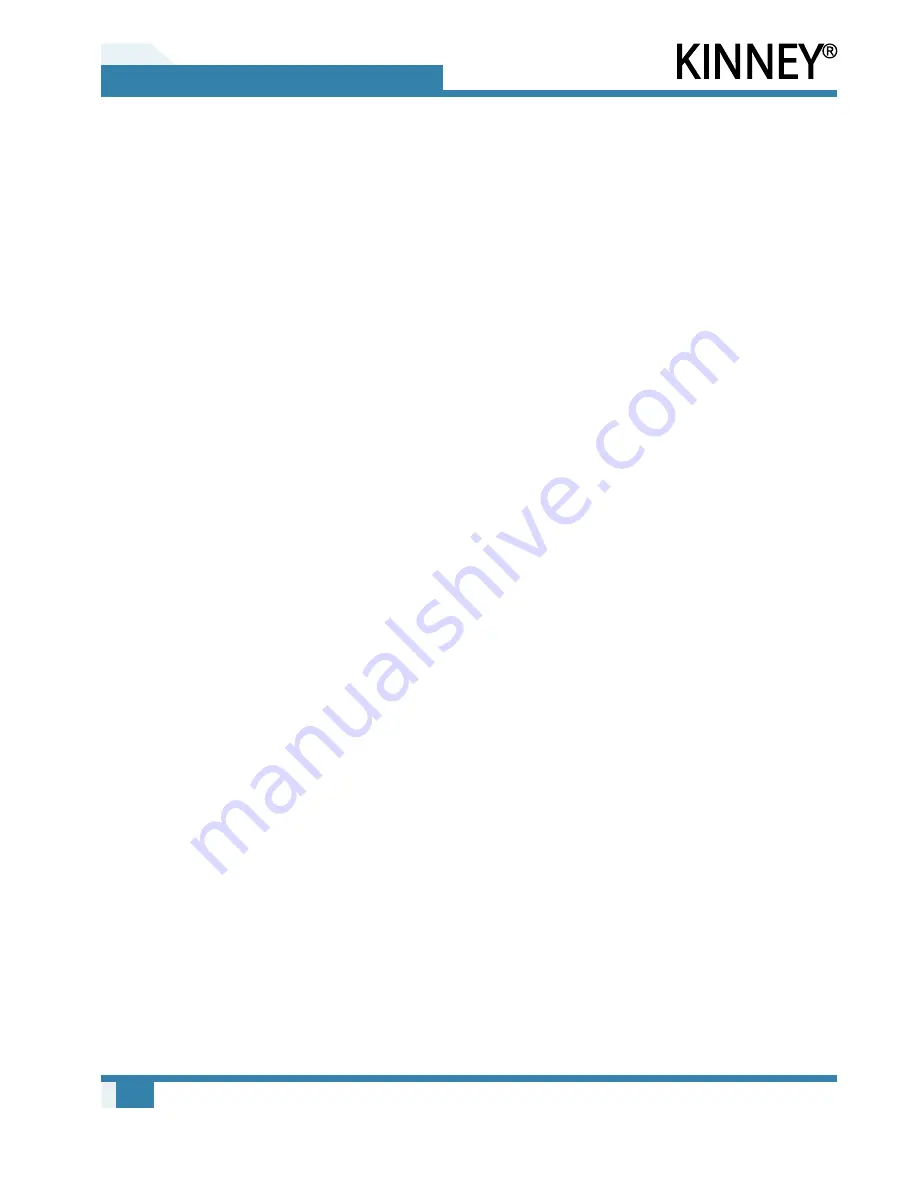
16
04
Operation
Manual 4804 Rev E p/n 004804 0000
5.
A liquid level gauge is installed to allow visual
monitoring of the sealant level. NOTE: The
limitations on what sealant can be used in the
liquid ring pump are based on the following
considerations:
a. The sealant should be compatible with the
materials of construction and the process
stream so that corrosion, polymerization,
or some adverse chemical reaction does
not occur.
b. The vapor pressure of the sealant must
be compatible with the desired process
pressure.
c.
Specific gravity should be between 0.5
and 2.
d.
Specific heat should be between 0.3 and 1.
e. Viscosity should be <45 cSt at sealant
operating temperature.
6.
After filling the liquid ring pump and recovery
system with sealant to the proper level,
position the manual valves for start-up.
a. Check the globe valve located in the
sealant line between the heat exchanger
and the liquid sealant.
b. Check that the two small valves located
in the seal cooling lines leading to the
mechanical seals on the liquid ring pump
are both fully opened. These valves may
be throttled down to halfway open later
if slightly higher vacuum is desired, or
if sealant pressure is high. Under no
circumstances should the valves be closed
more than halfway.
7. On initial start-up, or if the pumps have been
sitting idle for several weeks, rotate the pumps
by hand several rotations to be sure they are
mechanically free.
8. Jog the motor to check the proper direction of
rotation. Facing the drive shaft of each pump:
The KLRC-40 and KLRC-75 liquid ring pumps
rotate counterclockwise. All other models
rotate clockwise.
INITIAL START-UP
1. Turn on the main power by closing the external
fusible disconnect switch or circuit breaker.
2. Check that all isolation and discharge valves (if
fitted) are in the proper position.
3.
Push the START button. The liquid ring pump
should start immediately.
4. Turn on the sealant water.
5.
Adjust the anti-cavitation valve to obtain best
vacuum level without cavitating the liquid ring
vacuum pump.
6.
Check that the sealant flow to the mechanical
seals is adequate.
7.
Check that the cooling water flow to the liquid
ring heat exchanger is adequate by checking
the sealant temperature.
8. Check the sealant level in the separator tank. If
necessary, add or remove fluid.
PROCEDURE FOR MINIMUM
SEALANT FLOW RATE
The requirements for sealant flow, as shown in
, are the maximum
GPM for once-through, partial and full recovery
systems. To determine the minimum quantity of
sealant flow required for a specific application,
proceed as follows: For once-through and partial
sealant recovery systems, with the pump on a
system and operating at the desired operating inlet
pressure, slowly decrease the flow of sealant liquid
until the inlet pressure begins to fluctuate, and then
gradually increase the flow until the pressure again
becomes steady. This is the setting to be used for
minimum seal flow as long as operating conditions
remain constant.
Cavitation occurs when there is localized boiling
of the sealant. This boiling action causes the
formation and collapse of vapor bubbles, and the
resultant shock forces cause erosion by tearing
out metal particles. The damage can be especially
severe in corrosive environments.
Содержание KLRC125
Страница 33: ...28 08 Reassembly Manual 4804 Rev E p n 004804 0000 Figure 8 2 Bearing Driver Tool ...
Страница 34: ...29 08 Reassembly Manual 4804 Rev E p n 004804 0000 Figure 8 3 Foot Alignment Tool ...
Страница 37: ...32 09 Troubleshooting Manual 4804 Rev E p n 004804 0000 NOTES ...
Страница 38: ...33 Parts Lists and Assembly Drawings Manual 4804 Rev E p n 004804 0000 CROSS SECTION KLRC 40 AND KLRC 75 ...
Страница 42: ...37 Parts Lists and Assembly Drawings Manual 4804 Rev E p n 004804 0000 CROSS SECTION KLRC 125 TO KLRC 525 ...