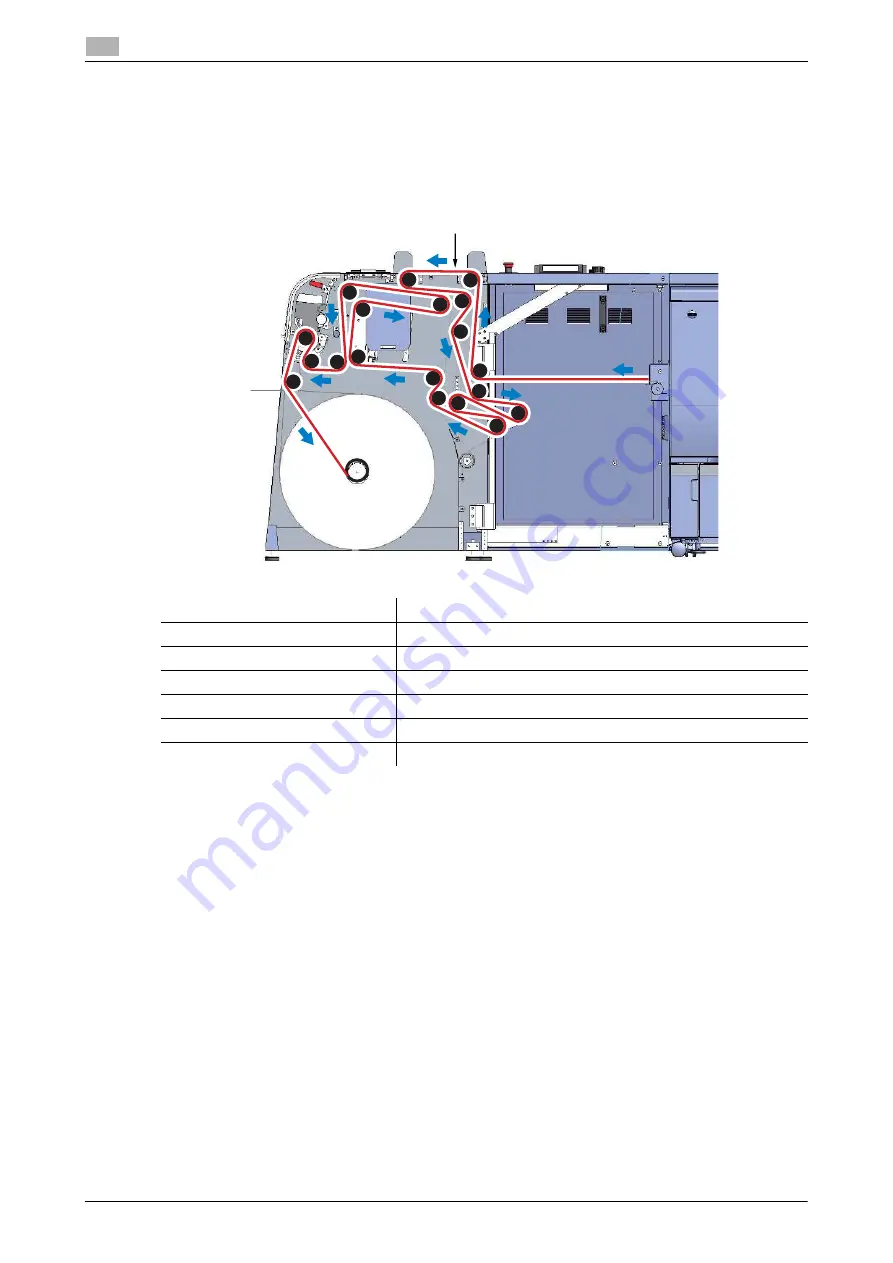
4-12
AccurioLabel 230
Setting media
4
4.2
4.2.4
Feed the media to Roll Winder RW-210
The following diagram shows the media route of
Roll Winder RW-210
. Feed the media along the correct
route.
NOTICE
Feed the media so that it passes through the center position of each roller.
Item
Description
Rollers (1) to (2)
Open the front door and feed the media.
Roller (3)
Feed the media from above the media inspection table.
Rollers (4) to (9)
Open the front door and feed the media.
Rollers (10) to (12)
Feed the media from the rewinder spindle side.
Rollers (13) to (15)
Open the safety cover of the upper side and feed the media.
Rollers (16) to (19)
Open the nip safety cover and feed the media.
1
2
3
14
4
5
6
7
9
8
10
11
12
13
15
16
17
18
19
Pass it above the media inspection table.
Содержание AccurioLabel 230
Страница 1: ...AccurioLabel 230 QUICK GUIDE...
Страница 2: ......
Страница 7: ...1 Introduction...
Страница 8: ......
Страница 12: ...1 6 AccurioLabel 230 Configuration and usage of this manual 1 1 5...
Страница 13: ...2 Before using this machine...
Страница 14: ......
Страница 35: ...3 Printing workflow...
Страница 36: ......
Страница 68: ...3 34 AccurioLabel 230 Operation after printing 3 3 3...
Страница 69: ...4 Handling paper...
Страница 70: ......
Страница 90: ...4 22 AccurioLabel 230 Setting media 4 4 2 6 Press Close The screen returns to the MACHINE screen...
Страница 125: ...5 Cleaning...
Страница 126: ......
Страница 151: ...6 Troubleshooting...
Страница 152: ......
Страница 179: ...7 Appendix...
Страница 180: ......
Страница 194: ...7 16 AccurioLabel 230 Typical specifications 7 7 2...