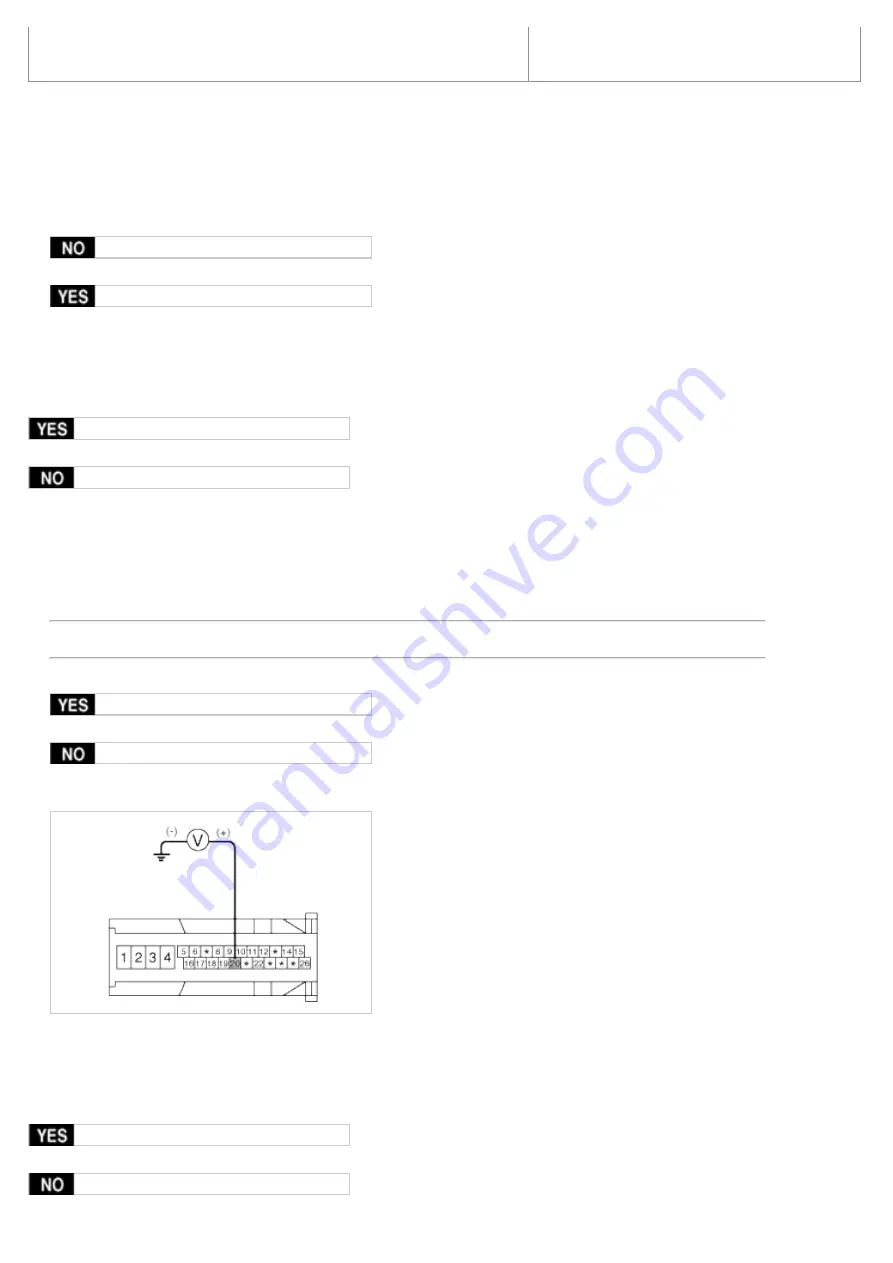
DTC is displayed, check the following probable cause. When the
problem is still occurring, replace the ABS control module.
b. Inoperative wheel speed sensor circuit
c. Inoperative hydraulic circuit for leakage
d. Inoperative HECU
INSPECTION PROCEDURES
DTC INSPECTION
1. Connect the Scan Tool with the data link connector and turn the ignition switch ON.
2. Verify that the system is operating to specifications.
Is the system operating to specifications?
▶
Check the wheel speed sensor circuit.
▶
Erase the DTC and recheck using Scan Tool.
CHECK THE WHEEL SPEED SENSOR CIRCUIT.
Refer to the DTC troubleshooting procedures.
Is the system operating to specifications?
▶
Check the stop lamp switch circuit.
▶
Repair or replace the wheel speed sensor.
CHECK THE STOP LAMP SWITCH CIRCUIT.
1. Check that stop lamp lights up when brake pedal is depressed and turns off when brake pedal is released.
2. Measure the voltage between terminal 20 of the ABS control module harness side connector and body ground
when brake pedal is depressed.
Specification: approximately B+
Is the voltage within specification?
▶
Check the hydraulic circuit for leakage.
▶
Repair the stop lamp switch. Repair an open in the wire between the ABS control module and the stop lamp
switch.
CHECK THE HYDRAULIC CIRCUIT FOR LEAKAGE.
