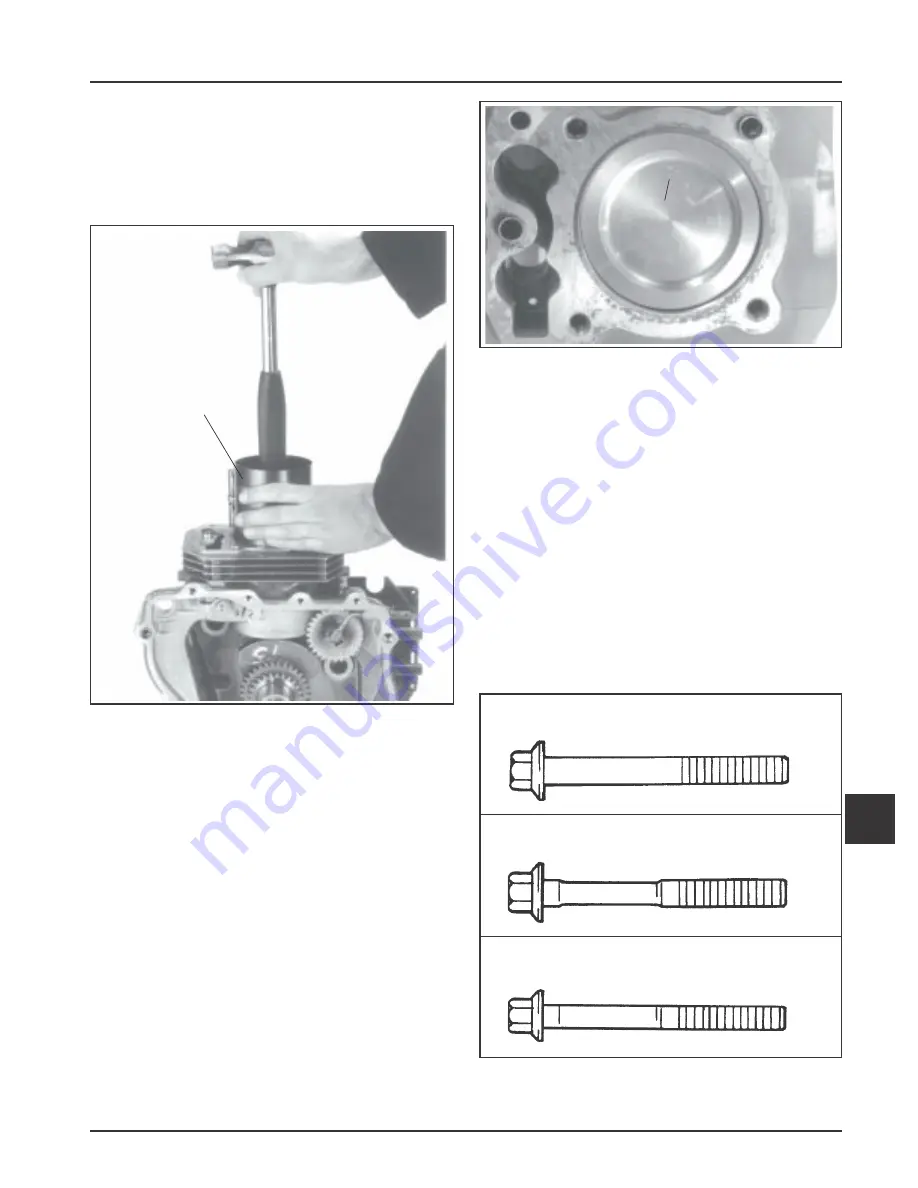
11.3
Section 11
Reassembly
11
Figure 11-6. Installing Piston and Connecting Rod.
3. Place the ring compressor on the top surface of
the crankcase and make certain it is seated down
around the entire circumference. The
FLY
arrow
on the piston should point toward the flywheel
side of the crankcase. See Figure 11-7. Use a soft,
rubber grip hammer handle and tap the piston/
connecting rod into the bore. The first tap should
be rather firm, so the oil ring moves from the
compressor into the bore in one smooth, quick
motion. Otherwise the oil ring rails may spring
out and jam between the ring compressor and
the top of the bore.
Figure 11-7. Piston Installation Identifier.
4. Lubricate the crankshaft journal and connecting
rod bearing surfaces with engine oil. Install the
rod cap to the connecting rod.
5. Three different types of connecting rod bolts have
been used in production, and each has a different
specific torque value. See Figures 11-8 and 11-9.
The 8 mm straight shank style rod bolts must be
torqued in increments to
22.7 N·m (200 in. lb.)
.
The 8 mm step-down shank style rod bolts must
be torqued in increments to
14.7 N·m
(130 in. lb.)
. The 6 mm straight shank style rod
bolts must be torqued in increments to
11.3 N·m
(100. in. lb.)
. Illustrated instructions are also
provide in the service rod package.
2. Lubricate the cylinder bore, piston, and rings
with engine oil. Compress the piston rings using
a piston ring compressor. See Figure 11-6. Push
the piston through the compressor so the oil
control (bottom) ring is just above the lower edge
of the compressor.
Piston Ring
Compressor Installed
Around Piston
Arrow Must
Point Towards
Flywheel
Torque these to 22.7 N·m (200 in. lb.)
8 mm Straight Shank
Torque these to 14.7 N·m (130 in. lb.)
8 mm Step-Down Shank
Torque these to 11.3 N·m (100 in. lb.)
6 mm Straight Shank
Figure 11-8. Connecting Rod Bolts.