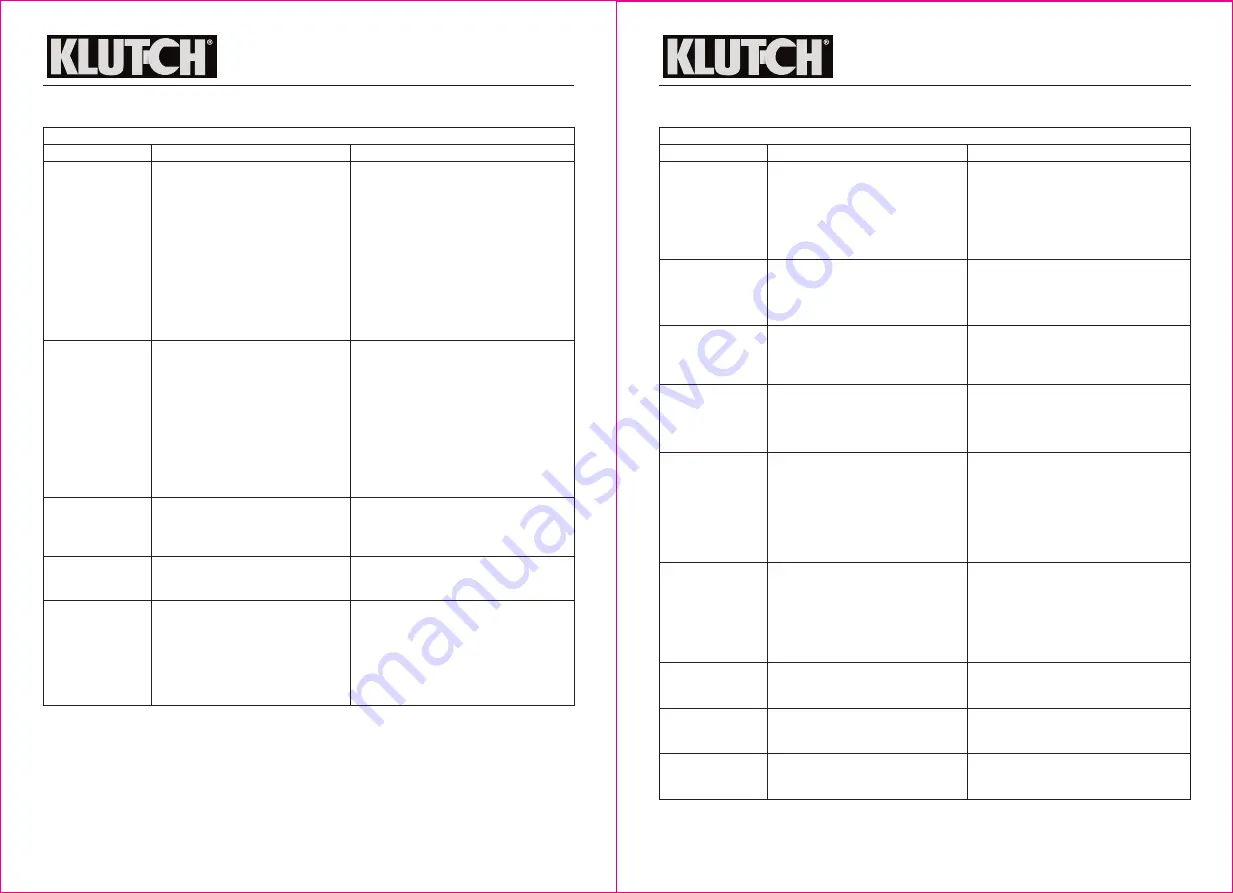
23 of 24
Troubleshooting
Machine does not
start or a breaker
trips.
Machine stalls or
is underpowered.
Loud, repetitious
noise coming from
machine near the
motor.
Motor overheats.
Motor is loud when
cutting. Overheats
or bogs down in
the cut.
1. Fuse has blown.
2. Emergency stop push-button is
engaged/ faulty.
3. Plug/receptacle is at fault or wired
incorrectly.
4. Computer board is at fault.
5. Power supply is at fault/switched OFF.
6. Motor on button or on /OFF switch
is at fault.
7. Spindle rotation switch is at fault.
8. Wiring is open/has high resistance.
9. Motor is at fault.
1. Wrong workpiece material (metal).
2. Computer board is at fault.
3. Motor speed rheostat is at fault.
4. Motor brushes are at fault.
5. Pulley/sprocket slipping on shaft.
6. Motor bearings are at fault.
7. Machine is undersized for the task.
8. Spindle rotation switch at fault.
1. Pulley setscrews or keys are
missing or loose.
2. Motor fan is hitting the cover.
1. Motor overloaded.
2. Air circulation through the motor
restricted.
1. Excessive depth of cut or feed rate.
2. RPM or feed rate wrong for cutting
operation.
3. Cutting tool is dull.
4. Gear setup is too tight, causing
them to bind.
