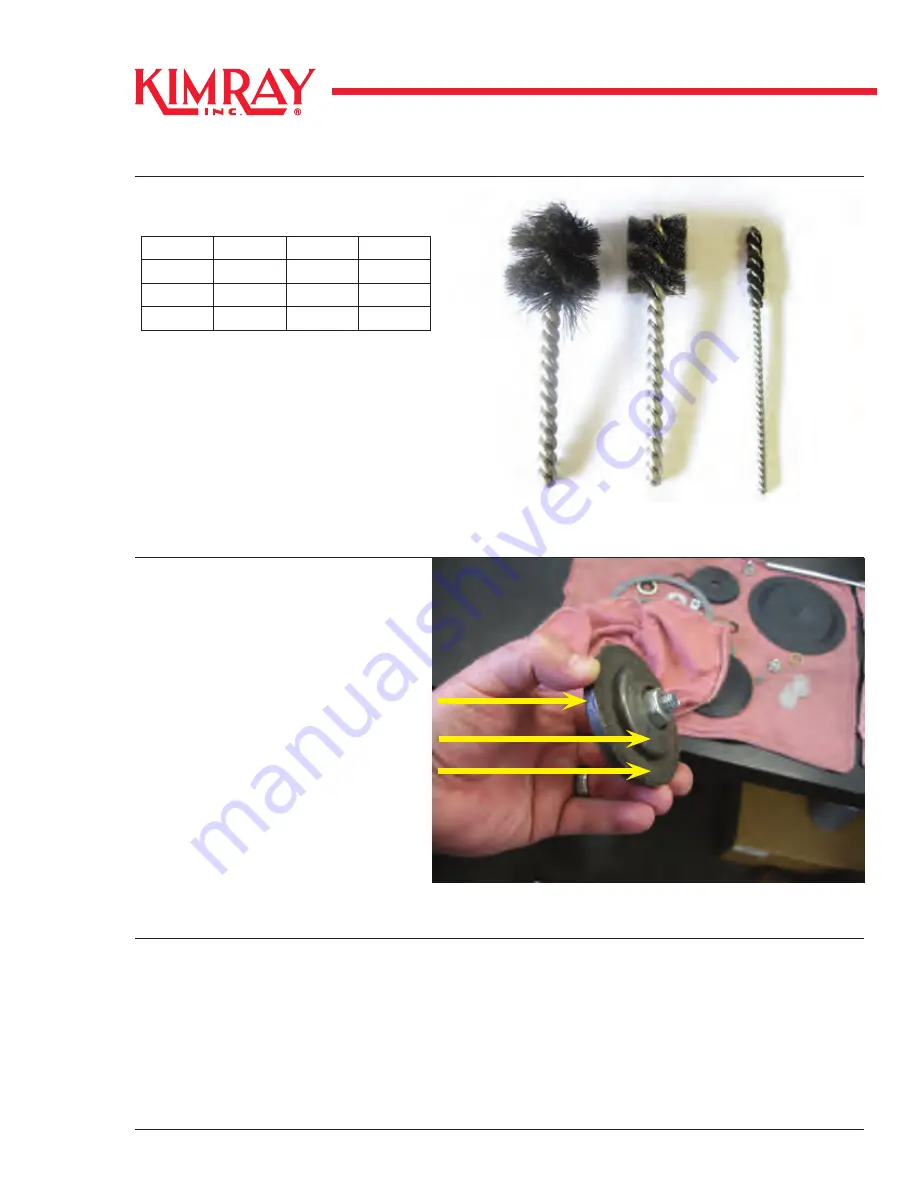
Page 11
PISTON BALANCED THROTTLING REPAIR MANUAL
CLEANING & INSPECTION
STEP 1
Cleaning
Diameter Wire Size Length Stem Dia.
1/4"
.004"
3-1/2"
1/8"
3/4"
.006"
3-1/2"
1/4"
1-1/4"
.008"
3-1/2"
1/4"
It is important to inspect all thread surfaces
for pits, debris and flat spots.
The listed wire brushes will allow you to
thoroughly clean virtually all threaded sur-
faces on Kimray products.
Often times the seat can-
not be removed and/or
replaced due to the length
of time in service. A seat
cleaning tool can be made
from a 3” ratio plug
(Fig. 1.1), a 2” ratio plug
(Fig. 1.2), and glue-on
sandpaper (Fig. 1.3). At-
tach the seat cleaning tool
to a speed wrench, make
flat contact and spin the
speed wrench to dress the
seat, inspect the seat for
scratches and repeat the
process as needed.
In the process of cleaning the valve there are a few essential areas that must be addressed:
1. All thread surfaces
2. Ensure all gasket material is removed.
3. Exterior free of solvents, debris and fluids if the product is to be re-painted.
4. Interior free of solvents, debris and fluids that may damage elastomers and affect O-ring / gasket seals.
www.kimray.com
Figure 1.1
Figure 1.2
Figure 1.3