Refer to the hydraulic lines.
Inspect leakage of the hydraulic lines.
Is the system operating to specifications?
▶
The problem is still occurring, replace the ABS control module.
Содержание Carnival 2007
Страница 1: ...CHAPTER 1 General Information ...
Страница 6: ...CHAPTER 2 Engine Mechanical System ...
Страница 21: ...Timing system Timing belt ...
Страница 22: ...2007 2 7L V6 GASOLINE COMPONENTS ...
Страница 32: ...Cylinder Head Assembly ...
Страница 33: ...2007 2 7L V6 GASOLINE COMPONENTS ...
Страница 34: ......
Страница 62: ...Engine And Transaxle Assembly ...
Страница 72: ...Cylinder Block 3LVWRQ DQG RQQHFWLQJ 5RG ...
Страница 73: ...2007 2 7L V6 GASOLINE COMPONENTS ...
Страница 74: ......
Страница 100: ...Cooling system ...
Страница 101: ...2007 2 7L V6 GASOLINE COMPONENTS ...
Страница 102: ......
Страница 111: ...5 Connect the radiator fan connectors A B LH RH 6 Install the transaxle oil cooler hoses A Refer to TR group ...
Страница 115: ...Lubrication system ...
Страница 116: ...2007 2 7L V6 GASOLINE COMPONENTS ...
Страница 127: ...Intake and Exhaust system ...
Страница 128: ...2007 2 7L V6 GASOLINE COMPONENTS ...
Страница 129: ......
Страница 130: ......
Страница 139: ...CHAPTER 3 Engine Electrical System ...
Страница 140: ...General information ...
Страница 152: ...Ignition System ...
Страница 158: ...Charging System ...
Страница 164: ...Alternator ...
Страница 165: ...2007 2 7L V6 GASOLINE COMPONENT ...
Страница 169: ...Battery ...
Страница 174: ...Starting System ...
Страница 178: ...Starter ...
Страница 179: ...2007 2 7L V6 GASOLINE COMPONENT ...
Страница 187: ...Starter Relay ...
Страница 189: ...CHAPTER 4 Emission Control System ...
Страница 190: ...2007 2 7L V6 GASOLINE SCHEMATIC DIAGRAM ...
Страница 191: ...General Information ...
Страница 194: ...5 Catalytic Converter Bank 2 ...
Страница 197: ...Crankcase Emission Control System ...
Страница 198: ...2007 2 7L V6 GASOLINE COMPONENTS ...
Страница 200: ...Positive Crankcase Ventilation PVC Valve ...
Страница 203: ...Evaporative Emission Control System ...
Страница 204: ...2007 2 7L V6 GASOLINE DESCRIPTION ...
Страница 206: ...Canister ...
Страница 209: ...Purge Control Solenoid Valve PCSV ...
Страница 212: ...Fuel Filler cap ...
Страница 213: ...2007 2 7L V6 GASOLINE DESCRIPTION ...
Страница 214: ...Exhaust Emission Control System ...
Страница 216: ...CVVT Continuously Variable Valve Timing System ...
Страница 219: ...CHAPTER 5 Fuel System ...
Страница 220: ...General Information ...
Страница 222: ...2007 2 7L V6 GASOLINE BASIC TROUBLESHOOTING BASIC TROUBLESHOOTING GUIDE CUSTOMER PROBLEM ANALYSIS SHEET ...
Страница 238: ...Engine Control System ...
Страница 246: ...Engine Control Module ECM ...
Страница 247: ...2007 2 7L V6 GASOLINE CIRCUIT DIAGRAM ...
Страница 248: ......
Страница 249: ......
Страница 250: ......
Страница 251: ......
Страница 264: ...Mass Air Flow Sensor MAFS ...
Страница 267: ...Manifold Absolute Pressure Sensor MAPS ...
Страница 270: ...Intake Air Temperature Sensor IATS ...
Страница 273: ...Engine Coolant Temperature Sensor ECTS ...
Страница 276: ...Accelerator Position Sensor APS ...
Страница 279: ...Specification Refer to SPECIFICATION ...
Страница 280: ...Heated Oxygen Sensor HO2S ...
Страница 282: ...Heater Resistance Ω 3 0 4 0Ω at 21 C 69 8 F WAVEFORM CIRCUIT DIAGRAM ...
Страница 284: ...4 Check that the resistance is within the specification Specification Refer to SPECIFICATION ...
Страница 285: ...CVVT Oil Temperature Sensor OTS ...
Страница 288: ...Knock Sensor KS ...
Страница 290: ...CIRCUIT DIAGRAM ...
Страница 291: ...Crankshaft Position Sensor CKPS ...
Страница 293: ...COMPONENT INSPECTION 1 Check signal waveform of CKPS and CMPS using a scantool Specification Refer to WAVE FORM ...
Страница 294: ...Camshaft Position Sensor CMPS ...
Страница 296: ...WAVEFORM CIRCUIT DIAGRAM ...