Possible Solution
Symptom
Possible Cause
Motor & Electrical
1. Correct short/replace fuse on control panel.
2. Rotate clockwise slightly until it pops
out/replace it.
3. Test for good contacts; correct the wiring.
4. Inspect computer board; replace if faulty.
5. Ensure hot lines have correct voltage on
all legs and main power supply is
switched on.
6. Replace faulty on button or on /OFF switch.
7. Turn switch to FWD/REV; replace bad
switch.
8. Check for broken wires or disconnected/
corroded connections, and repair/replace
as necessary.
9. Test/repair/replace.
1. Use metal with correct properties for your
type ofmachining.
2. Inspect and replace if faulty.
3. Test and replace if faulty.
4. Remove brushes and clean/replace.
5. Replace loose pulley/shaft.
6. Test by rotating shaft; rotational grinding
/loose shaftrequires bearing replacement.
7. Use sharp lathe bits/chisels at correct
angle; reducefeed rate/depth of cut; use
cutting fluid if possible.
8. Turn switch to FWD/OFF/REV; replace
bad switch.
1. Inspect keys and setscrews. Replace or
tighten if necessary.
2. Tighten fan or shim cover, or replace
items.
1. Reduce load on motor.
2. Clean out motor to provide normal air
circulation.
1. Decrease depth of cut or feed rate.
2. Refer to RPM feed rate chart for
appropriate rates.
3. Sharpen or replace the cutting tool.
4. Readjust the gear setup with a small
amount ofbacklash so the gears move
freely and smoothlywhen the chuck is
rotated by hand.
Entire machine
vibrates
successively
upon start up and
while running.
Bad surface finish.
Can't remove
tapered tool from
tailstock quill.
Cross slide,
compound slide,
or carriage feed
has sloppy
operation.
Cross slide,
compound slide,
or carriage feed
handwheel is hard
to move.
Cutting tool or
machine
components
vibrate excessively
during cutting.
Inaccurate turning
results all along
the workpiece .
Chuck jaws won't
move or don't
move easily.
Carriage won't feed.
1.Workpiece is unbalanced.
2. Loose or damaged belt(s).
3. V-belt pulleys are not properly
aligned.
4. Worn or broken gear present.
5. Chuck or faceplate has become
unbalanced.
6. Spindle bearings badly worn.
1. Wrong rpm or feed rate.
2. Dull tooling or poor tool selection.
3. Too much play in the gibs.
4. Tool too high.
1. Quill had not retracted all the way
back into the tailstock.
2. Debris was not removed from
taperbefore inserting into quill.
1. Gibs are out of adjustment.
2. Handwheel is loose.
3. Lead screw mechanism worn or
out of adjustment.
1. Gibs are loaded up with shavings,
dust, or grime.
2. Gib screws are too tight.
3. Backlash setting too tight (cross
slide only).
4. Bedways are dry.
1. Tool holder not tight enough.
2. Cutting tool sticks too far out of
tool holder; lack of support.
3. Gibs are out of adjustment.
4. Dull cutting tool.
5. Incorrect spindle speed or feed rate.
1. Headstock and tailstock are not
properly aligned with each other.
1. Chips lodged in the jaws.
1. Gears are not all engaged.
2. Gears are broken.
3. Loose screw on the feed handle.
Possible Solution
Symptom
Possible Cause
Operation and Work Results
1. Reinstall workpiece so it is as centered with
the spindle bore as possible.
2. Tighten/replace the belt as necessary.
3.Align the V-belt pulleys.
4. Inspect gears and replace if necessary.
5. Rebalance chuck or faceplate; contact a
local machine shop for help.
6. Replace spindle bearings.
1. Adjust for appropriate RPM and feed rate.
2. Sharpen tooling or select a better tool for
the intended operation.
3. Tighten the gibs.
4. Lower the tool position.
1. Turn the quill handwheel until it forces
taper out of quill.
2. Always make sure that taper surfaces
are clean.
1. Adjust gib screw(s) (see Page 35).
2. Tighten handwheel fasteners.
3. Tighten any loose fasteners on lead screw
mechanism.
1. Remove gibs, clean ways/dovetails,
lubricate, and readjust gibs.
2. Loosen gib screw(s) slightly, and
lubricate bedways.
3. Slightly loosen backlash setting by
loosening the locking screw and
adjusting the spanner ring at the end
of the handle.
4. Lubricate bedways and handles.
1. Check for debris, clean, and retighten.
2. Reinstall cutting tool so no more than
1⁄3 of the total length is sticking out of
tool holder.
3. Tighten gib screws at affected
component.
4. Replace or re-sharpen cutting tool.
5. Use the recommended spindle speed.
1. Realign the tailstock to the headstock
spindle bore center line.
1. Remove jaws, clean and lubricate chuck
threads, and replace jaws.
1. Adjust gear positions.
2. Replace.
3. Tighten.
22 of 24
Mini Metal Lathe 7 x 12
OWNER’S MANUAL
Mini Metal Lathe 7 x 12
OWNER’S MANUAL