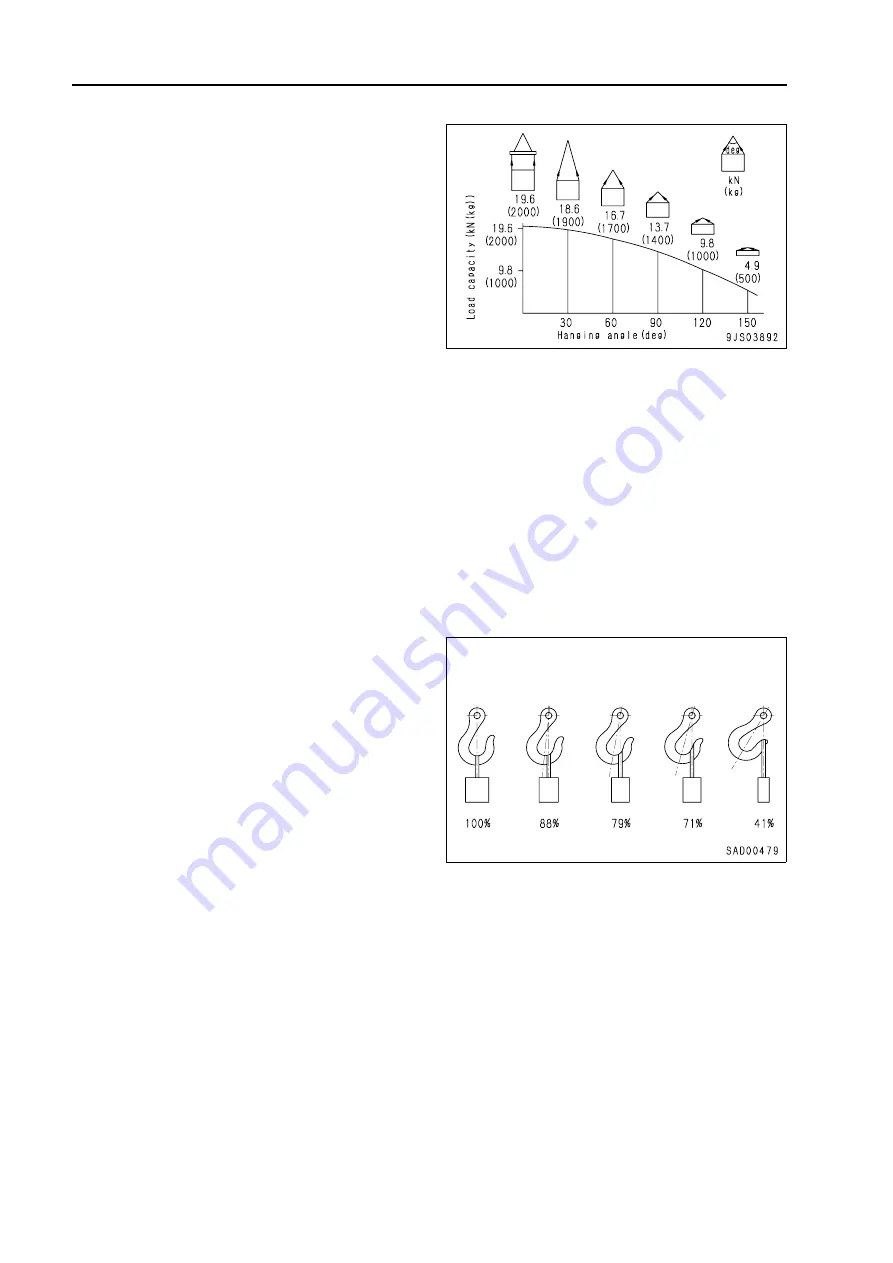
SEN00094-05
00 Index and foreword
4
PC200, 220-8
4.
Precautions for sling work and making
signs
1)
Only one appointed worker must make
signs and co-workers must communicate
with each other frequently. The appointed
sign maker must make specified signs
clearly at a place where he is well seen
from the operator's seat and where he can
see the working condition easily. The sign
maker must always stand in front of the
load and guide the operator safely.
q
Do not stand under the load.
q
Do not step on the load.
2)
Check the slings before starting sling
work.
3)
Keep putting on gloves during sling work.
(Put on leather gloves, if available.)
4)
Measure the weight of the load by the eye
and check its center of gravity.
5)
Use proper sling according to the weight
of the load and method of slinging. If too
thick wire ropes are used to sling a light
load, the load may slip and fall.
6)
Do not sling a load with 1 wire rope alone.
If it is slung so, it may rotate and may slip
out of the rope. Install 2 or more wire
ropes symmetrically.
k
Slinging with 1 rope may cause
turning of the load during hoisting,
untwisting of the rope, or slipping
of the rope from its original wind-
ing position on the load, which can
result in a dangerous accident.
7)
Limit the hanging angle to 60°, as a rule.
Do not sling a heavy load with ropes form-
ing a wide hanging angle from the hook.
When hoisting a load with 2 or more
ropes, the force subjected to each rope
will increase with the hanging angle. The
table below shows the variation of allow-
able load in kN {kg} when hoisting is made
with 2 ropes, each of which is allowed to
sling up to 9.8 kN {1,000 kg} vertically, at
various hanging angles. When the 2 ropes
sling a load vertically, up to 19.6 kN {2,000
kg} of total weight can be suspended.
This weight is reduced to 9.8 kN {1,000
kg} when the 2 ropes make a hanging
angle of 120°. If the 2 ropes sling a 19.6
kN {2,000 kg} load at a lifting angle of
150°, each of them is subjected to a force
as large as 39.2 kN {4,000 kg}.
8)
When installing wire ropes to an angular
load, apply pads to protect the wire ropes.
If the load is slippery, apply proper mate-
rial to prevent the wire rope from slipping.
9)
Use the specified eyebolts and fix wire
ropes, chains, etc. to them with shackles,
etc.
10) Apply wire ropes to the middle portion of
the hook.
q
Slinging near the tip of the hook may
cause the rope to slip off the hook
during hoisting. The hook has the
maximum strength at the middle por-
tion.
11) Do not use twisted or kinked wire ropes.
12) When lifting up a load, observe the follow-
ing.
q
Wind in the crane slowly until wire
ropes are stretched. When settling
the wire ropes with the hand, do not
grasp them but press them from
above. If you grasp them, your fingers
may be caught.
q
After the wire ropes are stretched,
stop the crane and check the condi-
tion of the slung load, wire ropes, and
pads.