Страница 297: ...COMPONENT INSPECTION 1 Check signal waveform of CMPS and CKPS using a scantool Specification Refer to WAVE FORM ...
Страница 298: ...Injector ...
Страница 301: ...4 Check that the resistance is within the specification Specification Refer to SPECIFICATION ...
Страница 302: ...CVVT Oil Control Valve OCV ...
Страница 305: ...Variable Intake Solenoid Valve VIS ...
Страница 308: ...Electronic Throttle System ETS ...
Страница 314: ...Fuel Delivery System ...
Страница 315: ...2007 2 7L V6 GASOLINE COMPONENT LOCATION ...
Страница 316: ...2007 2 7L V6 GASOLINE FUEL PRESSURE TEST ...
Страница 317: ......
Страница 318: ......
Страница 319: ...Fuel Tank ...
Страница 322: ...Fuel Pump ...
Страница 325: ...CHAPTER 6 Automatic Transaxle System ...
Страница 326: ...General Information ...
Страница 330: ...Automatic Transaxle System ...
Страница 342: ...D 1ST gear ...
Страница 343: ...D 2ND gear ...
Страница 344: ...D 3nd gear ...
Страница 345: ...D 4th gear ...
Страница 346: ...Reverse ...
Страница 347: ......
Страница 349: ...Dynamic drive by sports mode ...
Страница 373: ......
Страница 374: ...Automatic Transaxle ...
Страница 375: ...2007 2 7L V6 GASOLINE COMPONENTS 1 ...
Страница 376: ...COMPONENTS 2 ...
Страница 377: ...COMPONENTS 3 ...
Страница 378: ...COMPONENTS 4 ...
Страница 379: ......
Страница 392: ...Valve Body System ...
Страница 393: ...Solenoid Valve ...
Страница 396: ......
Страница 397: ...VFS Variable Force Solenoid Valve ...
Страница 401: ...Automatic Transaxle ControlSystem ...
Страница 402: ...Input Speed Sensor ...
Страница 404: ......
Страница 406: ...Output Speed Sensor ...
Страница 408: ......
Страница 410: ...Transaxle Oil Temperature Sensor ...
Страница 413: ...Inhibiter Switch ...
Страница 418: ...CHAPTER 7 Manual Transaxle ...
Страница 419: ...General Information ...
Страница 423: ...Manual Transaxle System ...
Страница 425: ...2007 2 7L V6 GASOLINE COMPONENTS ...
Страница 442: ...CHAPTER 8 Driveshaft and Axle ...
Страница 443: ...General Information ...
Страница 447: ...BJ 28 RBA 250 g BJ 26 RBA 210 g TSJ 26 RBA 150 g UTJ II 25 CK 2 220 g ...
Страница 448: ...Driveshaft Assembly Front Driveshaft ...
Страница 449: ...2007 2 7L V6 GASOLINE COMPONENTS COMPONENTS ...
Страница 450: ...COMPONENTS ...
Страница 451: ......
Страница 465: ......
Страница 466: ...Front Axle Assembly ...
Страница 467: ...Front Hub Axle ...
Страница 468: ...2007 2 7L V6 GASOLINE COMPONENTS ...
Страница 475: ...Rear Axle Assembly ...
Страница 476: ...2007 2 7L V6 GASOLINE COMPONENTS ...
Страница 483: ...CHAPTER 9 Suspension System ...
Страница 484: ...General Information ...
Страница 505: ...Front Suspension System ...
Страница 506: ...2007 2 7L V6 GASOLINE COMPONENTS ...
Страница 507: ...Front Strut Assembly ...
Страница 508: ...2007 2 7L V6 GASOLINE COMPONENTS ...
Страница 515: ...Front Lower Arm ...
Страница 516: ...2007 2 7L V6 GASOLINE COMPONENTS ...
Страница 521: ...Front Stabilizer Bar ...
Страница 522: ...2007 2 7L V6 GASOLINE COMPONENTS ...
Страница 524: ...6 Remove both sides of the lower arm A mounting bolts B 7 Remove the engine mounting bolts A B ...
Страница 530: ...Rear Suspension System ...
Страница 531: ...2007 2 7L V6 GASOLINE COMPONENTS ...
Страница 532: ...Rear Shock Absorber ...
Страница 533: ...2007 2 7L V6 GASOLINE COMPONENTS ...
Страница 537: ...Rear Upper Arm ...
Страница 538: ...2007 2 7L V6 GASOLINE COMPONENTS ...
Страница 543: ...Rear Lower Arm ...
Страница 544: ...2007 2 7L V6 GASOLINE COMPONENTS ...
Страница 548: ...Rear Assist Arm ...
Страница 549: ...2007 2 7L V6 GASOLINE COMPONENTS ...
Страница 554: ...Trailing Arm ...
Страница 555: ...2007 2 7L V6 GASOLINE COMPONENTS ...
Страница 561: ...Rear Stabilizer Bar ...
Страница 562: ...2007 2 7L V6 GASOLINE COMPONENTS ...
Страница 567: ...Tires Wheels ...
Страница 568: ...Tires ...
