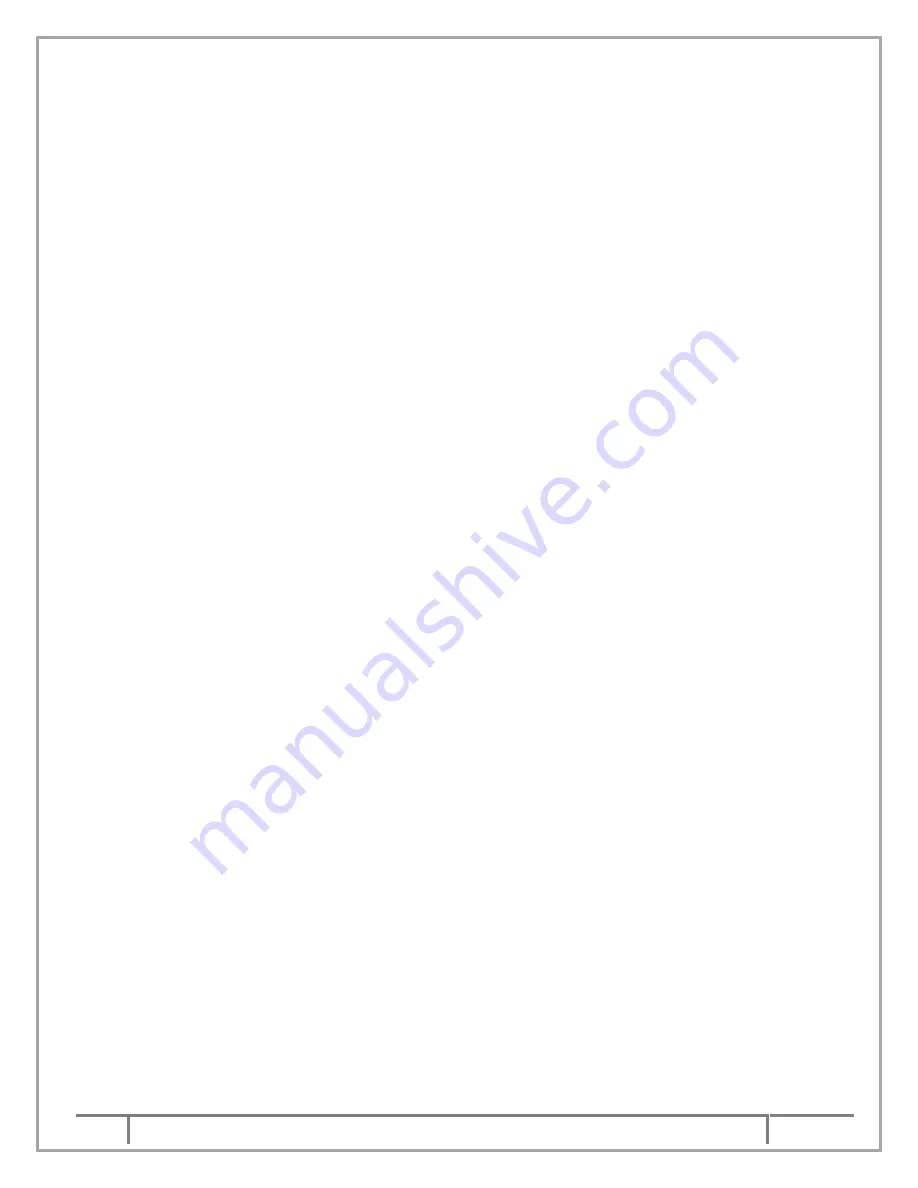
12
This is a proprietary document of Kirloskar Brothers Limited, YAMUNA’ Survey No. 98/ 3 to 7, Baner, Pune – 411045, India.
NS IOM MANUAL
1 Sept 2018
4.1.5
Hoist up the pump and momentarily switch on the power. If the connections are correctly made the
pump should jerk in anticlockwise direction when viewed from top. If the pump jerks in opposite
direction, change two phases of the incoming leads to the control panel. In no case the direction of
rotation should be changed by changing the leads of motor terminals. Do not run the pump dry.
Just check in which direction the pump jerks.
4.2
While putting the pump in operation, follow the procedure outlined below.
4.2.1 Start the pump. Let the motor pick-up its full speed.
4.2.2 Open the discharge valve slowly.
4.3
Check during running that –
4.3.1
The pump is running smooth.
4.3.2
Power consumption is within limit.
4.3.3
Head and capacity developed by the pump is as specified.
4.3.4
Stop the pump immediately if any defects are detected and must not be started unless they
are rectified. Report immediately to the supplier if it is not possible to rectify the defect.
4.4
STOPPING THE PUMP:
4.4.1
Pump should be switched off only after closing the delivery sluice valve.
5.
MAINTENANCE:
Preventive maintenance schedule is the periodical checks and precautions by which possibilities
of failure and break-downs are minimized.
5.1 Daily checks –
5.1.1
An hourly record of the delivery pressure and power input to the pump should be maintained.
5.1.2
Noise and vibrations is the first sign of impending troubles like bearing failure, choking of impeller
or casing and such other operating troubles. The pump performance should be checked for noise
and vibration.
5.2
Periodical checks –
5.2.1
The lubrication of mechanical seals should be checked. The lubricant might get contaminated with
foreign material or get blackened due to overheating. In such cases, oil chamber should be flushed
and filled with fresh oil. Before filling, heat the oil [Servo system 317] to 140
°
C. This is required to
remove moisture present in the oil.
5.2.2
THE ELECTRODES/FLOAT SWITCHES SHOULD BE CLEANED WHENEVER POSSIBLE BUT
NOT LATER THAN 15 DAYS FOR SMOOTH WORKING OF PUMP.
5.2.3
Clean the sump if there are chances of deposition of the contents of liquid handled.
5.2.4
Replace the Oil from pump periodically after 2000 hrs.
5.3
Annual checks [after one year minimum] –
5.3.1
The pump portion of the motor pump set should be overhauled completely to check the clearance
and to replace the worn-out parts. Clearance between impeller and casing ring and casing cover
are very important.
5.3.2
The effect of liquid handled on pump components should be checked. If abnormal corrosion,
erosion is observed then the components should be replaced with that of suitable material.