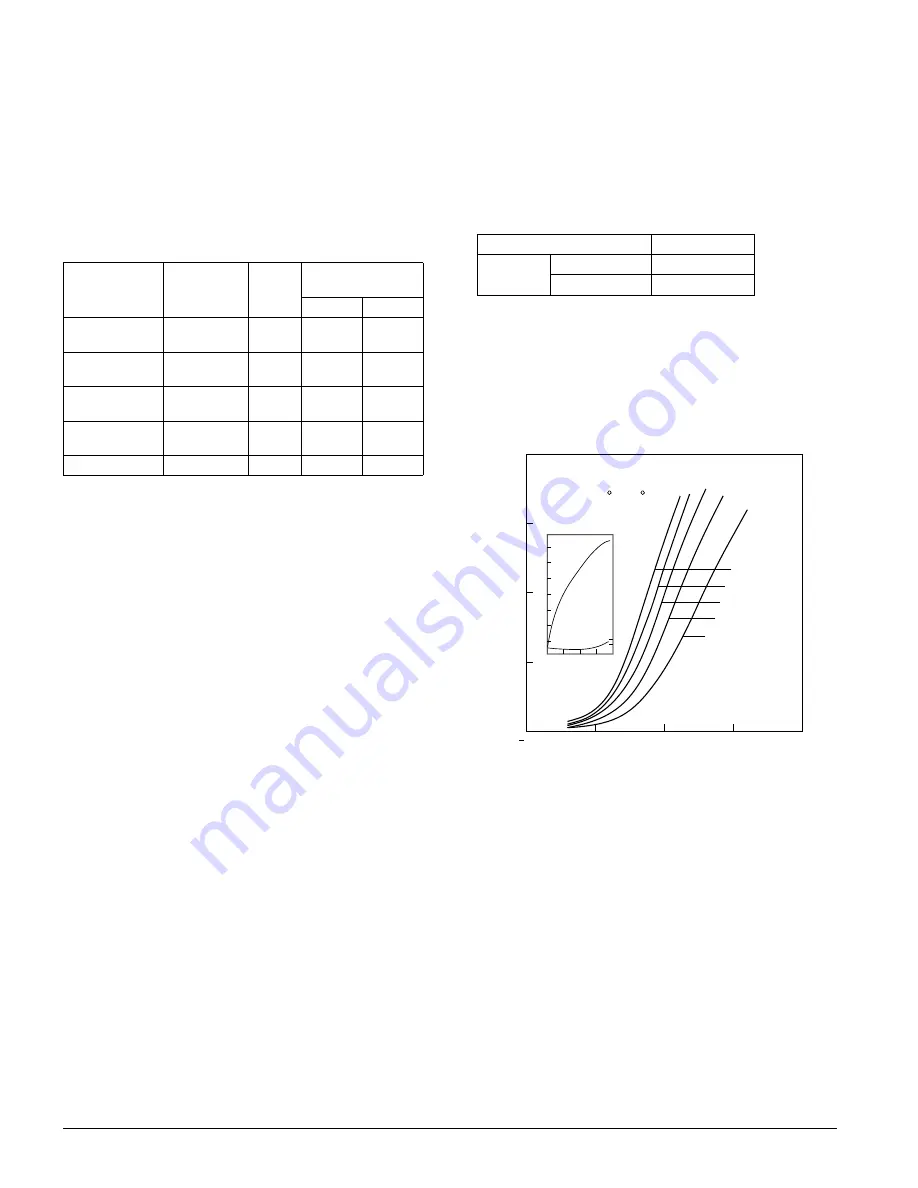
2
EASTMAN Fine Grain Release Positive Film 5302 / 7302
•
H-1-5302
PROCESSING
The following process recommendations should be used as
starting points for a typical continuous-immersion
processing machine using formulas presented in KODAK
Publication No.H-24,
Manual for Processing EASTMAN
Motion Picture Films
, Module 15. The processing times may
require modification for a particular machine.
Notice:
Observe precautionary information on product labels and on the
Material Safety Data Sheets.
*
Agitation in the developer and fixing bath should be by recirculation through
submerged spray jets that impinge on the film strands.
†
Develop to recommended control gamma of 2.4 to 2.6 (Status A).
‡
Countercurrent flow of fixer-laden water overflow from the wash tank, pH
about 6.
§
Many factors affect the drying: air temperature, relative humidity (RH);
volume, rate and distribution of the air flow; final squeegeeing, etc. In a
conventional convection-type drying cabinet with air at about 95
°
F (35
°
C)
and 40 to 50 percent RH, drying will take 15 to 20 minutes. With an
impingement-type drying cabinet, however, with a higher temperature and
lower RH, drying time is greatly reduced. With either type of dryer, the film
should be dry without tackiness 1/2 to 2/3 of the way through. Upon cooling
to room temperature after leaving the dryer, the film should be in equilibrium
with the room air at approximately 50 percent RH.
LUBRICATION
All films destined for projection require some lubrication to
prevent problems during early projection life. Edge waxing
with a paraffin wax solvent solution provides a simple,
inexpensive, and adequate lubrication for 35 and 70 mm
projection prints. For 8 and 16 mm prints, an overall
lubricant may be required.
Processing Step
Temperature
Time
Replenishment Rate
(mL per 100 ft)
35 mm
16 mm
KODAK
Developer D-97
*
70
±
1/2
°
F
(21
±
0.3
°
C)
†
650
(D-97R)
325
(D-97R)
Stop Rinse
‡
70
±
2 F
°
(21
±
1
°
C)
50 sec
12,000
6,000
KODAK Fixing
Bath F-5
*
70
±
2
°
F
(21
±
1
°
C)
9 min
600
300
Wash (counter-
current)
70
±
2
°
F
(21
±
1
°
C)
10 min
12,000
6,000
Dry
95
°
F (35
°
C)
§
—
—
IMAGE STRUCTURE
The modulation-transfer curves, the diffuse rms
granularity, and the resolving-power data were generated
from samples of 5302 Film exposed with tungsten light and
processed as recommended in KODAK Developer D-97 at
70 F (21 C) to the recommended control gamma. For more
information on image-structure characteristics, see
KODAK Publication No H-1, EASTMAN Professional
Motion Picture Films.
*
Read at a net diffuse visual density of 1.0, using a 48-micrometre aperture.
†
Determined according to a method similar to the one described in ISO
6328-1982, Photography — Photographic Materials — Determination of ISO
Resolving Power.
CURVES
Characteristic Curves
NOTICE:
The sensitometric curves and data in this
publication represent product tested under the conditions
of exposure and processing specified. They are
representative of production coatings, and therefore do
not apply directly to a particular box or roll of photographic
material. They do not represent standards or specifications
that must be met by Eastman Kodak Company. The
company reserves the right to change and improve
Diffuse rms Granularity
*
8
Resolving
Power
†
63 lines/mm
(TOC 1.6:1)
125 lines/mm
(TOC 1000:1)
2
4
6
8
10
DEVELOPMENT TIME
(Minutes)
2.8
2.6
2.4
2.2
2.0
0.00
0.10
GAMMA
NET
FOG
Time-
Gamma
Time-Fog
2 min.
3 1/2 min.
5 min.
7 min.
9 min.
Visual
F010_0023AC
D-97, at 21 C (70 F)
3.0
Characteristic Curves
Diffuse
Tungsten
KODAK Developer
Process:
Exposure:
Densitometry:
2.0
1.0
4.0
3.0
2.0
1.0
DENSITY
0.0
0.0
1.0
LOG EXPOSURE (lux-seconds)
3.0
3.2
3.4