Страница 571: ...Wheel ...
Страница 577: ...CHAPTER 10 Steering System ...
Страница 578: ...General Information ...
Страница 588: ...Steering Column Shaft ...
Страница 589: ...2007 2 7L V6 GASOLINE COMPONENTS ...
Страница 595: ...Hydraulic Power Steering System ...
Страница 596: ...2007 2 7L V6 GASOLINE COMPONENTS ...
Страница 597: ...Power Steering Gear ...
Страница 598: ...2007 2 7L V6 GASOLINE COMPONENT ...
Страница 614: ......
Страница 615: ...Power Steering Hoses ...
Страница 616: ...2007 2 7L V6 GASOLINE COMPONENTS Diesel Gasoline ...
Страница 617: ......
Страница 619: ... Diesel Gasoline 5 Remove the bracket of the return tube and hose Diesel Gasoline ...
Страница 621: ...Power Steering Oil Pump ...
Страница 622: ...2007 2 7L V6 GASOLINE COMPONENTS ...
Страница 632: ...Variouble Rack Stroke ...
Страница 634: ......
Страница 637: ...VRS Control Unit ...
Страница 639: ...VRS Operating Unit ...
Страница 641: ...VRS Switch ...
Страница 643: ...CHAPTER 11 Heating Ventilation Air Conditioning ...
Страница 644: ...Air Conditioning System ...
Страница 648: ...Air Conditioning System ...
Страница 651: ...2007 2 7L V6 GASOLINE REFRIGERATION CYCLE ...
Страница 652: ...2007 2 7L V6 GASOLINE COMPONENT LOCATION INDEX ENGINE ROOM INTERIOR ...
Страница 653: ......
Страница 657: ...Compressor ...
Страница 658: ...2007 2 7L V6 GASOLINE COMPONENT LOCATION COMPONENTS ...
Страница 659: ......
Страница 664: ...Compressor oil ...
Страница 666: ...Condenser ...
Страница 667: ...2007 2 7L V6 GASOLINE COMPONENT LOCATION ...
Страница 670: ...Refrigerant Line ...
Страница 671: ...2007 2 7L V6 GASOLINE COMPONENT LOCATION ...
Страница 673: ...A C Pressure Transducer ...
Страница 674: ...2007 2 7L V6 GASOLINE COMPONENT LOCATION ...
Страница 677: ...Evaporator Temperature Sensor ...
Страница 678: ...2007 2 7L V6 GASOLINE COMPONENT LOCATION ...
Страница 682: ...In car Sensor ...
Страница 683: ...2007 2 7L V6 GASOLINE COMPONENT LOCATION ...
Страница 686: ...Photo Sensor ...
Страница 687: ...2007 2 7L V6 GASOLINE COMPONENT LOCATION ...
Страница 690: ...Water Temperature Sensor ...
Страница 691: ...2007 2 7L V6 GASOLINE COMPONENT LOCATION ...
Страница 694: ...4 Installation is the reverse order of removal Take care that wire of water temperature sensor is not to be damaged ...
Страница 695: ...Ambient Sensor ...
Страница 696: ...2007 2 7L V6 GASOLINE COMPONENT LOCATION ...
Страница 699: ...Air Quality Sensor ...
Страница 700: ...2007 2 7L V6 GASOLINE COMPONENT LOCATION ...
Страница 703: ...Humidity Sensor ...
Страница 704: ...2007 2 7L V6 GASOLINE COMPONENT LOCATION ...
Страница 707: ...Heater ...
Страница 708: ...2007 2 7L V6 GASOLINE COMPONENT LOCATION COMPONENTS ...
Страница 709: ......
Страница 710: ......
Страница 711: ......
Страница 712: ......
Страница 716: ...Temperature Control Actuator ...
Страница 717: ...2007 2 7L V6 GASOLINE COMPONENT LOCATION ...
Страница 721: ...Model Control Actuator ...
Страница 722: ...2007 2 7L V6 GASOLINE COMPONENT LOCATION ...
Страница 725: ... Passenger s Driver s 5 Installation is the reverse order of removal ...
Страница 726: ...Fuel Fired Heater ...
Страница 727: ...2007 2 7L V6 GASOLINE COMPONENT LOCATION ...
Страница 735: ...Positive Temperature Coefficient Heater ...
Страница 738: ...Rear Heater ...
Страница 739: ...Rear Heater Unit ...
Страница 740: ...2007 2 7L V6 GASOLINE COMPONENT LOCATION COMPONENTS ...
Страница 741: ......
Страница 742: ......
Страница 745: ...Rear Blower Unit ...
Страница 747: ...Rear Temperature Control Actuator ...
Страница 750: ...Rear Mode Control Actuator ...
Страница 752: ...Rear Power Mosfet ...
Страница 754: ...Rear Control Panel ...
Страница 755: ...2007 2 7L V6 GASOLINE COMPONENT 1 Tail lamp ILL 2 IGN 2 3 Rear temp S W 4 Rear temp S W VENT 5 Rear temp S W B L ...
