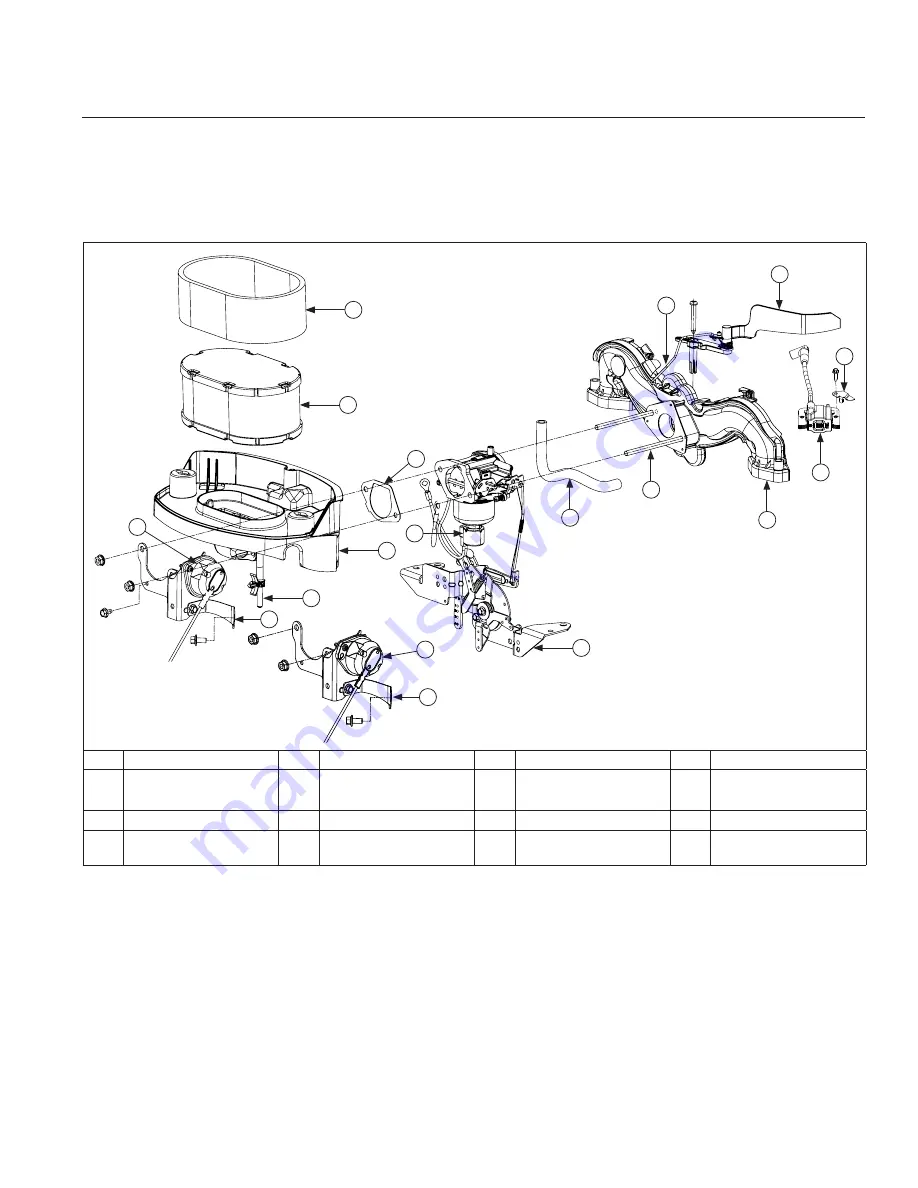
Fuel System
35
32 690 03 Rev. I
KohlerEngines.com
Smart-Choke
™
Components
A
B
C
D
E
F
H
I
J
K
L
N
M
P
G
O
E
F
A
Precleaner
B
Paper Element
C
Air Cleaner Base
D
Evap Hose
E
Smart-Choke
™
Bracket Assembly
F
Thermostat
G
Solenoid Lead
H
Air Cleaner Gasket
I
Control Assembly
J
Breather Hose
K
Stud
L
Intake Manifold
M
Choke Unloader
Linkage
N
Ignition Module
O
De
fl
ector Support Tab
P
Air Vane De
fl
ector
Smart-Choke
™
An air vane de
fl
ector assembly that operates by air from cooling fan opens choke partially when engine is running.
When engine is cold, a spring on air vane de
fl
ector assembly, in conjunction with a bimetallic spring, holds choke
closed for starting. A bimetallic spring reacts to heat generated by electrical resistance as engine is running and
opens choke plate position. When engine is warm, bimetallic spring holds choke completely open, while engine
is running. Choke will be 2/3 closed when warm and not running. These two elements work together to operate a
smooth choke system that facilitates easy reliable starting.