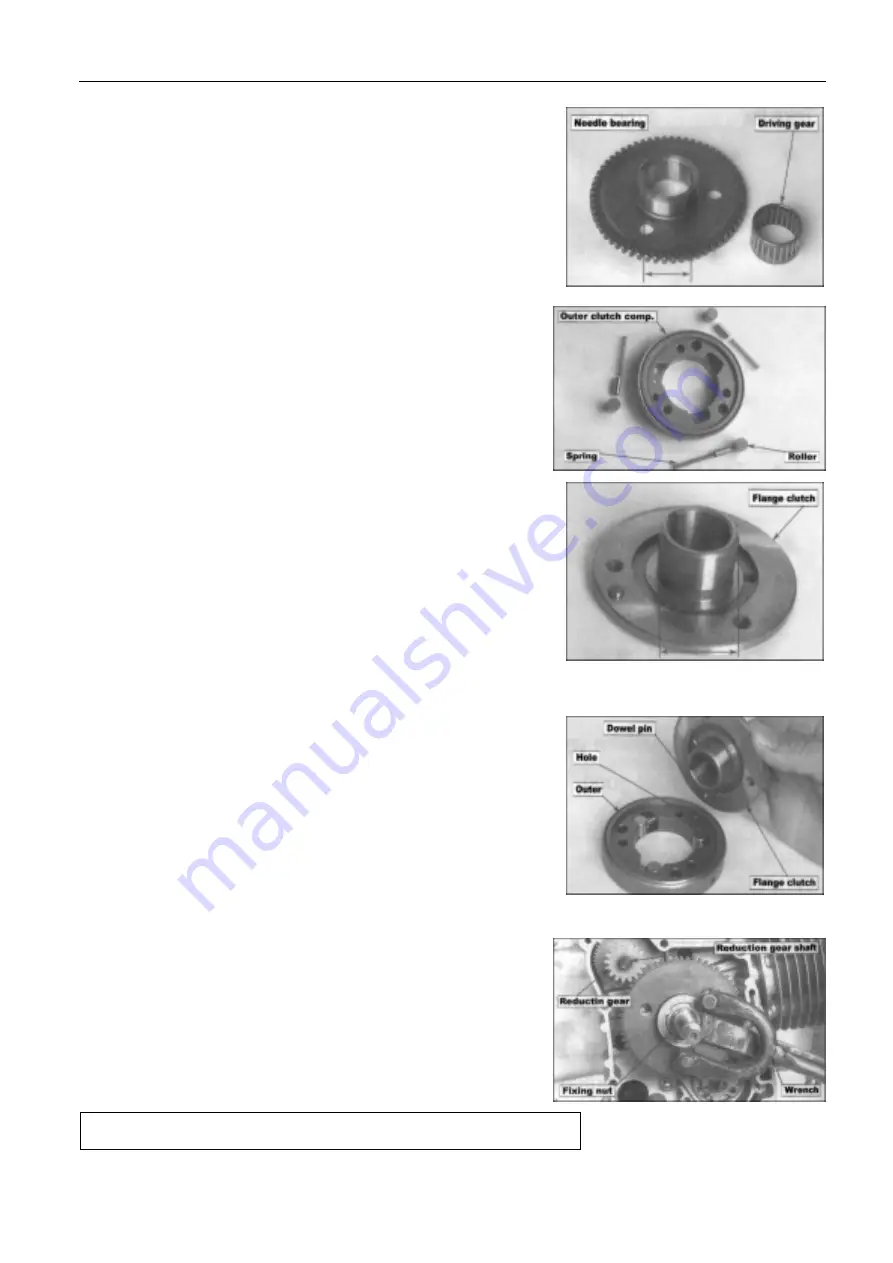
KINROAD 150 SERVICE MANUAL VERSION 1, DEC., 2005
45
Inspect if there is any abrasion or damage on the contact surface
between the driving gear and the needle bearing. It should be
replaced if the surface is damaged.
Measure the inner diameter of the driving gear. It should be replaced
when the diameter is more than 32.06mm.
Inspect the condition of the needle bearing. It should be replaced if
there is any damage.
Inspect if there is any abrasion or damage on the contact surface
between the outer clutch component and the roller.
Inspect if there is any injury on the roller.
Inspect if there is any distortion of the spring.
If the damage is serious, it should be replaced.
Measure the inner diameter of the flange clutch. It should be
replaced when the diameter is more than 27.94mm.
STARTING CLUTCH INSTALLATION
Install the spring, the roller and the top pin on the body of the clutch.
Align the dowel pin on the flange clutch with the hole on the clutch
body, then install.
Apply some thread lock on the outer clutch component bolt and
tighten.
Apply some oil on the needle bearing and the driving gear, and then
put the outer clutch component on.
Align the groove of the woodruff key on the crank, and install the
starting clutch.
Apply some oil on the reduction gear and the reduction gear shaft,
then install.
Hold the drive face with the universal wrench. At the same time
fasten the clutch nut.
z
Notice that the thread of the nut should be left-handed rotation.