Страница 758: ...Blower ...
Страница 759: ...Blower Unit ...
Страница 760: ...2007 2 7L V6 GASOLINE COMPONENT LOCATION COMPONENTS ...
Страница 761: ......
Страница 763: ...Blower Motor ...
Страница 764: ...2007 2 7L V6 GASOLINE COMPONENT LOCATION ...
Страница 766: ...Blower Relay ...
Страница 767: ...2007 2 7L V6 GASOLINE COMPONENT LOCATION ...
Страница 769: ...Power Mosfet ...
Страница 770: ...2007 2 7L V6 GASOLINE COMPONENT LOCATION ...
Страница 772: ...4 Installation is the reverse order of removal ...
Страница 773: ...Climate Control Air Filtar ...
Страница 776: ...Intake Actuator ...
Страница 777: ...2007 2 7L V6 GASOLINE COMPONENT LOCATION ...
Страница 780: ...Controller ...
Страница 781: ...MANUAL ...
Страница 785: ...FULL AUTOMATIC ...
Страница 789: ...CHAPTER 12 Restraint ...
Страница 790: ...General information ...
Страница 798: ...2007 2 7L V6 GASOLINE COMPONENTS ...
Страница 799: ...COMPONENTS LOCATION DRIVER AIRBAG DAB PASSENGER AIRBAG PAB ...
Страница 800: ...SIDE AIRBAG SAB SEAT BELT PRETENSIONER BPT ...
Страница 801: ...SEAT BELT BUCKLE PRETENSIONER BUPT SIDE IMPACT SENSOR SIS ...
Страница 802: ...FRONT IMPACT SENSOR FIS ...
Страница 803: ...SUPPLEMENTAL RESTRAINT SYSTEM CONTROL MODULE SRSCM ...
Страница 806: ...Supplemental Restraint System Control Module SRSCM ...
Страница 807: ...2007 2 7L V6 GASOLINE CIRCUIT DIAGRAM 1 CIRCUIT DIAGRAM 2 ...
Страница 808: ...SRSCM CONNECTOR TERMINAL SRSCM HARNESS CONNECTOR ...
Страница 815: ...SRS Control Module SRSCM ...
Страница 817: ...2007 2 7L V6 GASOLINE COMPONENTS ...
Страница 820: ...Front Impact Sensor FIS ...
Страница 822: ...2007 2 7L V6 GASOLINE COMPONENTS ...
Страница 824: ...Side Impact Sensor SIS ...
Страница 826: ...2007 2 7L V6 GASOLINE COMPONENTS ...
Страница 829: ...Airbag Module ...
Страница 832: ...Drive Airbag DAB Module and Clock Spring ...
Страница 834: ...2007 2 7L V6 GASOLINE COMPONENTS ...
Страница 838: ...Passenger Airbag PAB Module ...
Страница 840: ...2007 2 7L V6 GASOLINE components ...
Страница 843: ...Curtain Airbag CAB Module ...
Страница 845: ...2007 2 7L V6 GASOLINE components ...
Страница 847: ...Side Airbag SAB Module ...
Страница 849: ...2007 2 7L V6 GASOLINE components ...
Страница 852: ...Seat Belt Pretensioner BPT ...
Страница 854: ...2007 2 7L V6 GASOLINE components ...
Страница 856: ...Seat Belt Buckle Pretensioner ...
Страница 858: ...2007 2 7L V6 GASOLINE components ...
Страница 860: ...CHAPTER 13 Brake System ...
Страница 861: ...General information ...
Страница 868: ...Brake System ...
Страница 874: ...Brake Booster ...
Страница 875: ...2007 2 7L V6 GASOLINE COMPONENTS ...
Страница 879: ...Master Cylinder ...
Страница 880: ...2007 2 7L V6 GASOLINE COMPONENTS ...
Страница 886: ...Brake Line ...
Страница 887: ...2007 2 7L V6 GASOLINE COMPONENT ...
Страница 890: ...Brake Pedal ...
Страница 891: ...2007 2 7L V6 GASOLINE COMPONENTS COMPONENTS ADJUSTABLE PEDAL ...
Страница 892: ......
Страница 895: ......
Страница 896: ...Front Disc Brake ...
Страница 897: ...2007 2 7L V6 GASOLINE COMPONENTS ...
Страница 898: ......
Страница 903: ...Rear Disc Brake ...
Страница 904: ...2007 2 7L V6 GASOLINE COMPONENTS ...
Страница 909: ...Parking Brake System Parking Brake Assembly ...
Страница 910: ...2007 2 7L V6 GASOLINE COMPONENTS 1 COMPONENTS 2 ...
Страница 911: ...COMPONENTS 3 ...
Страница 912: ......
Страница 921: ...Parking Brake Switch ...
Страница 923: ...ABS Anti lock Brake System ...
Страница 924: ...2007 2 7L V6 GASOLINE ABS CIRCUIT DIAGRAM 1 ABS CIRCUIT DIAGRAM 2 ...
Страница 933: ...2007 2 7L V6 GASOLINE COMPONENTS ...
