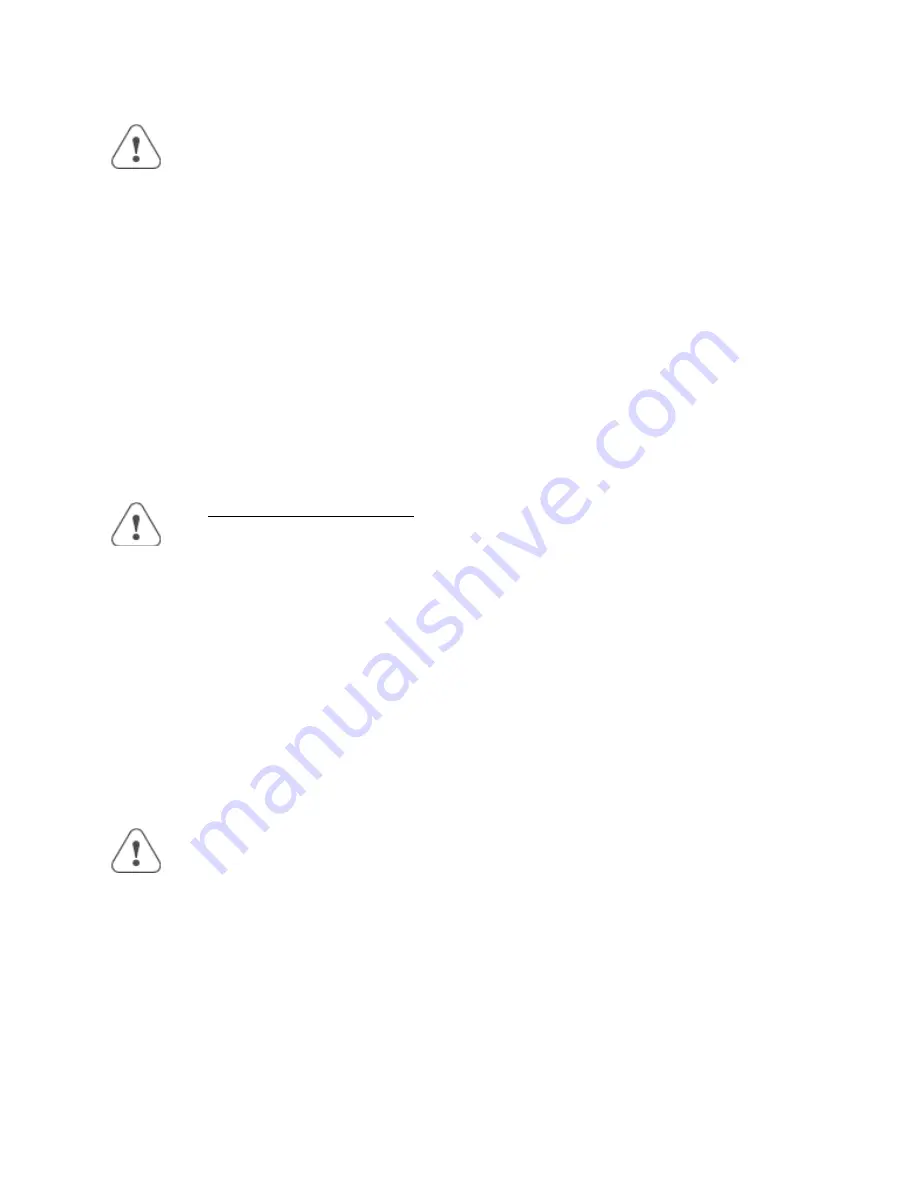
Caution
Supply Voltage
Note: The 24 VDC output from
some controllers may not have enough current to power the
MMI8000.
Caution Wire
Routing
Wire lengths should be minimized (Maximum 1600’ (500 m) shielded, 1000’ (300 m)
unshielded).
Wires should be run in pairs with a neutral or common paired with a hot or
signal line.
If wiring is to be exposed to lightning or surges, use appropriate surge
suppression devices.
Keep AC, high energy, and rapidly switching DC wiring separate from
signal wires.
Equip ungrounded DC supplies with a resistor and capacitor in parallel to earth ground. This
provides a path for static and high frequency dissipation. Typical values to use are 1MOhm and
4700pF.
Connection
To make a connection, strip about 3/8” of insulation off the end of the wire, turn the connector
screw counterclockwise until the gap is wide open, insert the wire all the way in, and turn the
screw clockwise until it’s tight.
Connect positive DC line to the ‘+24V’ terminal and the DC ground to the
‘0V‘ terminal.
2.2.2 Grounding Requirements
Chassis ground must be used. DC ground is not directly coupled to Earth ground internally. It is
preferable not to ground DC negative return to chassis ground as poor site earths can introduce
noise into a system, but if necessary an earth connection should be made, from the power supply
return point to the central star earth point. Ground conductors should be as short and as large in
size as possible. The conductors must always be large enough to carry the maximum short circuit
current of the path being considered. Ground conductors should be connected to a tree from a
central star earth ground point. This ensures that no ground conductor carries current from any
other branch.
2.2.3 CE Requirements
To make an MMI8000 comply with EMC directives, and to reduce susceptibility to electrical
interference, a separate #14 AWG ground wire should be taken to the chassis ground terminal of the
power connector. This ground connection should be run directly to the central star earth connection
point (as recommended in most Installation Instructions).
2.2.4 Safety Guidelines
This section presents recommended installation practices, and procedures. Since no two
applications are identical, these recommendations should be considered as guidelines.
Hardware
Considerations
WARNING!
The system designer should be aware that devices in Controller systems could fail and thereby
create an unsafe condition. Furthermore, electrical interference in an operator interface, such as
an MMI8000, can lead to equipment start-up, which could result in property damage and/or
physical injury to the equipment operator.
If you, or your company, use any programmable control systems that require an operator or
attendant, you should be aware that this potential safety hazard exists and take appropriate
precautions. Although the specific design steps depend on your particular application, the
following precautions generally apply to installation of solid-state programmable control devices.
In addition, these precautions conform to the guidelines for installation of Controllers as
recommended in the NEMA ICS 3-304 Control Standards.
Programming
Considerations
To conform with ICS Safety Recommendations, checks should be placed in the controller to
ensure that all writable registers that control critical parts of plant or machinery have limit checks