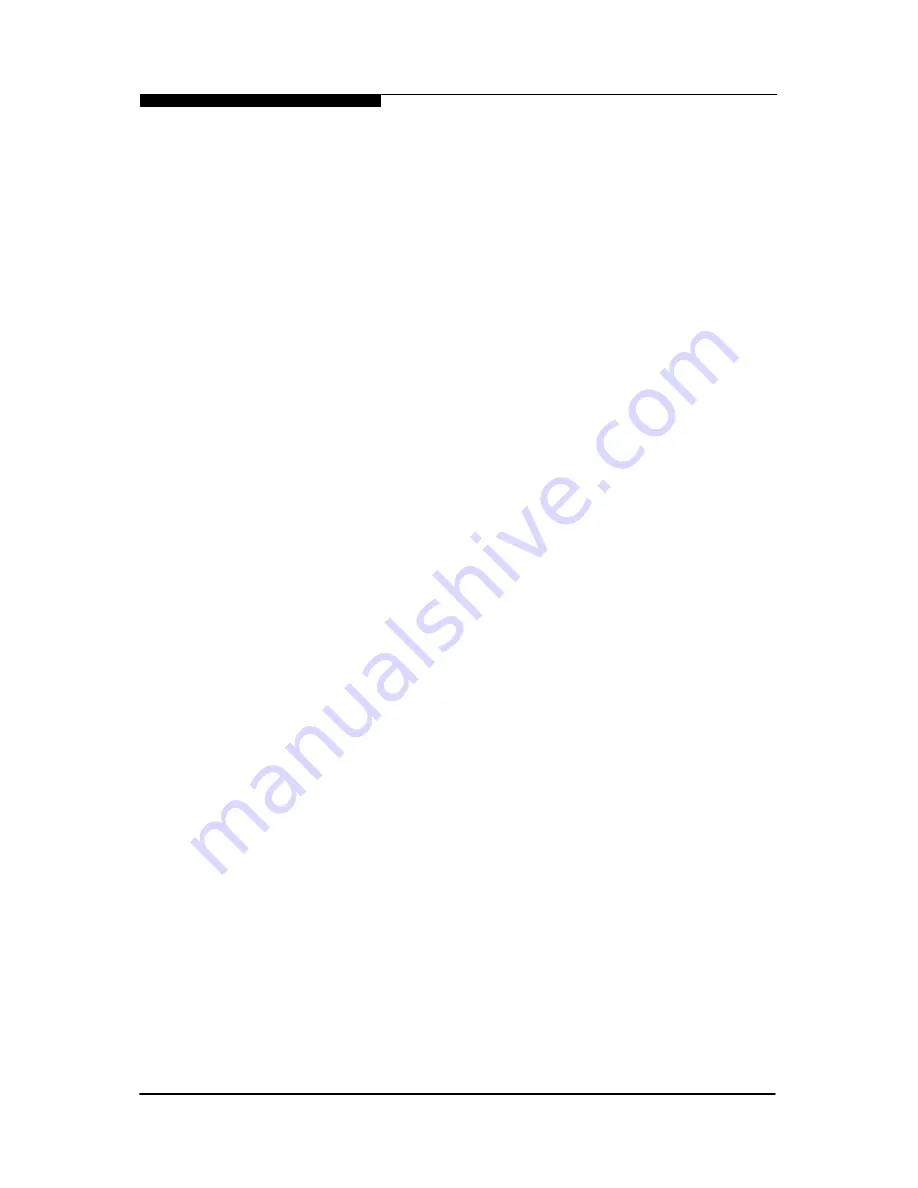
ii)
Gain access (Section 7.2)
iii)
Remove the push on connectors to the gas low pressure switch taking
note of the correct positions.
iv)
Unscrew the gas low pressure switch from the brass holder.
v)
Reassemble (Section 7.3)
7.5
GAS ORIFICE
(Fig 5.7.3 item 87)
i)
Isolate the appliance (Section 7.1)
ii)
Gain access (Section 7.2)
iii)
Unscrew and remove the brass plug from the gas outlet block.
iv)
Remove the rubber seal from the injector housing.
v)
Insert a flat blade screwdriver into the exposed hole and unscrew the gas injector.
vi)
Check the injector is the correct size for the boiler size and fuel type.
vii)
Reassemble (Section 7.3)
NB: Ensure that the injector is screwed fully home
viii)
Reset the gas pressure (See Section 4 - Commissioning)
7.6
SPARK IGNITION/FLAME DETECTION ELECTRODE
(Fig. 5.7.2 item 50)
i)
Isolate the appliance (Section 7.1)
ii)
Gain access (Section 7.2)
iii)
Remove the pull off HT lead to the spark ignition electrode.
iv)
Remove the burner head (Section 7.7 steps iv to vi).
v)
Undo the screws to the spark ignition electrode flange located on the burner
head and withdraw the spark ignition electrode.
vi)
Reassemble (Section 7.3)
NB:
When reassembling inspect the gasket for damage and replace if
necessary. With the new spark ignition electrode in place it is essential to
ensure the gap between the tip of the electrode and the burner surface is
4 mm. Distance above or below 4 mm will affect the ignition performance.
If necessary gently bend the electrode, taking care not to damage the
ceramic insulator.
7.7
BURNER HEAD & BURNER
(Fig. 5.7.2 items 47 & 45)
i)
Isolate the appliance (Section 7.1)
ii)
Gain access (Section 7.2)
iii)
Remove the pull off HT lead to the spark ignition/flame detection electrode head.
iv)
Remove the four screws retaining the access panel (Fig. 5.7.4 item 1) and
remove the access panel from the top of the cabinet.
iv)
Remove the two allen screws fixing the flange gas/air mixture pipe connection to
the burner head.
v)
Remove the five allen screws fixing the burner head to the top of the heat
exchanger.
vi)
Withdraw the burner & burner head from the top of the heat exchanger through
the access panel opening in the top of the cabinet.
vii)
Unscrew the burner from the burner head taking care not to damage the burner
mesh.
vi)
Reassemble (Section 7.3)
NB:
When reassembling inspect any gaskets for damage and replace if
necessary. Set the spark gas as detailed in Section 7.6
vii)
Reset the gas rate (see Section 4 - Commissioning)
WD51/2/1997 Chapter 7 : Replacement Of Parts
The Keston 170 Condensing Boilers
Installation & Servicing Instructions
Page : 45