Страница 948: ...ABS Control Unit ...
Страница 949: ...2007 2 7L V6 GASOLINE COMPONENTS ...
Страница 952: ...Front Wheel Speed Sensor ...
Страница 953: ...2007 2 7L V6 GASOLINE COMPONENTS ...
Страница 956: ...Rear Wheel Speed Sensor ...
Страница 957: ...2007 2 7L V6 GASOLINE COMPONENTS ...
Страница 959: ...a V_low 0 44 V 0 63 V b V_high 0 885 V 1 26 V c Frequency range 1 2 500 Hz ...
Страница 960: ...EBFD Electronic Brake Force Distribution ...
Страница 962: ...ESP Electronic Stability Program System ...
Страница 963: ...2007 2 7L V6 GASOLINE ESP circuit DIAGRAM 1 ESP circuit DIAGRAM 2 ...
Страница 964: ...ESP circuit DIAGRAM 3 ...
Страница 976: ...2007 2 7L V6 GASOLINE COMPONENTS ...
Страница 978: ...Steering Angle Sensor ...
Страница 980: ...CIRCUIT DIAGRAM YAW RATE LATERAL G SENSOR ...
Страница 981: ...ESP OFF Switch ...
Страница 983: ...Yaw rate and Lateral G Sensor ...
Страница 985: ...Steering Angle Sensor ...
Страница 989: ...CHAPTER 14 Body Interior and Exterior ...
Страница 990: ...General information ...
Страница 992: ...09880 4F000 Hogring clip installer Installation of the hogring clip ...
Страница 995: ...Exterior ...
Страница 996: ...Fender ...
Страница 998: ...Hood ...
Страница 1006: ......
Страница 1007: ...Taligate ...
Страница 1020: ......
Страница 1021: ...Front Door ...
Страница 1022: ...2007 2 7L V6 GASOLINE COMPONENTS ...
Страница 1034: ...Rear Door ...
Страница 1035: ...2007 2 7L V6 GASOLINE COMPONENTS ...
Страница 1046: ...Body Side Moldings ...
Страница 1050: ...Mirror ...
Страница 1051: ...2007 2 7L V6 GASOLINE COMPONENTS ...
Страница 1054: ...Interior ...
Страница 1055: ...Console ...
Страница 1056: ...2007 2 7L V6 GASOLINE COMPONENTS ...
Страница 1057: ......
Страница 1061: ...Crash Pad ...
Страница 1062: ...2007 2 7L V6 GASOLINE COMPONENTS LHD RHD ...
Страница 1063: ......
Страница 1076: ... RHD ...
Страница 1078: ...d Enter the anti theft code for the radio then enter the customer s radio station presets ...
Страница 1079: ...Roof Trim ...
Страница 1080: ...2007 2 7L V6 GASOLINE COMPONENTS ...
Страница 1084: ......
Страница 1085: ...Interior Trim ...
Страница 1086: ...2007 2 7L V6 GASOLINE COMPONENTS ...
Страница 1093: ......
Страница 1094: ...Windshield Glass ...
Страница 1095: ...2007 2 7L V6 GASOLINE COMPONENTS ...
Страница 1102: ...Bumper ...
Страница 1103: ...Front Bumper ...
Страница 1105: ......
Страница 1106: ...Rear Bumper ...
Страница 1108: ......
Страница 1109: ...Seat Power Seat ...
Страница 1110: ...2007 2 7L V6 GASOLINE COMPONENT LOCATION ...
Страница 1111: ...Front Seat ...
Страница 1112: ...2007 2 7L V6 GASOLINE COMPONENTS ...
Страница 1113: ...Rear Seat ...
Страница 1123: ......
Страница 1124: ...2007 2 7L V6 GASOLINE COMPONENTS SECONDARY SEAT THIRD SEAT ...
Страница 1125: ......
Страница 1134: ...3 Remove the seat assembly A 4 Installation is the reverse of removal RECLINER COVER REPLACEMENT 1 Remove the recliner cover A ...
Страница 1136: ...4 Remove the hogring clips A 5 Remove the headrest guide A 6 Remove the frame A ...
Страница 1140: ...Seat Belt ...
Страница 1141: ...Front Seat Belt ...
Страница 1149: ...3 Installation is the reverse of removal ...
Страница 1150: ...CHAPTER 15 Body Electrical System ...
Страница 1151: ...General information ...
Страница 1157: ...Audio ...
Страница 1158: ...2007 2 7L V6 GASOLINE COMPONENT LOCATION ...
Страница 1160: ...CHART 1 ...
Страница 1161: ......
Страница 1162: ...CHART 2 CHART 3 ...
Страница 1163: ...CHART 4 ...
Страница 1164: ......
Страница 1165: ...CHART 5 ...
Страница 1166: ......
Страница 1167: ...CHART 6 ...
Страница 1168: ...CHART 7 CHART 8 ...
Страница 1169: ...CHART 9 ...
Страница 1171: ...Audio Unit ...
Страница 1172: ...2007 2 7L V6 GASOLINE COMPONENT LOCATION AM FM CDP M445 AM FM Cassette MP3 M455 ...
Страница 1173: ...AM FM Cassette 6CDC MP3 M465 ...
Страница 1174: ......
Страница 1177: ...Speakers ...
Страница 1181: ...Antenna ...
Страница 1186: ...8 If there is continuity replace the antenna cable ...
Страница 1187: ...Audio Remote Control ...
Страница 1188: ...2007 2 7L V6 GASOLINE CIRCUIT DIAGRAM ...
Страница 1190: ...Multifunction Switch ...
Страница 1191: ...2007 2 7L V6 GASOLINE COMPONENT LOCATION ...
Страница 1192: ......
Страница 1195: ...4 Remove the wiper switch A after disconnecting the connector and pin B LHD RHD 5 Installation is the reverse of removal ...
Страница 1196: ...Horn ...
Страница 1197: ...2007 2 7L V6 GASOLINE COMPONENT LOCATION ...
Страница 1199: ...Keyless Entry And Burglar Alarm ...
Страница 1201: ...2007 2 7L V6 GASOLINE COMPONENT LOCATION ...
Страница 1208: ...Transmitter ...
Страница 1210: ...Body Control Module BCM ...
Страница 1253: ...4 Installation is the reverse of removal ...
Страница 1254: ...IMS Integrated Memory ...
Страница 1255: ...IMS Integrated Memory Module ...
Страница 1257: ...IMS Integrated Memory Power Seat Control ...
Страница 1258: ...2007 2 7L V6 GASOLINE CIRCUIT DIAGRAM ...
Страница 1264: ...IMS Integrated Memory Control Switch ...
Страница 1266: ...Seat Electrical ...
Страница 1267: ...Power Seat Motor ...
Страница 1271: ...Power Seat Motor Switch ...
Страница 1273: ...Seat Heater Switch ...
Страница 1275: ...Seat Heater Module ...
Страница 1277: ...Seat Heater ...
Страница 1279: ...Fuel Filler Door ...
Страница 1280: ...2007 2 7L V6 GASOLINE COMPONENT LOCATION ...
Страница 1281: ...Fuel Filler Door Release Actuator ...
Страница 1283: ...Fuel Filler Door Open Switch ...
Страница 1285: ...Fuses and Relays ...
Страница 1286: ...2007 2 7L V6 GASOLINE COMPONENT LOCATION ...
Страница 1287: ...Relay Box Engine Compartment ...
Страница 1288: ...2007 2 7L V6 GASOLINE COMPONENTS FAM FRONT AREA MODULE ...
Страница 1289: ......
Страница 1291: ......
Страница 1293: ...Relay Box Passenger Compartment ...
Страница 1294: ...2007 2 7L V6 GASOLINE COMPONENTS IPM INSTRUMENT PANEL MODULE ...
Страница 1295: ...RAM REAR AREA MODULE ...
Страница 1296: ......
Страница 1297: ......
Страница 1300: ...ICM Integrated Circuit Module Relay Box ...
Страница 1303: ...Indicators and Gauges ...
Страница 1304: ...2007 2 7L V6 GASOLINE COMPONENT LOCATION ...
Страница 1305: ...Instrument Cluster ...
Страница 1306: ...2007 2 7L V6 GASOLINE COMPONENTS ...
Страница 1313: ...Power Door Locks ...
Страница 1314: ...2007 2 7L V6 GASOLINE COMPONENT LOCATION ...
Страница 1320: ...4 Select option 02 CURRENT DATA 5 To check the Input Value of door lock switch in force mode select option 05 ACTUATION TEST ...
Страница 1321: ......
Страница 1322: ...Power Sliding Door System ...
Страница 1330: ...2007 2 7L V6 GASOLINE COMPONENT LOCATION ...
Страница 1337: ...Power Sliding Door Unit ...
Страница 1343: ...Power Sliding Door Control Module ...
Страница 1345: ...Power Sliding Door Buzzer ...
Страница 1347: ...Detent Switch ...
Страница 1350: ...Latch Switch ...
Страница 1353: ...Power Sliding Door Switch ...
Страница 1358: ...Power Door Mirrors ...
Страница 1359: ...2007 2 7L V6 GASOLINE COMPONENT LOCATION ...
Страница 1360: ...Power Door Mirror Actuator ...
Страница 1362: ......
Страница 1363: ...Door Mirror Folding Switch ...
Страница 1365: ......
Страница 1366: ...Door Tail Gate System ...
Страница 1371: ...2007 2 7L V6 GASOLINE COMPONENT LOCATION ...
Страница 1383: ...Anti Pinch Strip ...
Страница 1386: ...PTG Power Latch ...
Страница 1389: ...PTG Switch ...
Страница 1393: ...Power Windows ...
Страница 1394: ...2007 2 7L V6 GASOLINE COMPONENT LOCATION ...
Страница 1395: ...Power Window Motor ...
Страница 1401: ...Power Window Switch ...
Страница 1404: ...Windshield Deicer ...
Страница 1406: ...2007 2 7L V6 GASOLINE COMPONENT LOCATION ...
Страница 1408: ...Windshield Deicer Switch ...
Страница 1410: ...Windshield Deicer Timer ...
Страница 1412: ...Rear Glass Defogger ...
Страница 1413: ...Rear Glass Defogger Printed Heater ...
Страница 1416: ...scrape away excess deposits with a knife after the paint has completely dried Allow 24 hours ...
Страница 1417: ...Rear Glass Defogger Switch ...
Страница 1419: ...Rear Glass Defogger Timer ...
Страница 1421: ...Windshield Wiper Washer ...
Страница 1422: ...2007 2 7L V6 GASOLINE COMPONENT LOCATION ...
Страница 1423: ...Windshield Wiper Washer Switch ...
Страница 1425: ... RHD WIPER SWITCH WASHER SWITCH ...
Страница 1426: ...Front Wiper Motor ...
Страница 1427: ...2007 2 7L V6 GASOLINE COMPONENT LOCATION ...
Страница 1430: ...Front Washer Motor ...
Страница 1432: ......
Страница 1433: ...Rain Sensor ...
Страница 1438: ...Rear Wiper Washer ...
Страница 1439: ...Rear Wiper Motor ...
Страница 1442: ...Rear Washer Switch ...
Страница 1444: ...Rear Washer Motor ...
Страница 1446: ...Electro Chromic Inside Rear View Mirror ...
Страница 1449: ...Sun Roof ...
Страница 1450: ...2007 2 7L V6 GASOLINE COMPONENT LOCATION ...
Страница 1451: ...Sun Roof Assembly ...
Страница 1452: ...2007 2 7L V6 GASOLINE COMPONENTS ...
Страница 1460: ......
Страница 1461: ...Sun Roof Switch ...
Страница 1463: ...Sun Roof Motor ...
Страница 1465: ...Lighting System ...
Страница 1466: ...2007 2 7L V6 GASOLINE COMPONENT LOCATION ...
Страница 1468: ...Head Lamps ...
Страница 1471: ...1 Turn the low beam on with driver The cut off line should be projected in the allowable range shaded region ...
Страница 1472: ...2 Turn the front fog lamp on with driver The cut off line should be projected in the allowable range shaded region ...
Страница 1473: ...Turn Signal Lamp ...
Страница 1475: ...3 Remove the socket in a counterclockwise direction 4 Replace the bulb ...
Страница 1476: ...Room Lamp ...
Страница 1478: ...Overhead Console Lamp ...
Страница 1480: ...Courtesy Lamp ...
Страница 1482: ...Front Fog Lamps ...
Страница 1484: ...Rear Fog Lamp ...
Страница 1486: ...License Lamps ...
Страница 1488: ...High Mounted Stop Lamp ...
Страница 1490: ...Auto Lighting System ...
Страница 1492: ...2007 2 7L V6 GASOLINE COMPONENT LOCATION ...
Страница 1493: ...Auto Light Switch ...
Страница 1495: ...Auto Light Sensor ...
Страница 1497: ...Daytime Running Lights ...
Страница 1498: ...Daytime Running Lights Control Module ...
Страница 1500: ...Immobilizer System ...
Страница 1501: ...2007 2 7L V6 GASOLINE CIRCUIT DIAGRAM ...
Страница 1502: ......
Страница 1505: ...c The antenna coil sends transponder signal to the SMARTRA It is located directly in front of the steering handle lock ...
Страница 1509: ... 1 PCM ECM learnt status ...
Страница 1510: ......
Страница 1513: ......
Страница 1514: ... If the wrong password is entered wait 10 seconds then start again from step 1 2 User password changing ...
Страница 1520: ......
Страница 1521: ...Immobilizer Control Unit ...
Страница 1523: ...Antenna Coil ...
Страница 1525: ...Trip Computer ...
Страница 1528: ......
Страница 1531: ...Rear Parking Assist System ...
Страница 1532: ...Rear Parking Assist System Control Unit ...
Страница 1534: ...2007 2 7L V6 GASOLINE COMPONENT LOCATION ...
Страница 1540: ...Parking Assist Sensor ...
Страница 1544: ...Buzzer ...
Страница 1546: ...Ignition Switch Assembly ...
Страница 1548: ...6 Remove the key lock cylinder C after pushing lock pin B with key ACC 7 Installation is the reverse of removal procedure ...
Страница 1549: ...Multiplex Communication ...
Страница 1550: ...Driver Door Module ...
Страница 1555: ...Assist Door Module ...
Страница 1556: ...2007 2 7L V6 GASOLINE COMMUNICATION DIAGRAM ...
Страница 1561: ...CHAPTER 16 Clutch System ...
Страница 1563: ......
Страница 1564: ...Clutch Cover And Disc ...
Страница 1565: ...2007 2 7L V6 GASOLINE COMPONENTS ...
Страница 1569: ...Clutch Master Cylinder ...
Страница 1572: ...Clutch Pedal ...